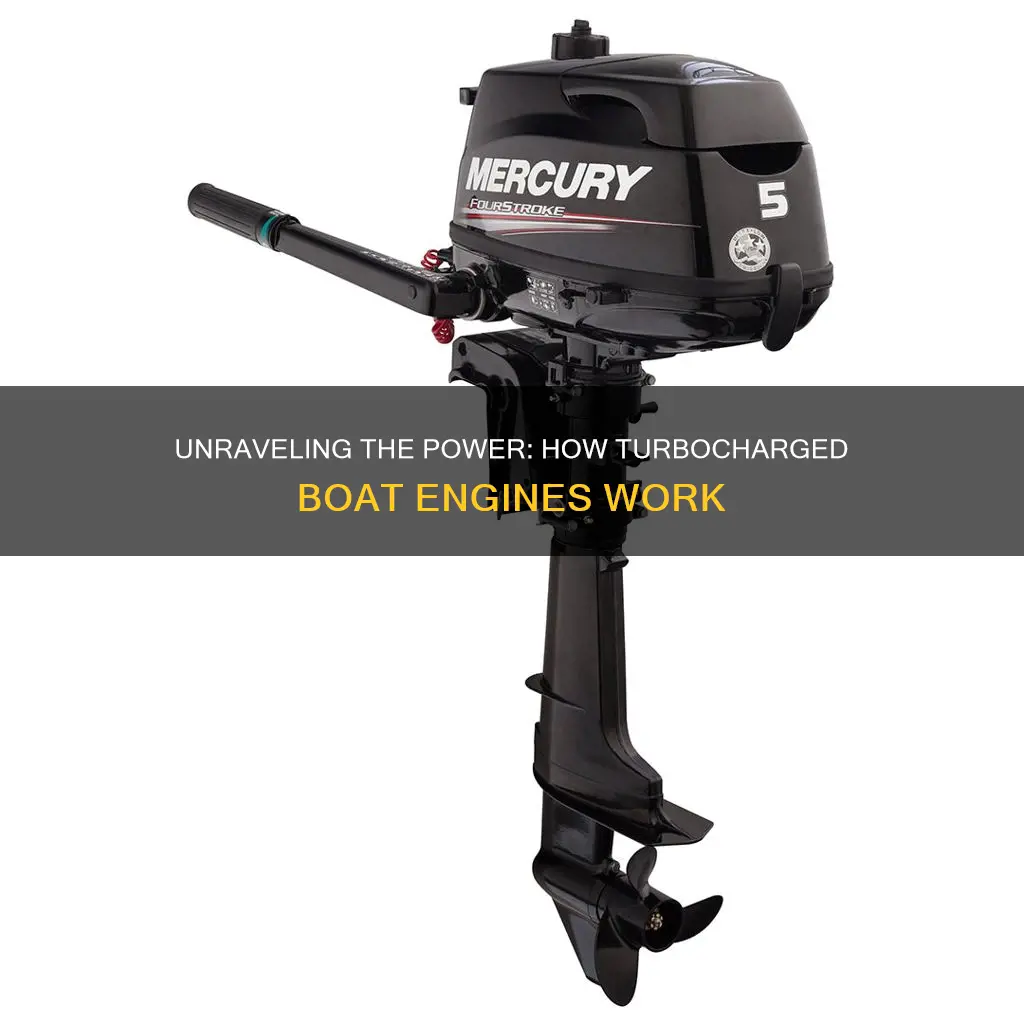
A turbining boat, also known as a jet boat, operates by utilizing a powerful engine that drives a turbine. This turbine is connected to a propeller, which is positioned in the water. The engine's energy is transferred to the propeller, creating a high-speed jet of water that propels the boat forward. This design allows for exceptional maneuverability and high-speed capabilities, making turbining boats popular for recreational activities and racing.
What You'll Learn
- Engine Power: Turbines convert engine power into forward motion
- Propeller: Propeller design and rotation create thrust
- Water Flow: Turbines harness water flow to generate power
- Hydrodynamics: Boat shape and hull design optimize water flow
- Control Systems: Throttle, steering, and trim systems control boat movement
Engine Power: Turbines convert engine power into forward motion
The process of converting engine power into forward motion is a crucial aspect of how turbined boats propel themselves through water. At the heart of this mechanism are turbines, which play a pivotal role in harnessing the energy generated by the engine and transforming it into the force that drives the boat ahead. When a boat's engine operates, it produces a significant amount of power, which is typically in the form of rotational energy. This energy is then directed towards the turbine, a device specifically designed to capture and utilize this power.
Within the turbine, the rotational force is transferred to a series of blades, often arranged in a circular pattern. These blades are carefully angled and shaped to optimize the conversion of energy. As the engine's power rotates the turbine, it causes the blades to spin rapidly. This spinning motion is a direct result of the engine's power being harnessed and directed through the turbine's intricate design.
The key to the turbine's functionality lies in its ability to multiply the engine's power. Through a process known as 'torque multiplication', the turbine increases the rotational speed and force, creating a more powerful output. This amplification of power is essential for propelling the boat forward, as it provides the necessary thrust to overcome water resistance and move the vessel efficiently. The turbine's design ensures that the engine's power is not only harnessed but also optimized for the specific requirements of the boat's propulsion system.
