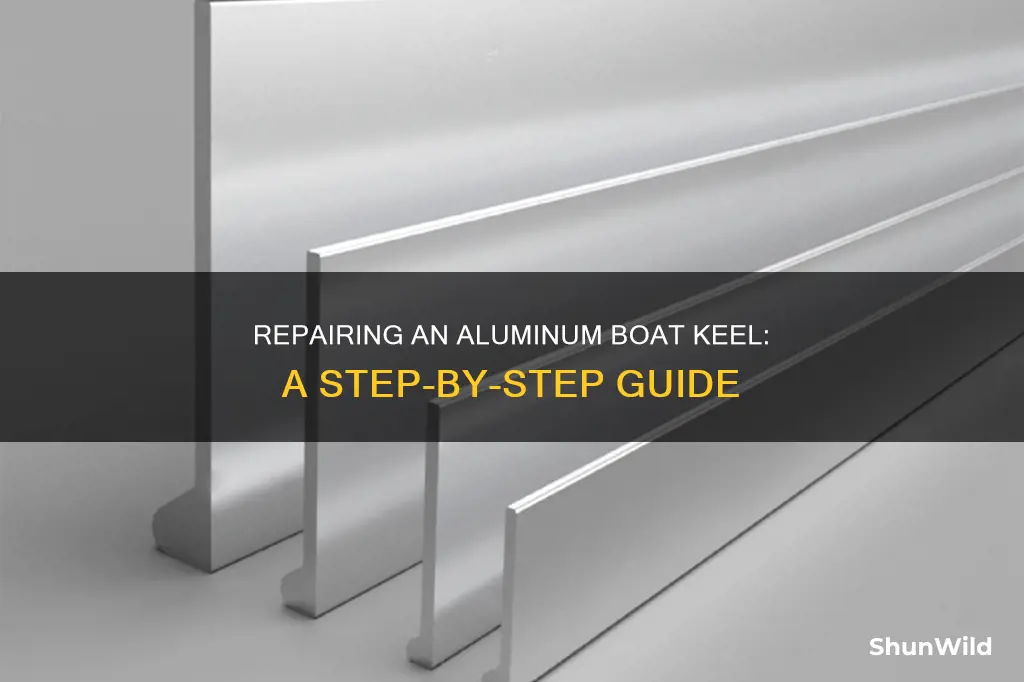
Repairing the keel of an aluminium boat can be a tricky task. While welding is often suggested as the best method, it can be expensive and there are other ways to fix a leaky keel. Epoxy putty, such as J.B. Weld, can be used to repair tears, cracks or punctures in the skin of the boat. It is important to clean and sand the area before applying the putty. Another option is to use a sealant like 3M #5200, which can be used to fill the hollow keel from the outside. Drilling holes in the keel and filling them with sealant can stop leaks. It is also important to consider the cause of the leak, which may be electrolysis or rivets that need to be tightened.
Characteristics | Values |
---|---|
Repair method | Welding |
Repair method | Epoxy putty |
Repair method | 3M #5200 sealant |
Repair method | JB Weld |
Repair method | Fiberglass and epoxy |
Repair method | Gluvit |
Repair method | Polyester resin |
Repair method | Brazing |
Repair method | Soldering |
Repair method | Marine epoxy |
Repair method | Flex Seal |
Repair method | Flex Paste |
Repair method | Marine sealant |
What You'll Learn
Welding or using epoxy to repair a keel
When repairing a keel, welding and using epoxy are two different methods that can be considered. Both methods have their own advantages and can effectively repair damage to the keel of a boat.
Welding
Welding is a common method for repairing aluminium boats. It involves using a welding machine to melt and join metal parts together. This method can be used to repair cracks, holes, or damaged sections of the keel. It is important to note that welding requires specialised skills and knowledge of the specific aluminium alloy used in the boat. Additionally, welding near rivets is not recommended as the heat can damage the gasketing between connections.
Using Epoxy
Epoxy is an alternative method for repairing keels, offering a strong and flexible solution. One advantage of using epoxy is that it can be applied without specialised welding equipment, making it more accessible for boat owners to perform themselves. Epoxy repairs typically involve cleaning the surface, applying the epoxy, and then sanding and painting the repaired area. It is important to use the correct type of epoxy for the material of the keel, such as G/flex Epoxy for cast-iron keels, which provides toughness and tensile elongation to prevent cracks from reappearing.
