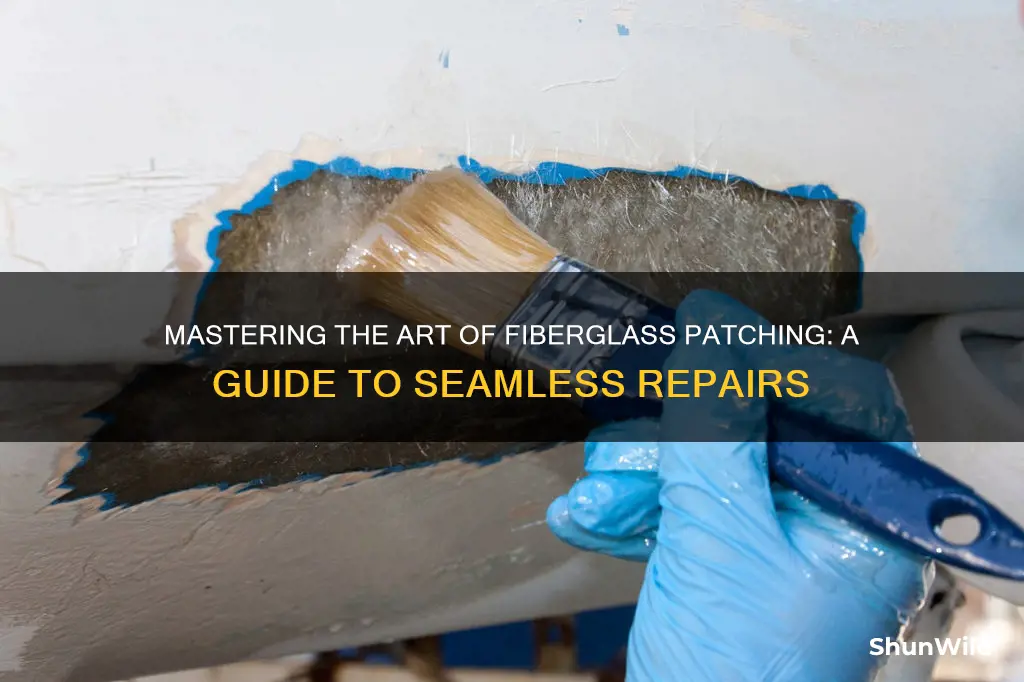
Blending a fiberglass patch seamlessly onto a boat can be a challenging but rewarding task. This guide will provide a step-by-step approach to ensure a successful repair. By following these instructions, you can effectively integrate a fiberglass patch onto your boat, restoring its structural integrity and appearance. The process involves careful preparation, precise application of materials, and meticulous finishing to create a nearly invisible repair. With the right techniques and attention to detail, you can achieve a professional-looking result that blends the patch seamlessly with the original fiberglass surface.
What You'll Learn
- Prepare the Surface: Clean and roughen the area for a strong bond
- Mix Resin and Fiber: Follow ratios for a strong, flexible patch
- Apply Adhesive: Use a suitable adhesive for fiberglass bonding
- Position and Secure: Align and clamp the patch for precise placement
- Finish and Sand: Smooth the surface and sand for a seamless blend
Prepare the Surface: Clean and roughen the area for a strong bond
When preparing the surface for a fiberglass patch, the goal is to ensure a strong and durable bond between the new material and the existing structure of the boat. This process begins with thorough cleaning and surface preparation, which are crucial steps to guarantee the long-term success of the repair.
Start by thoroughly cleaning the area where the patch will be applied. Use a mild detergent or a specialized marine cleaner to remove any dirt, grime, or old paint. Rinse the surface with fresh water to ensure no residue remains. It's important to work in a well-ventilated area or outdoors to avoid inhaling any fumes from the cleaning agents. For stubborn stains or old paint, you may need to use a scraper or a wire brush to carefully remove the material, being cautious not to damage the surrounding fiberglass.
Once the cleaning is complete, the surface needs to be roughened to provide a better adhesion surface for the fiberglass patch. This can be achieved by using sandpaper or a power tool like a random orbit sander. Start with a higher grit (e.g., 120-180 grit) to create a coarse surface, then gradually switch to a finer grit (e.g., 220-320 grit) to smooth out any rough patches. The goal is to create a texture that is slightly rough to the touch but not so rough that it causes damage to the new fiberglass. Ensure you follow the direction of the existing fiberglass weave to avoid creating a visible pattern in the new patch.
After sanding, inspect the surface to ensure it is clean and free of any debris. Use a damp cloth to wipe away any dust or sand particles, and then allow the area to dry completely. This preparation process is essential to create a strong bond between the old and new fiberglass, ensuring the patch blends seamlessly with the surrounding structure.