In the context of turbined boats, the turbine's role is to ensure a seamless and efficient transfer of power from the engine to the propeller. The propeller, connected to the turbine's output shaft, then converts this power into the forward motion of the boat. This intricate process showcases the engineering brilliance behind turbined propulsion systems, allowing boats to achieve high speeds and efficient performance on the water.
Understanding the mechanics of engine power conversion through turbines is fundamental to appreciating the capabilities of turbined boats. This technology enables vessels to navigate waters with enhanced speed and agility, making it a significant advancement in marine propulsion. By optimizing the engine's power and directing it through the turbine, these boats can achieve impressive performance, all while demonstrating the precision and innovation inherent in modern marine engineering.
Best Situations to Use a Plow Boat Anchor
You may want to see also
Propeller: Propeller design and rotation create thrust
A propeller is a crucial component of a turbining boat's propulsion system, responsible for generating the necessary thrust to move the vessel forward. The design and functionality of a propeller are intricate and play a significant role in the boat's performance and efficiency.
Propeller design involves careful consideration of various factors. The shape and size of the propeller blades are critical, as they determine the amount of lift and thrust produced. Propellers typically have a curved or twisted blade profile, which helps to create a pressure differential between the forward and rear surfaces of the blade. This pressure difference generates lift, similar to an airplane's wing, allowing the propeller to push water backward and, consequently, move the boat forward. The angle of attack, which is the angle at which the propeller blade meets the oncoming water flow, is also crucial. Adjusting this angle can optimize thrust and efficiency.
The rotation of the propeller is another essential aspect. Propellers rotate in a specific direction, often counterclockwise in the Northern Hemisphere and clockwise in the Southern Hemisphere, due to the right-hand rule. This rotation creates a vortex of water, which is deflected to one side, resulting in a forward force on the boat. The direction of rotation is carefully designed to ensure that the propeller's thrust aligns with the boat's desired direction of travel.
Propeller design also takes into account factors such as blade pitch, which refers to the angle of the blades relative to the propeller axis. Blade pitch can be adjusted to control the speed of the propeller and, consequently, the boat's speed. Propellers with adjustable blade pitch can optimize performance in different water conditions and speeds. Additionally, the number of blades on a propeller can vary, with three, four, or more blades being common designs. Each blade configuration has its advantages and trade-offs in terms of thrust, efficiency, and noise.
In summary, the propeller's design and rotation are key elements in the propulsion of a turbining boat. By carefully engineering the propeller's shape, angle of attack, and rotation direction, engineers can create a powerful and efficient thrust system. This enables the boat to navigate through water with the desired speed and maneuverability, making the propeller a vital component in marine transportation and recreational boating.
Claiming Abandoned Boats: Texas Title Procedures
You may want to see also
Water Flow: Turbines harness water flow to generate power
Water flow is a powerful force that can be harnessed to generate electricity, and this is where turbines come into play. These mechanical devices are designed to convert the kinetic energy of moving water into electrical power, offering a sustainable and renewable energy source. The process begins with the understanding that the flow of water possesses a significant amount of energy, which can be captured and utilized.
Turbines are strategically positioned in water bodies, such as rivers, dams, or even the ocean, where the water's velocity is optimal for power generation. The design of these turbines is crucial, as they must be able to withstand the force of the water while efficiently capturing its energy. Typically, turbines are designed with blades that are angled and shaped to optimize the capture of water flow. As the water flows past these blades, it creates a lift force, similar to how an airplane's wings generate lift. This lift force causes the turbine blades to rotate, initiating the power generation process.
The rotation of the turbine blades is connected to a generator, which is the heart of the power generation system. The generator converts the mechanical energy of the rotating blades into electrical energy through the principles of electromagnetic induction. This process involves the movement of a conductor (such as a coil of wire) within a magnetic field, producing an electric current. The faster the turbine blades rotate, the more electrical power is generated.
One of the key advantages of using water flow to generate power is the consistency and reliability of the resource. Unlike some renewable energy sources, such as wind or solar, water flow is predictable and consistent, especially in areas with well-defined water bodies. This predictability allows for better planning and management of energy production, ensuring a stable supply of electricity. Additionally, the environmental impact of water-based power generation is generally considered low, making it an attractive option for sustainable energy solutions.
In the context of a 'turbing boat', the concept is similar, but the application is different. A turbing boat, or a water turbine boat, is a vessel equipped with turbines that can harness the water flow while the boat is in motion. This design allows for power generation even when the boat is moving through a river or a canal. The turbines are strategically placed to capture the water flow from different angles, ensuring optimal energy capture. This technology can be particularly useful for powering boats or ships, providing a sustainable energy source for transportation.
Unraveling the Mechanics: How Ferry Boats Work
You may want to see also
Hydrodynamics: Boat shape and hull design optimize water flow
The design of a boat's hull is a critical factor in its ability to generate thrust and move efficiently through water. The hull, which is the main body of the boat, is shaped to optimize water flow and reduce drag. This is achieved through a process called hydrodynamics, which involves the study of how water flows around and under the boat.
