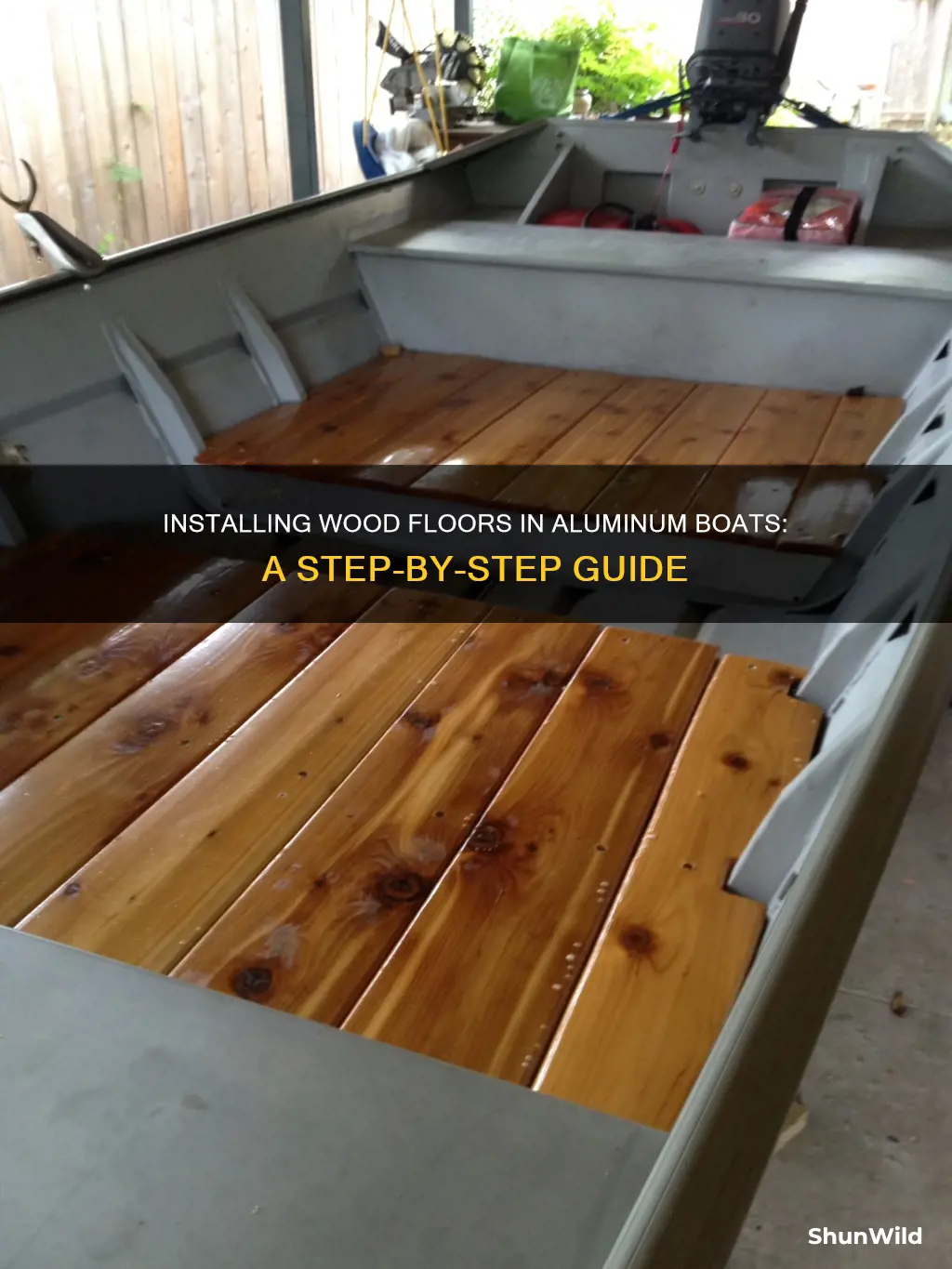
Adding a wooden floor to an aluminium boat is a great way to improve its stability and comfort. There are several ways to go about this, depending on your budget and the level of customisation you want to achieve. One of the most popular methods is to use marine-grade plywood, which is designed to withstand the harsh conditions of a marine environment. This type of plywood is made from better materials, has no internal voids, and uses waterproof glue to prevent deterioration. When selecting the plywood, it is important to match the thickness of the original floor to ensure a proper fit and maintain the boat's structural integrity.
To install the new wooden floor, you will need to remove the old flooring and clean the bottom of the boat thoroughly. You may also need to make repairs to the hull, such as fixing loose rivets or welding cracks. Once the boat is prepared, you can cut the plywood to size, seal it with oil-based paint, and attach it to the boat using rivets or screws. Finally, you can reinstall the seats and storage compartments, making sure to align the rivet holes for a secure fit.
