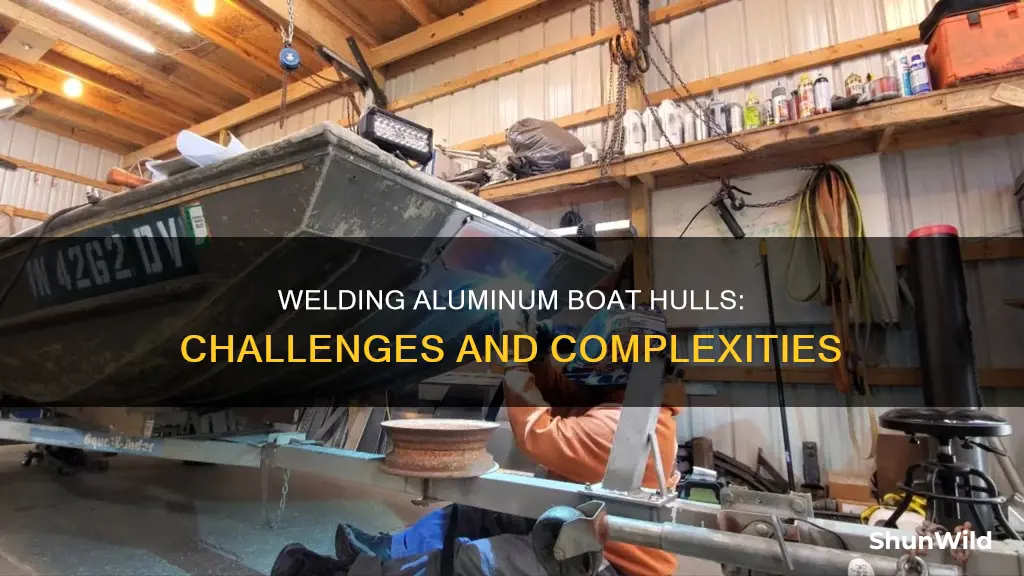
Welding an aluminium boat hull can be challenging, especially for beginners. Aluminium is a complicated metal to weld due to its unique characteristics, such as its low melting point and high heat dissipation rate. It also tends to be very porous, which can lead to corrosion and other issues. However, with the right knowledge, skills, and equipment, it is certainly possible to weld aluminium successfully.
One of the critical aspects of welding aluminium is cleanliness and surface preparation. The filler material and the base metal must be thoroughly cleaned and free of any contaminants, as aluminium is very susceptible to oxidation when exposed to air. Proper cleaning ensures a stronger and more reliable weld. Additionally, choosing the correct filler metal and understanding the welding procedures specific to aluminium are essential for achieving desirable results.
Another challenge with welding aluminium is avoiding distortion. Aluminium expands and contracts irregularly during the heating and cooling cycle, which can affect the shape and functionality of the boat. To prevent this, welders must follow a specific sequence, starting with tack welding the borders of the aluminium sheets and working strategically to minimise the accumulation of heat in any one area.
Characteristics | Values |
---|---|
Welding technique | TIG welding |
Welding difficulty | Difficult due to the need for specialised techniques, the material's low melting point, and its fast heat dissipation |
Welding speed | Fast |
Welding preparation | Requires thorough cleaning and surface preparation to remove contaminants and prevent oxidation |
Welding equipment | Requires a machine with HF and a spool gun |
Welding experience | Recommended to gain experience through practice before attempting repairs |
Welding sequence | Tack weld borders, chain weld stringers, install butt plates, weld longitudinal seams, weld connections |
What You'll Learn
The challenges of welding aluminium boats
Welding aluminium boats can be challenging, especially for beginners. Here are some of the key challenges to consider:
Difficulty of the Process
Welding aluminium requires following some unique techniques and methods. Important factors to consider when welding aluminium include choosing the correct filler metal, thorough cleaning of the base material, and using appropriate welding procedures. Aluminium is very different from steel or other standard materials in terms of science and fracture susceptibility.
Experience and Skill Requirements
Welding aluminium boats is not a task for beginners. It requires a high level of experience and skill to ensure strong and reliable welds. Inexperience can lead to more damage and increased expenses. It is crucial to understand the parameters of aluminium welding, including the extreme importance of cleanliness to avoid contamination.
Aluminium's Unique Characteristics
Aluminium has a lower melting point than steel but dissipates heat much faster. This means that welders need to work quickly and maintain a higher heat level than they would with steel to create a weld puddle. Aluminium is also highly susceptible to burning through, making it challenging to work with thin sheets, which are commonly used in boat construction.
Oxidation
Untreated aluminium quickly oxidises when exposed to air, making welding more difficult over time. Therefore, aluminium pieces should be cut immediately before welding to minimise the formation of aluminium oxide on the surfaces. A clean stainless steel brush is an effective tool for removing aluminium oxide and providing a better welding outcome.
