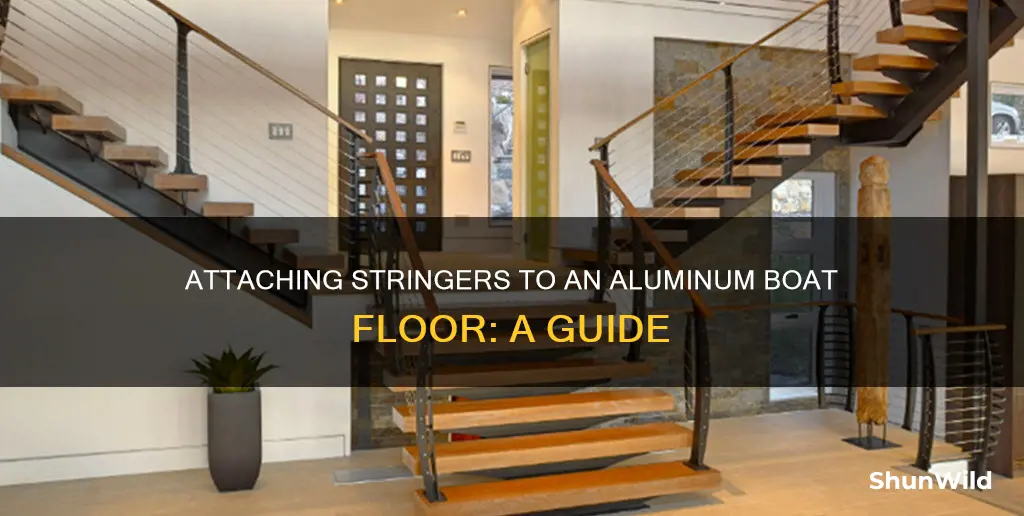
There are several ways to attach stringers to an aluminium boat floor. One way is to use pop rivets, which are commonly used by boat manufacturers as they are cheap, fast, and effective. Another method is to use stainless steel sheet metal screws, which provide a stronger hold but are more likely to back out due to the twisting and pounding of waves. Some people also use glue or thickened resin to attach the floor to the stringers, which can be effective if combined with other methods such as screwing or riveting. Additionally, it is important to consider the type of wood used for the stringers, as well as whether to coat it with epoxy or another sealant to prevent rotting.
What You'll Learn
- Use rivets, not screws, to avoid the twisting and pounding they take going over waves
- Use aluminium pop rivets to anchor the floor
- Seal the floor with Clear penetrating epoxy sealant
- Consider using Velcro to attach the floor for ease of access/maintenance
- Use aluminium channel pieces to reinforce the bottom and screw down a floor
Use rivets, not screws, to avoid the twisting and pounding they take going over waves
When it comes to attaching stringers to an aluminium boat floor, it is recommended to use rivets instead of screws. This is because screws have a tendency to back out from the twisting and pounding they take when navigating waves. Rivets, on the other hand, are better at withstanding such conditions and are less likely to come loose.
Rivets are also preferable to screws because they are used in permanent assemblies and are typically used to join thinner materials together. In addition, rivets are measured by diameter and grip length, with the diameter corresponding to the hole size and the grip range referring to the thickness of the fastened material. This makes rivets a more precise option for fastening.
Furthermore, rivets can be used when only one side of the installation material is visible, making them a more versatile option. They also provide a quick and efficient way to hold two materials together. While screws offer the convenience of disassembly and reassembly, rivets offer superior vibration resistance and a low-profile head.
It is worth noting that pop rivets, a type of rivet that can be installed from one side, are not watertight. If a watertight seal is required, closed-end rivets should be used and installed properly. Additionally, rivets cannot be reused or tightened once installed, and they may rotate if they are old, loose, or installed incorrectly.
The Jet Boat Engine: Water-Cooled Power
You may want to see also
Use aluminium pop rivets to anchor the floor
Aluminium pop rivets are a great way to anchor the floor of your boat. They are strong, easy to use, and will keep your floor securely in place. Here's a step-by-step guide on how to use aluminium pop rivets for this task:
Step 1: Gather Your Materials and Prepare the Surface
Before you begin, make sure you have all the necessary materials, including a sufficient number of aluminium pop rivets, a drill, a drill bit that matches the size of your rivets, safety goggles, and gloves for protection. Clean the surface of your boat floor and stringers, ensuring there is no dirt or debris that could interfere with the riveting process.