The shape of the hull is designed to create a smooth, continuous flow of water over the boat's surface. This is done by using a series of curves and contours that guide the water around the boat, reducing turbulence and drag. The hull is also designed to create a pressure differential between the front and back of the boat, with the front of the boat experiencing higher pressure than the back. This pressure differential creates a force that pushes the boat forward, known as thrust.
The hull's design also takes into account the concept of displacement, which is the amount of water that the boat displaces as it moves through the water. The displacement of water is directly related to the boat's weight and the amount of water that it displaces. By optimizing the displacement of water, the boat can move more efficiently through the water, reducing the amount of energy required to move the boat.
In addition to the hull's shape, the design of the boat's propeller also plays a crucial role in its ability to generate thrust. The propeller is designed to create a vortex of water that is directed backward, which creates a force that pushes the boat forward. The propeller's design also takes into account the concept of cavitation, which is the formation of bubbles in the water as the pressure drops. Cavitation can cause damage to the propeller and the boat's hull, so the propeller's design is optimized to minimize the formation of bubbles.
The hydrodynamics of a boat's design is a complex process that involves the study of fluid dynamics, aerodynamics, and structural engineering. By optimizing the shape of the hull and the design of the propeller, boat designers can create a vessel that is efficient, fast, and capable of generating thrust in a variety of water conditions.
Painting Your John Boat: A Step-by-Step Guide
You may want to see also
Control Systems: Throttle, steering, and trim systems control boat movement
The control systems of a turbining boat are crucial for its maneuverability and performance, allowing operators to navigate efficiently and respond to various conditions. These systems work in harmony to ensure the boat's movement is precise and controlled.
Throttle System:
The throttle system is the primary mechanism for controlling the boat's speed. It operates the engine's throttle valves, which regulate the airflow into the engine. By adjusting the throttle, the operator can increase or decrease the engine's power output. This system is typically electronic or hydraulic, with a control pedal or lever that the operator uses to modulate the engine's speed. When the throttle is fully open, the boat accelerates, and when closed, it decelerates. Modern turbining boats often feature advanced throttle controls, such as cruise control and speed limiters, to ensure safe and efficient operation.
Steering System:
Steering is essential for directing the boat's movement. Turbining boats employ a steering system that connects the helm (the operator's position) to the boat's rudders or propellers. There are two main types: traditional mechanical steering and power-assisted steering. In mechanical steering, the operator turns the wheel or tiller, which physically moves the steering gear, connecting to the rudders via cables or hydraulic lines. Power-assisted steering, on the other hand, uses an electric motor or hydraulic pump to assist the operator in turning the wheel, making it easier to maneuver, especially at high speeds or when loaded with cargo.
Trim System:
Trim systems are designed to adjust the boat's stability and performance by altering its trim (the angle of the hull relative to the waterline). This system uses actuators or pumps to move the boat's weight, typically the engine or fuel tanks, forward or backward. By adjusting the trim, the boat can be optimized for different water conditions, such as planing, cruising, or deep-water operation. For example, a boat can be trimmed to achieve a flatter hull for better stability at speed or a more upright position for better performance in shallow waters.
These control systems work in conjunction with each other. The throttle controls the boat's speed, steering directs its path, and trim adjusts its stability. Modern turbining boats often feature integrated control panels, allowing operators to adjust these systems simultaneously. This integration ensures that the boat's movement is responsive and controlled, providing a seamless driving experience. Additionally, advanced control systems may include features like automatic trim adjustment, which optimizes the boat's performance without operator intervention.
Becoming a Tug Boat Driver: Australia's Requirements and Pathways
You may want to see also
Frequently asked questions
A turbofan engine, also known as a marine turbofan, is a type of propulsion system used in boats and ships. It works by compressing air and mixing it with fuel, which is then ignited to create a high-pressure, high-temperature gas. This gas is directed through a turbine, which rotates at high speeds, driving a propeller or other mechanical components. The turbofan engine's efficiency and power make it a popular choice for recreational and commercial vessels, offering a balance between speed, fuel consumption, and maintenance.
Turbomachinery systems are integral to a boat's propulsion system, especially in larger vessels. These systems consist of a compressor, a turbine, and a shaft, all working in harmony. The compressor takes in air and increases its pressure, while the turbine extracts energy from the exhaust gases, driving the compressor and the propeller shaft. This process creates a continuous flow of high-pressure air, resulting in efficient propulsion. Turbomachinery systems are known for their reliability and ability to provide consistent performance, making them a preferred choice for marine applications.
A turbopump is a critical component in a boat's propulsion system, particularly in high-speed vessels. It is essentially a combination of a compressor and a pump, designed to increase the pressure of the fluid (usually water or fuel) to create thrust. The turbopump works by accelerating the fluid through a series of rotating and stationary blades, which compress and accelerate the fluid. This high-pressure fluid is then directed towards the propeller, providing the necessary force for propulsion. Turbopumps are known for their ability to handle high-pressure and high-temperature environments, making them suitable for powerful and efficient marine applications.