Both welding and epoxy repair methods have their benefits, and the choice between them depends on factors such as the extent of the damage, the material of the keel, and the skills and equipment available. For major structural damage, welding may be the preferred option, while epoxy repairs are often suitable for cosmetic repairs or sealing leaks.
Sailing the Valheim Seas: Mastering Boat Navigation
You may want to see also
Repairing a keel with sealant or putty
If you are repairing a keel with sealant or putty, there are a few different methods you can use. Firstly, you will need to identify the problem. If you have a leaking rivet, you can replace the rivet or peen it, which involves gently hammering it to mash it slightly. If you have a tear, crack or puncture, you can repair this with epoxy putty or sealant.
If you are repairing a hollow keel, you can fill the space with sealant. Drill a few 1/4" holes 4-6 inches apart along the length of the damaged area and fill with sealant. You can also use epoxy putty to fill the space. If you are repairing a keel/hull joint, you can use a scraper blade to remove the old sealant, sand the area, and then reseal with a flexible compound.
If you are repairing a keel stub, you can use a thick washer of polysulfide compound around each bolt where it enters the hull and fill the rest of the joint with a stiff, reinforced epoxy putty. You can also use a product called Gluvit for minor leaks.
Alabama's Boat Dock: A Mystery Unveiled
You may want to see also
Fixing a keel with bolts, screws and washers
Step 1: Inspect the Keel and Identify the Problem
Before beginning any repair work, it is crucial to thoroughly inspect the keel and identify the specific issues that need to be addressed. Check for signs of water intrusion, corrosion, or damage to the keel bolts, nuts, and washers. It is important to determine the extent of the damage and understand the underlying causes to develop an effective repair plan.
Step 2: Gather the Necessary Materials and Tools
Make sure you have all the required materials and tools before starting the repair work. This includes stainless steel truss head Phillips screws, flat washers, nylon locking nuts, marine-grade sealant (such as 3M 5200), epoxy putty (like J.B. Weld), wire brushes, and appropriate safety gear (goggles, gloves, respirator, etc.). Having all the necessary items on hand will make the repair process more efficient and help ensure a successful outcome.
Step 3: Prepare the Surface
Clean and prepare the surface of the keel and the surrounding area. Remove any built-up crusting, debris, or old sealant using wire brushes or sandpaper. Ensure that the surface is free of dirt, grease, or other contaminants that may interfere with the adhesion of the new fasteners and sealant. This step is crucial for achieving a strong and durable repair.
Step 4: Replace or Tighten Keel Bolts
If the keel bolts are damaged or corroded, they will need to be replaced. Consult a qualified professional or boatyard for assistance in removing the old bolts and installing new ones. In some cases, it may be necessary to fabricate new bolts to match the original specifications. If the bolts are simply loose, tightening them with the appropriate torque may be sufficient.
Step 5: Apply Sealant and Install Washers and Screws
Before inserting the screws, apply a bead of marine-grade sealant (such as 3M 5200) around each screw hole. This will help create a watertight seal and prevent future leaks. Place a flat washer over each screw and secure it with a nylon locking nut on the backside. Use stainless steel truss head Phillips screws of the appropriate size and length for the best results.
Step 6: Re-fair and Coat the Keel
Once all the screws, washers, and nuts are in place, it is time to re-fair and coat the keel. Sand the repaired area to create a rough surface that will enhance the adhesion of the new coating. Apply a suitable epoxy barrier coat, such as Interprotect 2000E, to protect the keel and ensure a smooth finish. Follow the manufacturer's instructions for proper application and curing times.
Step 7: Final Inspection and Testing
After the repairs are complete, conduct a final inspection to ensure that all fasteners are secure and the sealant is properly applied. Test the boat in a controlled environment, such as a boatyard or marina, to ensure that the repairs have been successful and the keel is functioning correctly. Check for any signs of leaks or movement in the keel and address any remaining issues.
Remember, keel repairs can be complex and require a good understanding of boat maintenance and repair techniques. If you are unsure about any aspect of the process, it is always best to consult a qualified boat repair professional or yard for guidance or assistance.
The Intriguing Question: Boats Dock, But Do They Land?