Step 2: Drill Holes
Put on your safety goggles and gloves. Using the drill and the appropriately sized drill bit, carefully drill holes through the boat floor and into the stringers underneath. Drill a hole at each point where you want to place a rivet, making sure the holes are spaced evenly and aligned correctly.
Step 3: Insert the Rivets
Take an aluminium pop rivet and insert it into one of the drilled holes. The rivet should fit snugly, with the tail end of the rivet protruding from the bottom. Repeat this step for all the drilled holes, ensuring each rivet is securely in place.
Step 4: Set the Rivets
Using a rivet gun or a rivet setting tool, begin to set each rivet. Squeeze the handles of the rivet gun firmly and hold for a few seconds to ensure the rivet is properly set. You will feel resistance, and then a snap, as the mandrel of the rivet breaks, leaving a tightly joined rivet in place.
Step 5: Inspect and Test
Once all the rivets are set, carefully inspect your work. Ensure that each rivet has been properly set and is securely holding the floor to the stringers. Test the floor for stability and sturdiness. You can also apply a sealant or epoxy to the rivets for added protection against water intrusion.
Using aluminium pop rivets is a reliable method for anchoring your boat floor. It is important to take your time, work carefully, and ensure that each rivet is properly set. With this method, you can feel confident that your boat floor is securely attached and ready for many adventures on the water!
Repairing Hairline Cracks: Restoring Your Boat's Floor
You may want to see also
Seal the floor with Clear penetrating epoxy sealant
Sealing the floor of your aluminum boat with a clear penetrating epoxy sealant is a crucial step to protect the wood from moisture damage and ensure the longevity of your boat. Here's a detailed guide on how to properly seal the floor:
Step 1: Prepare the Wood
Before applying the epoxy sealant, it is essential to ensure that the wood is bare and unfinished. The epoxy sealant will not effectively penetrate and seal the wood if there are any finishes or stains on the surface. Sand the wood to create a smooth and porous surface, removing any previous coatings or treatments. This step will allow the epoxy to penetrate deeper into the wood's grain. Additionally, always perform a small area test to ensure the epoxy sealant is compatible with the wood.
Step 2: Mix the Epoxy
TotalBoat's Clear Penetrating Epoxy Sealer comes in two parts: the resin and the hardener. It is crucial to mix these two components in the precise ratio specified by the manufacturer. For TotalBoat's product, the mix ratio is 2 parts resin to 1 part hardener by volume. You can use the calibrated TotalBoat 2:1 Epoxy Pumps to measure the exact ratio, or you can manually measure by weight or volume.
Step 3: Apply the Epoxy
Once you have prepared the wood surface and mixed the epoxy, it's time to apply the sealant. You can use a brush, roller, syringe, or epoxy spreader for application. Ensure that you apply the epoxy generously, allowing it to soak into the wood and fully saturate it. Pay particular attention to areas of rot or damage, as these areas will require more epoxy to restore and strengthen the wood.
Step 4: Allow Curing
After application, you need to give the epoxy sealant adequate time to cure. The curing time will depend on the temperature conditions. At 85°F, the epoxy will have a pot life of 20 minutes and will take 2 days to fully cure. At 40°F, the pot life extends to 40 minutes, and the full cure time is 4 days. During the curing process, the epoxy will create a hard, waterproof surface that will protect the wood from moisture and rot.
Step 5: Sand and Finish
Once the epoxy has fully cured, you can sand the surface lightly if needed. After sanding, you can apply a primer, paint, or varnish to further protect and enhance the appearance of the wood. The cured epoxy will improve the adhesion of any subsequent coatings, ensuring they last longer and provide better protection for your boat floor.
By following these steps and using a clear penetrating epoxy sealant, you will effectively seal and protect the floor of your aluminum boat. Remember to work in a well-ventilated area and always wear the appropriate protective gear when handling epoxy products.
Exploring Hyde Park: Paddle Boat Rental Rates
You may want to see also
Consider using Velcro to attach the floor for ease of access/maintenance
When it comes to attaching a floor to your aluminum boat, ease of access and maintenance is an important consideration. While traditional methods like screws, rivets, or welding offer secure fastening, they can be cumbersome and time-consuming when it comes to removing the floor for repairs or inspections. This is where Velcro comes in as a surprisingly effective and versatile alternative.
Velcro, specifically the heavy-duty variety, can provide a strong and removable bond between the floor and the boat's stringers. It eliminates the need for drilling, screwing, or riveting, making the installation process quicker and less invasive. More importantly, it offers unparalleled convenience when you need to access the underside of the floor. With Velcro, you can simply peel back the floor without the hassle of power tools or the risk of damaging your boat. This is especially advantageous if you frequently need to access the bilge area, inspect for corrosion, or perform maintenance on components located beneath the floor.