Distortion
Aluminium welding distortion is a common problem for beginners. During the heating and cooling cycle, the welded aluminium can expand and contract irregularly, causing the boat's shape and outline to distort. This can affect not only the aesthetic appeal but also the functionality of the boat. To avoid distortion, a careful sequence of welding steps must be followed, including tack welding, chain welding, and specific patterns to minimise the accumulation of heat in any one area.
Boat Insurance in Arizona: What's the Law?
You may want to see also
Choosing the right welding equipment
Welding an aluminium boat is challenging, especially for beginners. However, with the right tools and knowledge, it can be done successfully. Here is a guide to choosing the right welding equipment for the job:
When it comes to welding aluminium boats, there are several key pieces of equipment that you will need. Here is a list of the essential tools and considerations to help you get started:
- Welding Machine: The type of welding machine you choose is crucial. Aluminium welding often requires a specialised machine capable of AC/DC operation, such as a TIG (Tungsten Inert Gas) welder or a MIG (Metal Inert Gas) welder with pulse functionality. TIG welding offers greater control and is suitable for thinner aluminium sheets, while MIG welding is typically used for thicker aluminium.
- Filler Metal: Choosing the correct filler metal is essential when welding aluminium. The filler metal should be marine-grade aluminium, typically 5356 and 4043 alloy, to ensure strong and durable welds.
- Spool Gun Attachment: When using a MIG welder for aluminium, a spool gun attachment is necessary. The softness of the aluminium welding wire requires a spool gun to feed the wire smoothly through the cable to the welding gun.
- Cleaning and Surface Preparation: Cleanliness is of utmost importance when welding aluminium. Ensure that all surfaces to be welded are thoroughly cleaned and free of any grease, oil, or foreign materials. Use high-quality solvents to remove contaminants and consider using a stainless steel brush to remove aluminium oxide from the welding surfaces.
- Cutting Equipment: It is recommended to cut aluminium pieces just before welding, as untreated aluminium can oxidise when exposed to air for a prolonged period, making welding more difficult. A plasma arc cutter, laser cutter, or circular saw can be used for this.
- Practice and Technique: Welding aluminium requires a different technique than welding steel. Aluminium has a lower melting point and dissipates heat faster, so you need to work quickly and maintain a higher heat level than you would with steel. Practising on scrap aluminium pieces is highly recommended to develop your technique and get a feel for welding aluminium.
- Safety Gear: Welding can be hazardous, so it is crucial to wear the appropriate safety gear. This includes items such as a welding helmet, flame-resistant gloves, and respiratory protection, as well as eye protection and a fire extinguisher.
By choosing the right welding equipment and following the necessary preparation and safety procedures, you can successfully weld an aluminium boat and create a strong and durable vessel.
Biggest Boats on Deadliest Catch: Who Reigns Supreme?
You may want to see also
Preparing the aluminium for welding
Welding an aluminium boat can be challenging, especially for beginners. Aluminium welding requires specific methods and procedures to be followed. Here is a detailed guide on preparing the aluminium for welding:
Cleanliness and Surface Preparation:
Cleanliness is of utmost importance when welding aluminium. Both the filler material and the base aluminium surface must be thoroughly cleaned and free of any contaminants such as oil, grease, or foreign objects. Use a high-quality solvent to remove grease and oil from the aluminium pieces. Do not use shop clothes or rags as they can transfer dirt and grime to the aluminium surface. Instead, use a clean stainless steel brush to remove aluminium oxide from the welding surfaces. Aluminium oxide can compromise the integrity of your weld, so removing it ensures a longer-lasting result.
Cut Pieces Right Before Welding:
Untreated aluminium quickly oxidises when exposed to air, making welding more difficult. Therefore, cut the aluminium pieces immediately before welding. Use a plasma arc, laser, or a circular saw to cut the pieces. Avoid using a grinder as it leaves burrs and imperfections that hinder the welding process.
Avoid Oxy-Fuel and Compressed Air:
Oxy-fuel contains oxygen, leading to unwanted oxidation in your welds. Similarly, compressed air often contains moisture, which can react negatively during the welding process, causing oxidation.
Choose the Right Filler Metal:
Selecting the correct filler metal is crucial when welding aluminium. The filler metal should be compatible with the base aluminium alloy and the intended service conditions of the boat.
Practice and Experience:
Welding aluminium can be tricky, and it's easy to burn through the material. Practising on scrap pieces of aluminium before attempting to weld the boat is essential to gaining experience and understanding the unique characteristics of aluminium welding.
McCook Lake's Boat Launch: A South Dakota Gem
You may want to see also
Techniques for welding aluminium boats
Welding an aluminium boat is challenging, especially for beginners. However, with the right knowledge, skills, and equipment, it can be done successfully. Here are some essential techniques to help you weld an aluminium boat effectively:
Selecting the Right Welding Equipment
Aluminium welding requires specific tools such as a MIG or TIG welder. These welders ensure a stable wire feed and reduce the risk of contamination, which is crucial in achieving solid and clean welds.
Preparing the Aluminium Surface
Proper surface preparation is vital for aluminium welding. Start by thoroughly cleaning the aluminium to remove any dirt, grease, or oxide layers. Use a stainless steel brush designed for aluminium, and clean the surface just before welding to prevent contamination and ensure a clean weld pool.