You may want to see also
Repairing a keel with fibreglass
Repairing the keel of an aluminium boat with fibreglass is a complex process and it is recommended that you seek out a professional welder to do the job. However, if you are confident in your ability to perform the repair, here is a step-by-step guide:
Firstly, it is important to prepare the surface by cleaning and drying the area. This includes removing any paint and grinding or sanding the surface to create a smooth, even base for the fibreglass to adhere to. It is also essential to ensure that there is no remaining wax on the keel, as this can affect adhesion.
Next, you will need to mix and apply a thickened epoxy resin to the damaged area. This will help to build up the structure of the keel and provide a strong foundation for the fibreglass. Allow this to cure thoroughly before proceeding.
Once the epoxy has cured, you can begin to apply the fibreglass. Cut the fibreglass cloth to size, ensuring that it is large enough to cover the entire damaged area. It is recommended to use a thin glass cloth, such as 6oz, and apply multiple layers to ensure a strong repair. Apply the fibreglass using epoxy resin, working it into the cloth to remove any air bubbles and ensure a strong bond.
After the fibreglass has cured, you can sand or grind the area to create a smooth, flush surface. This will help to create a seamless repair and improve the overall finish.
Finally, you can apply a barrier coat and anti-fouling paint to protect the repaired area and improve its appearance.
It is important to note that this is a general guide and the specific steps may vary depending on the extent of the damage and the products used. Always refer to the manufacturer's instructions for the epoxy and fibreglass products you are using, and ensure you are working in a well-ventilated area with the appropriate safety gear.
Air Filters in Boat Engines: Are They Necessary?
You may want to see also
Using a professional welder to repair a keel
Choosing the Right Professional Welder
- Look for a welder who has experience with aluminium welding. Aluminium welding requires some unique techniques and knowledge, so it's important to find someone who is skilled in this area.
- Consider contacting fabrication shops, off-road shops, racing shops, or marine fabrication shops. These places often have welders who are experienced in working with aluminium and can provide you with a reasonable quote.
- Ask for recommendations from boat owners who have had similar repairs done. Word-of-mouth referrals can help you find reliable and skilled professionals.
Preparation for Welding
- Ensure that the aluminium boat is clean and free from any contaminants. Aluminium oxide can form on the surface when exposed to air, making welding more difficult. Use a stainless steel brush to remove any oxidation from the welding surfaces.
- Cut the aluminium pieces right before welding. Aluminium should not be exposed to air for long periods, as it can lead to oxidation. Use a metal circular saw, laser, or plasma cutter for precise cutting.
- Avoid using oxy-fuel for cutting or pre-heating, as it contains oxygen, which can lead to more oxidation during welding.
- Do not use compressed air or shop clothes to clean the aluminium surfaces, as they can contain moisture and contaminants that can react negatively during welding. Instead, use a solvent to remove grease and oil from the surfaces to be welded.
Welding Process
- Use the right filler metal for aluminium welding. The choice of filler metal is crucial for a strong and durable weld.
- Ensure proper cleaning and surface preparation. Cleanliness is critical in TIG welding. Both the filler material and the base metal must be free from any contaminants.
- Start by tack welding and welding the borders of the aluminium sheet to hold the edges securely in place.
- Follow a specific sequence for welding to avoid distortion. Weld from the centre of the boat outwards, and work on the transverse butt welds before moving to the longitudinal butt welds.
- Use a low amperage setting on your TIG welding machine and clean the area with a light arc before starting the weld. This helps remove any final contaminants and ensures a strong weld.
- For boat propellers, practice on scrap aluminium pieces first. Propellers are expensive, and you don't want to risk damaging them during the learning process.
By following these instructions and working with a skilled professional welder, you can effectively repair the keel of your aluminium boat and have it back in the water in no time.
Zinc Overload: Steel Hull Boat's Demise
You may want to see also
Frequently asked questions
Welding is a skilful job and can be expensive. It is also not recommended for riveted boats as the heat can melt the bonding material and cause new leaks.
Epoxy putty is a good option for repairing leaks in an aluminium boat keel. Clean the area, removing any paint, and apply the putty. Allow 24 hours to cure.
Products such as JB Weld, JB Water Weld, and 3M 5200 Marine Sealant can be used to repair leaks in aluminium boats.
Stainless steel truss head Phillips screws with flat washers and nylon locking nuts are recommended for repairing missing rivets. Use a sealant around the screw head and clean the exterior with lacquer thinner.
Adding a rubber keel guard can help to prevent corrosion and damage to an aluminium boat keel.