Exploring Helene: Boat Trip from Roatan
You may want to see also
Mix Resin and Fiber: Follow ratios for a strong, flexible patch
When preparing to blend resin and fiber for a fiberglass patch, it's crucial to follow the correct ratios to ensure a strong and flexible repair. The key to a successful patch lies in the precise mixing of these two components. The resin acts as a binding agent, while the fiber provides the necessary strength and reinforcement.
The ideal ratio for mixing resin and fiber is typically around 3:1 by volume. This means for every three parts of resin, you should use one part of fiber. This ratio is a general guideline and may vary slightly depending on the specific type of resin and fiber being used. Always refer to the manufacturer's instructions for the best results.
To begin the mixing process, ensure you have a clean and well-ventilated workspace. Gather your materials, including the chosen resin, fiber glass cloth or mat, and any necessary catalysts or hardeners. Catalysts are often added to the resin to initiate the curing process, so make sure to include them in your mix.
Carefully measure the resin and fiber according to the desired ratio. Accuracy is essential here; using too much or too little of either component can affect the final outcome. Pour the measured resin into a clean container, ensuring it is free from any contaminants. Then, gently add the fiber to the resin, allowing it to saturate and blend evenly. It's important to mix thoroughly to ensure a homogeneous mixture.
Stir the mixture continuously as you add the fiber to ensure an even distribution. You can use a wooden or plastic spatula for this process. If you're using a catalyst, add it to the resin before mixing to avoid contamination. Always follow the manufacturer's instructions for the correct addition and mixing times. Once the mixture is well-blended, it's ready for application.
Boat Cleaning: A Lucrative Business Opportunity?
You may want to see also
Apply Adhesive: Use a suitable adhesive for fiberglass bonding
When blending in a fiberglass patch on a boat, the adhesive you choose is crucial for a strong and durable bond. Fiberglass is a composite material that requires a specific type of adhesive to ensure proper adhesion and long-term performance. The goal is to create a seamless transition between the patch and the existing fiberglass structure, making it nearly impossible to distinguish where the patch ends and the original material begins.
Start by cleaning the surface of the boat where the patch will be applied. Remove any dirt, grease, or old adhesive residue. A clean and smooth surface is essential for optimal bonding. You can use a mild detergent and water solution to wash the area, ensuring no soap residue remains. Rinse thoroughly and allow the surface to dry completely before proceeding.
Next, select an appropriate adhesive for fiberglass bonding. There are several types of adhesives available, including epoxy resins, urethanes, and specialized fiberglass repair adhesives. For most boat repair applications, a two-part epoxy adhesive is commonly used. These epoxy systems provide excellent strength and flexibility, making them ideal for bonding fiberglass. Ensure you follow the manufacturer's instructions for mixing and applying the adhesive.
Apply the adhesive to the fiberglass patch and the prepared boat surface. Start by brushing the adhesive onto the patch, ensuring full coverage. Allow the adhesive to set for a short period, typically as per the manufacturer's guidelines, which could be a few minutes to an hour, depending on the product. This initial setting time is crucial to ensure the patch remains in place during the blending process.
Once the adhesive is set, carefully position the patch onto the boat's surface, aligning it with the surrounding fiberglass. Use a trowel or a similar tool to smooth out any air bubbles and ensure a tight bond. Press firmly and hold the patch in place for the recommended time, usually several minutes, to allow the adhesive to cure further. This process requires patience and a steady hand to achieve a seamless blend.
Remember, the key to a successful fiberglass patch repair is proper surface preparation and the use of an appropriate adhesive. Take your time with each step, and don't rush the process. With careful application and attention to detail, you can effectively blend the patch into the boat's original fiberglass structure, ensuring a professional-looking finish.
Lake Texoma Boat Ramps: Open Access for Sailors
You may want to see also
Position and Secure: Align and clamp the patch for precise placement
When preparing to blend a fiberglass patch onto a boat, the first crucial step is positioning and securing the patch for precise placement. This process ensures that the repair is not only aesthetically pleasing but also structurally sound. Here's a detailed guide on how to achieve this:
- Clean and Prepare the Surface: Before you begin, ensure the area around the damage is clean and free of any debris or old fiberglass. Use a wire brush or a scraper to remove any loose fibers or old material. This step is essential to create a strong bond between the existing structure and the new patch.
- Measure and Mark: Carefully measure the dimensions of the damage and mark the corresponding areas on the boat's surface. Accurate measurements will guide your alignment process. If the damage is extensive, consider taking detailed photos of the area to ensure you don't miss any crucial details.