When choosing Velcro for this application, opt for heavy-duty or industrial-strength varieties with molded hooks. These provide a more secure grip and are less likely to creep or buckle due to humidity changes. Look for products designed for outdoor use, as they typically have higher temperature ratings and more durable adhesives that can withstand the marine environment. Ensure the Velcro is compatible with the materials of your boat's floor and stringers, whether they are aluminum, wood, or fiberglass.
To install the Velcro, start by cleaning and preparing the surfaces. Follow the manufacturer's instructions for application, as different adhesives have specific temperature requirements for optimal bonding. Firmly press the Velcro strips onto the floor and the stringers, allowing sufficient time for the adhesive to cure. Use a sufficient amount of Velcro to ensure a strong bond along the entire length of the floor. You may also want to consider adding additional support structures to the stringers to compensate for any potential reduction in structural rigidity due to using Velcro instead of permanent fasteners.
While Velcro may not be the conventional choice for attaching a floor to an aluminum boat, it offers undeniable benefits in terms of ease of access and maintenance. It strikes a balance between secure fastening and convenient removability, making it a viable option for boat owners who prioritize the ability to quickly and easily access hidden systems and components.
Transforming My Boat: Bass Boat Edition
You may want to see also
Use aluminium channel pieces to reinforce the bottom and screw down a floor
To attach stringers to an aluminium boat floor, you can use aluminium channel pieces to reinforce the bottom and screw down a floor.
First, you will need to purchase or cut aluminium channel pieces to the length of your boat. These channel pieces will act as support beams for your floor. The number of channel pieces you need will depend on the size and structure of your boat. Once you have your channel pieces, you will need to drill holes in them to match the rivet holes in your boat's hull.
Next, you will need to prepare the bottom of your boat for installation. Clean the inside of your boat thoroughly, removing any old rivet pins left after drilling out the rivet heads to take out the old floor. Mark the location of the hull cross members on the side of the boat so you can align your new floor during installation.
Now, you can install your new floor. With the help of at least one other person, lift and place the new floor into the boat. You will want the rivet holes in the new floor to align with the cross-member support marks on the sides of the hull. Make any slight adjustments to the floor's position before moving on.
Drill holes in the new floor for the pop rivets to secure it to the supports on the bottom of the boat. Before inserting a pop rivet, squeeze a small amount of marine silicone into and around the hole. This will help ensure a watertight seal. Continue installing rivets around the perimeter of the floor and in all the floor supports.
Finally, reinstall any boat seats and storage compartments that you had to remove. You can use tapered punches or Clecos (special tools for aligning holes) to help with the alignment. Simply place the tapered punch in the hole on the seat flange and then into the corresponding hole in the boat's hull. Push it in and roll it around to align the two holes perfectly. Once the holes are aligned, you can install solid rivets to secure the seats and compartments in place.
The Real Name of the Jaws' Quinn Boat
You may want to see also
Frequently asked questions
There are several ways to attach a plywood floor to aluminium stringers. Some people suggest using screws, such as 1-inch 3/16 stainless steel sheet metal screws. However, others recommend against this as screws can back out due to the twisting and pounding of the boat when in water. Instead, rivets are a popular choice as they are less likely to come loose. When using rivets, it is recommended to use closed-end pop rivets made of stainless steel or aluminium, and to apply 3M 5200 in the hole and head of the rivet for extra security. Another option is to use thickened resin to "glue" the floor to the stringers, without the need for any fasteners.
This depends on the intended use of the boat and personal preference. Screws can be a good option, but they may need to be locked in place with a product like Locktite silicone to prevent them from coming loose. Rivets are a popular choice, particularly aluminium or stainless steel pop rivets, as they are less likely to come loose and can be easily replaced if needed. Welding is a permanent solution but may not be practical if you need to regularly access the underside of the floor for maintenance.
It is recommended to use marine-grade plywood for the stringers on an aluminium boat. The wood should be coated with epoxy to protect it from rotting. Some people also suggest using laminated lumber (LVL) coated with epoxy, as it is strong, stable, and straight. However, this material can be heavy and expensive.
To attach aluminium channel pieces to the hull of your boat and reinforce the stringers, it is recommended to use solid rivets. Make sure to be aware of the alloy of the ribs, as using a tough alloy can cause 'hard spots' in the hull that may lead to breakage in other areas.