What You'll Learn
Selecting the right wood
Type of Wood
The most popular choice for boat floors is hardwood due to its durability and resistance to water. Teak, mahogany, white oak, ash, and cedar are among the best options for boat floors. Teak, often considered the gold standard for boatbuilding, is valued for its durability, natural oils that repel insects and rot, and tight grain that prevents water penetration. Mahogany is known for its strength, stability, and beautiful reddish-brown colour. White oak, another versatile and rot-resistant option, is noted for its strength and tight grain. Ash wood is flexible and shock-resistant, making it suitable for areas that require some give. Cedar, a lightweight yet strong wood, has natural oils that resist rot and insects, and it adds a pleasant aroma to your boat.
Boat Type
The type of boat you own will significantly influence your choice of wood. For example, a small dinghy may require different materials than a large sailing yacht. Assess the specific needs of your boat, including its size, intended use, and exposure to the elements.
Durability and Workability
While durability is essential, you should also consider the ease of working with the wood. Some hardwoods may be challenging to cut, shape, and fasten, so finding a balance between durability and workability will make your boat-building or restoration process more enjoyable and efficient.
Sustainability and Cost
Sustainability is an important consideration in modern boatbuilding. Opt for hardwoods sourced from sustainable forests to minimise the environmental impact of your project. Additionally, premium hardwoods like teak and mahogany offer superior performance and longevity but come with a higher price tag.
Maintenance
Regular maintenance is crucial to ensure the longevity of your wooden boat floor. Keep your boat clean by washing it regularly with fresh water to remove salt, dirt, and other contaminants. Apply sealants and varnishes to protect the wood from water and UV damage, and reapply them periodically to maintain their effectiveness. Inspect your boat regularly for any signs of damage, such as cracks, rot, or insect infestation, and make repairs as needed.
Choosing the Best Boat Non-Skid for Your Vessel
You may want to see also
Sealing the wood
When sealing the plywood, it is also important to consider the type of wood being used. Regular plywood typically has external blemishes and internal voids, and the glue used may not be waterproof. Therefore, it is highly recommended to use marine-grade plywood, which is made from better materials and uses waterproof glue.
For boats wider than the standard 4x8-foot sheet of plywood, one cost-cutting option is to buy a larger sheet of marine plywood and cut it in half, creating two pieces that can be spliced together to form the required width. This will result in a very firm floor, and the joint can be reinforced with an aluminum strap and rivets.
Once the paint has dried, the plywood can be joined together using an aluminum strap and rivets. Start by pre-drilling the aluminum strap with rivet holes, and then drill the corresponding holes through the plywood. Apply a small dab of marine silicone to each hole before inserting the rivets. This will ensure a watertight seal and provide additional support to the joint.
By following these steps and allowing adequate time for the paint to dry, you can effectively seal the wood and create a strong, durable floor for your aluminum boat.
Hulu's Fresh Off the Boat: Streaming Availability and More
You may want to see also
Attaching the wood to the aluminium boat
Step 1: Prepare the Wood
Before attaching the wood to the aluminium boat, it is important to seal the wood to protect it from water damage. Use a good quality oil-based paint and apply two coats to all surfaces of the wood, allowing adequate drying time between coats. This will help to extend the life of the wood by providing a waterproof barrier.
Step 2: Select Appropriate Fasteners
There are several options for fasteners when attaching the wood to your aluminium boat. You can choose from screws, rivets, or welding. Consider the advantages and disadvantages of each option:
- Screws: They are easy to install and provide a secure hold. However, they may loosen over time and require maintenance.
- Rivets: Pop rivets or solid aluminium rivets are commonly used. Pop rivets are easy to install and can be found in large flange sizes for added support. Solid aluminium rivets provide a strong and watertight connection but require special tools for installation.
- Welding: Welding is a permanent solution but may not be suitable for all boat designs and requires specialised equipment.
Step 3: Prepare the Aluminium Boat
Before attaching the wood floor, clean the inside of the aluminium boat thoroughly. Remove any old rivet pins or fasteners that may interfere with the new floor installation. Mark the locations of the hull cross members on the side of the boat, ensuring they are visible once the new floor is in place. This will help guide your fastener placement.
Step 4: Dry Fit the Wood Floor
"Dry fit" the wood floor in the boat to ensure a snug fit. Leave a small gap of at least 1/8" between the wood and the sides of the boat to allow for the floor covering. Make any necessary adjustments by trimming or sanding the edges of the wood.
Step 5: Apply Adhesive and Fasteners
Apply a small amount of marine-grade silicone or adhesive to the rivets or screws before inserting them. This will help create a watertight seal and provide additional support. Install the fasteners at regular intervals along the perimeter and cross members of the boat, ensuring a secure hold.
Step 6: Finish and Seal
Once the wood floor is attached, finish the project by sealing any exposed edges or screw holes with marine silicone. This will help prevent water ingress and protect your boat from corrosion. Allow the silicone to cure completely before using the boat.
Winterizing Outboard Boat Engines: A Step-by-Step Guide
You may want to see also
Adding insulation
Planning and Materials
Before you begin, it's important to plan the layout of your insulation. Identify the areas where you want to add insulation, such as the floor, walls, and compartments. Determine the amount of insulation you'll need by measuring the length and width of these areas.