- Align and Position: Now, it's time to carefully align the fiberglass patch over the marked area. Ensure that the patch is centered and matches the contour of the surrounding surface. Use a straight edge or a ruler to guide the alignment, especially if the patch has a complex shape. Take your time with this step to avoid any misalignment.
- Secure with Clamps: Once the patch is positioned correctly, it's crucial to secure it temporarily. Use clamps to hold the patch in place. Apply the clamps evenly around the patch, ensuring they are tight enough to prevent any movement but not so tight that they damage the fiberglass. Clamps provide a temporary hold, allowing you to make any necessary adjustments before permanently bonding the patch.
- Verify and Adjust: With the patch temporarily secured, inspect it from all angles. Ensure it is flush with the surrounding surface and that there are no visible gaps or misalignments. If any adjustments are needed, carefully realign the patch and re-clamp it. This step is vital to achieving a seamless blend.
By following these steps, you'll ensure that the fiberglass patch is positioned and secured precisely, setting the foundation for a successful and long-lasting repair. Remember, taking the time to align and clamp the patch correctly will pay off in the final result.
Unraveling the Mechanics: How Boats Function in Autonauts
You may want to see also
Finish and Sand: Smooth the surface and sand for a seamless blend
To ensure a seamless blend of a fiberglass patch onto an existing boat surface, the finish and sanding process is crucial. Here's a detailed guide on how to achieve a smooth and seamless finish:
Surface Preparation: Before sanding, it's essential to prepare the surface. Clean the area around the patch to remove any dirt, grime, or old paint. Use a mild detergent and water solution to ensure the surface is free from contaminants. Rinse thoroughly and allow the area to dry completely. This step ensures better adhesion and a smoother finish.
Sanding Technique: Start sanding the fiberglass patch and the surrounding area with fine-grit sandpaper (600-grit or higher). Work in small sections, gently sanding the patch and blending it with the original surface. Use long, even strokes, following the direction of the fiber. Avoid applying too much pressure, as it can create scratches or damage the fiberglass. The goal is to create a smooth transition between the patch and the surrounding surface.
Gradual Progress: As you sand, gradually increase the grit of the sandpaper to achieve a finer finish. Start with 600-grit and move to 1200-grit or higher if needed. This progression ensures a seamless blend, as the higher grit sandpaper will refine the surface further. Take breaks and wipe away the dust frequently to maintain visibility and control.
Filling and Smoothing: After sanding, inspect the surface for any imperfections or gaps. Use a fiberglass filler or putty to fill any small holes or imperfections, ensuring it matches the surrounding area. Allow the filler to cure according to the manufacturer's instructions. Once cured, sand the filled area again with fine-grit sandpaper to create a smooth, continuous surface.
Final Touches: For an even more refined finish, consider using a fiberglass primer and paint to match the boat's existing color. This step ensures the patch blends seamlessly with the rest of the vessel. Apply the primer and paint in thin, even coats, sanding between each layer to achieve a smooth, professional-looking result.
By following these steps, you can ensure that the fiberglass patch is seamlessly blended into the boat's surface, creating a smooth and aesthetically pleasing finish. Remember, patience and attention to detail are key during the sanding and finishing process.
Larson Boats: Worth the Investment?
You may want to see also
Frequently asked questions
Before applying the patch, ensure the surface is clean, smooth, and free of any debris. Use a mild abrasive like 400-grit sandpaper to lightly sand the area, creating a subtle texture. This will help the patch adhere better and blend seamlessly.
For a seamless blend, it's best to use a fiberglass cloth or mat with a similar weave and color to the surrounding area. Choose a grade suitable for the thickness of the patch. For thinner repairs, a lightweight cloth is ideal, while thicker patches may require a heavier-weight cloth.
Color matching is crucial for a successful blend. Mix the appropriate amount of fiberglass resin and hardener to create a batch of gelcoat or colorant that matches the boat's existing color. You can use a color matching guide or consult a professional for precise color codes.
Start by applying a thin layer of resin to the prepared surface, then carefully lay the fiberglass cloth or mat onto the resin, ensuring it's smooth and free of wrinkles. Use a rolling pin or a heat gun to gently heat the cloth, allowing it to bond to the surface. Repeat this process for additional layers, building up the thickness gradually.
Blending the edges is key to a successful repair. Use a sharp blade or a specialized fiberglass blade to carefully cut the patch edges at a slight angle. Then, apply a thin layer of resin along the cut edges and use a wet cloth to feather the edges, blending them smoothly with the surrounding fiberglass. Practice and patience are essential for a professional finish.