Controlling Heat Input
Aluminium has high thermal conductivity, so it heats up and cools down quickly, which can lead to warping or burn-through. Control the heat input by using short welds and allowing the material to cool between passes. Preheating the aluminium slightly can also help manage heat flow and create more consistent welds.
Choosing the Right Filler Material
Using the correct filler material is essential for strong welds. The filler rod or wire should match the base aluminium material to ensure compatibility and strength. For most marine-grade aluminium, 5356 and 4043 filler materials are commonly used.
Welding in a Controlled Environment
Environmental factors can impact the quality of aluminium welding. Ideally, weld in a clean, controlled environment to prevent contaminants. If welding outdoors, use a portable welding shelter to protect the area from wind, dust, and moisture, ensuring a stable welding environment.
Practicing Proper Technique
Mastering the technique of aluminium boat welding is key to achieving strong and durable welds. Maintain a consistent travel speed for even heat distribution, practice steady hand movements, and use a push technique when welding to keep the shielding gas in the weld pool, further reducing the risk of contamination.
Avoiding Distortion
Aluminium welding distortion refers to the irregular expansion and contraction of the welded aluminium during heating and cooling. To avoid this, follow a specific sequence: tack and weld each border of the aluminium sheet, carefully chain-weld the stringers to the boat's body, install butt plates, and then weld the longwise creases, edges, and connections to plating and frames.
Additionally, always cut aluminium pieces right before welding, as untreated aluminium oxidises when exposed to air, making welding more difficult. Remove aluminium oxide from welding surfaces using a stainless steel brush, and clean every piece with a solvent to remove grease and oil.
The Ranger Bass Boat's Impressive Speed Secrets
You may want to see also
Common mistakes to avoid when welding aluminium boats
Welding an aluminium boat can be challenging, especially for beginners. However, with the right knowledge and skills, it can be done successfully. Here are some common mistakes to avoid when welding aluminium boats:
- Not using the right equipment: Aluminium welding requires specific tools such as a MIG or TIG welder to ensure a stable wire feed and reduce the risk of contamination. Using a welder designed for aluminium helps achieve solid and clean welds.
- Inadequate surface preparation: Properly cleaning the aluminium surface to remove any dirt, grease, or oxide layers is crucial. Use a stainless steel brush designed for aluminium, and clean the surface just before welding to ensure a clean weld pool and prevent contamination that can weaken the welds.
- Not controlling heat input: Aluminium has a high thermal conductivity, so it's important to control the heat input with short welds and allow the material to cool between passes. Preheating the aluminium slightly can also help manage heat flow and create more consistent welds.
- Choosing the wrong filler material: The filler rod or wire should match the base material to ensure compatibility and strength. For most marine-grade aluminium, 5356 and 4043 filler materials are commonly used.
- Welding in an uncontrolled environment: Environmental factors can affect the quality of aluminium welding. Weld in a clean, controlled environment to prevent contaminants from compromising the weld. If welding outdoors, consider using a portable welding shelter.
- Incorrect technique: Master the technique of aluminium boat welding to achieve strong and durable welds. Maintain a consistent travel speed for even heat distribution, practice steady hand movements, and use a push technique when welding aluminium to keep the shielding gas in the weld pool and reduce contamination.
- Not cutting pieces just before welding: Untreated aluminium oxidises when exposed to air, making welding more difficult. Cut aluminium pieces just before welding to minimise oxidation and improve weld quality.
- Failing to remove aluminium oxide: Aluminium oxide compromises the integrity of your weld. Use a stainless steel brush to remove aluminium oxide from the welding surfaces for longer-lasting welds.
- Not cleaning pieces with solvent: Shop clothes or compressed air can leave grease, oil, or moisture on the aluminium surfaces, causing flaws in your welds. Use a high-quality solvent to thoroughly clean each piece and ensure a truly clean surface.
Where Does a Boat Belong? Docking Explained
You may want to see also
Frequently asked questions
Welding an aluminium boat hull is a challenging task that requires expertise and precision. It is not recommended for beginners as aluminium welding is more complex than welding steel or other standard materials due to its scientific properties and brittleness.
When welding aluminium, it is crucial to select the correct filler metal, thoroughly clean the base material, and ensure proper welding procedures are followed. Aluminium is very sensitive to contamination and requires dedicated tools that have not been used for other metals.
One of the biggest challenges is avoiding distortion, which refers to the irregular expansion and contraction of the welded aluminium during heating and cooling. This can affect the aesthetics and functionality of the boat. Another challenge is preventing oxidation, as untreated aluminium left exposed to air can oxidise, making welding more difficult.
It is recommended to cut aluminium pieces immediately before welding using a plasma arc, laser, or a circular saw. This helps prevent oxidation and ensures a cleaner weld.
For vessels, a specific grade of aluminium is typically used, such as 5086 or 5083, which contains magnesium to enhance strength without requiring treatment.