For the insulation material, closed-cell foam sheets are a popular choice. You can find these at most home improvement stores, like Home Depot. Specifically, look for purple closed-cell foam sheets with thicknesses of 1" and 2". Additionally, you'll need an aluminum subfloor and decking to go over the insulation. The subfloor should be around .060 in thickness, while the decking can be .090.
Installation Process
- Prepare the Boat: Strip the boat down to the aluminum hull. This will give you a clean slate to work with.
- Cut and Place the Foam Sheets: Measure and cut the foam sheets to fit snugly between the boat ribs on the floor and inside the compartments. This will ensure proper drainage.
- Drill Drainage Holes: If there is no drainage channel in the center of the boat, drill a 3/4" hole in the floor ribs to allow trapped water to move.
- Install the Subfloor and Decking: Place the aluminum subfloor and decking over the foam sheets. Ensure they are securely attached and create a sturdy base.
- Fill Gaps with Sheet Foam: Use the foam sheets to fill in any remaining gaps between compartment walls and around the transom area.
- Add Pour Foam: In areas above the subfloor that are isolated from the rest of the boat, such as between PVC for rod lockers or empty spaces, consider adding pour foam for additional stiffness and floatation. Make sure to follow the manufacturer's instructions and safety precautions when working with pour foam.
- Seal and Protect: Finally, seal any exposed edges or openings with marine-grade sealant or paint to protect your handiwork from the elements.
Tips and Tricks:
- Avoid Waterlogged Foam: One of the challenges with insulation in boats is the potential for waterlogging. To mitigate this, avoid using pour foam in areas where it can expand and block drainage channels.
- Prevent Fuel Contact: Fuel can destroy foam insulation, so avoid placing foam board in the last two ribs near the transom and bilge. You can also tape the foam closer to the back with aluminum HVAC tape for added protection.
- Consider a Removable Floor: If you plan to use pour foam near the transom, make the floor removable with screws instead of rivets. This will allow for easier inspection and replacement of the foam over time.
- Priming the Hull: While some people prime their hull with paint before spraying foam insulation, others find it unnecessary. Consult with the foam manufacturer for their recommendations.
- Alternative Methods: If you're hesitant about spray foam, consider self-adhesive foam sheets or using styrofoam boards under the floor. These methods can provide effective insulation while being easier to replace if needed.
Remember to take your time, work in a well-ventilated area, and follow safety guidelines when working with any chemicals or power tools. Good luck with your project!
Keep Geese Away: Protect Your Boat Dock
You may want to see also
Finishing touches
Now that you have your new wooden floor in your aluminium boat, there are a few final steps to ensure it is secure, sealed, and ready for the water.
Firstly, you will want to seal any exposed edges of the plywood with oil-based paint or epoxy resin. This will protect the wood from water damage and ensure the longevity of your new floor. You should also fill any gaps or holes with marine-grade silicone to create a watertight seal.
If you haven't already, now is the time to re-install any boat seats, storage compartments, or other equipment that you removed. Use stainless steel or aluminium screws and solid aluminium rivets to secure these items through the new wooden floor and into the boat's hull.
When re-installing seats and compartments, take the time to align the rivet holes carefully. A slight adjustment to the floor's position can ensure the holes line up as closely as possible with the original rivet holes in the boat's hull. Use a tapered punch or a small screwdriver to help align the holes, and a small dab of marine silicone around each hole before inserting the rivet.
If you are reusing the floor covering (carpet or vinyl), ensure it is clean and free of any dirt, debris, or old glue. Lay the covering, face-up, on a smooth surface, and place the new floor on top, also face-up. Cut the floor covering to size, leaving a few inches of excess around the perimeter. Apply an appropriate glue for your type of floor covering, following the manufacturer's instructions, and lay the new floor covering in place. Use stainless steel staples to secure the floor covering to the underside of the plywood, and wrap the excess neatly around the edges.
Finally, give your new floor a test run! Fill the boat with water to check for any leaks around your new floor and make sure it is secure and watertight. Enjoy your refreshed boat!
Billie's Tragic End: Unraveling the Open Boat Mystery
You may want to see also
Frequently asked questions
You can use screws, rivets, or even weld the floor in place. It is important to consider the ease of removal for maintenance and the potential for galvanic corrosion between dissimilar metals.
Marine-grade plywood is recommended due to its superior materials, lack of internal voids, and waterproof glue. Regular plywood may have blemishes, voids, and non-waterproof glue, shortening its lifespan.
You can use oil-based paint, epoxy, fiberglass, or a combination of these. Sealing both sides of the plywood is recommended for maximum protection. Allow adequate drying time between coats.
Before beginning, ensure you have all the necessary tools and personal protective equipment, such as safety glasses, hearing protection, and gloves. Measure and cut the plywood to fit the boat, allowing for a small gap between the wood and aluminum for drainage. Reusing the old floor covering can save money and provide a template for the new floor.