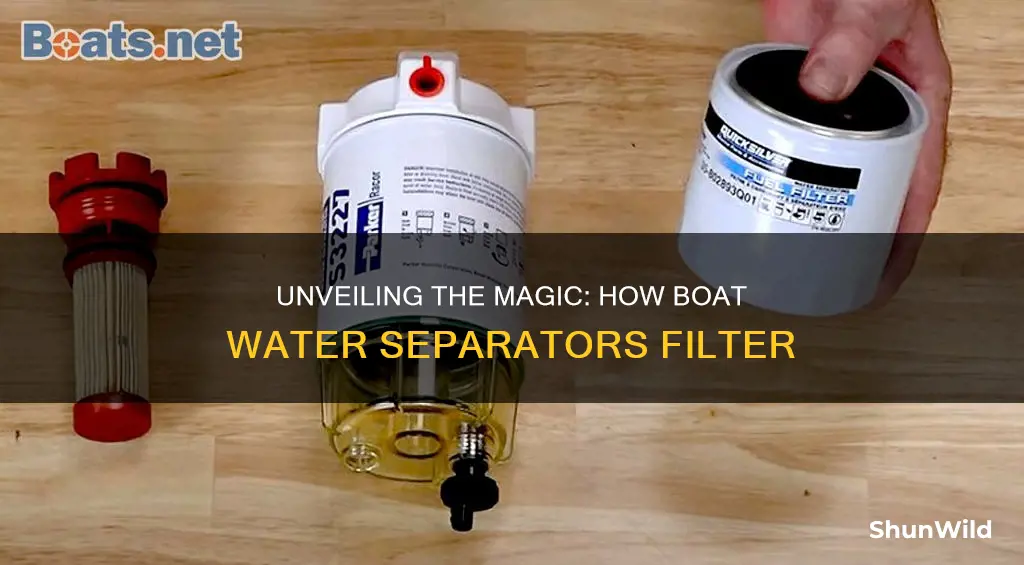
A boat water separator filter is an essential component for any vessel that relies on freshwater systems. This device plays a crucial role in maintaining the quality and safety of drinking water by removing contaminants and impurities from the water supply. The primary function of a water separator filter is to separate waterborne particles and pollutants, ensuring that the water is clean and safe for consumption. This process involves a series of intricate mechanisms that effectively trap and remove debris, sediment, and other unwanted substances. Understanding the inner workings of this filter is key to appreciating its importance in marine environments, where access to clean water is vital for the well-being of both passengers and the vessel's systems.
Characteristics | Values |
---|---|
Function | Removes water from fuel to prevent engine damage |
Design | Typically a cylindrical or cylindrical-cone shape with a filter element |
Material | Plastic or metal housing, pleated paper or fabric filter element |
Capacity | Varies, typically 1-5 gallons per minute |
Installation | Usually mounted near the fuel tank or engine |
Maintenance | Regular cleaning and replacement of the filter element |
Applications | Marine engines, small boats, recreational vehicles |
Advantages | Protects fuel system, extends engine life, reduces fuel consumption |
Disadvantages | Can be prone to clogging, requires periodic maintenance |
Types | Mechanical, coalescing, sediment filters |
Filtration Process | Fuel passes through the filter, water droplets are separated and collected |
Indicator | Some models have a visual indicator for when the filter needs cleaning |
What You'll Learn
- Physical Barriers: Boats use screens and filters to trap large particles
- Centrifugal Force: Spin filters separate water from contaminants using centrifugal force
- Chemical Treatment: Chemical processes neutralize contaminants, making them easier to remove
- Sedimentation: Gravity-based method where contaminants settle at the bottom of the separator
- Microfiltration: Tiny pores trap microscopic particles, ensuring clean water
Physical Barriers: Boats use screens and filters to trap large particles
Boats, especially those used for marine or freshwater applications, often require effective water separation systems to maintain the quality of their fuel and engine oil. One crucial component of these systems is the physical barrier, which employs screens and filters to trap large particles and contaminants. This method is a fundamental principle in water separation technology and is designed to prevent the passage of larger particles while allowing cleaner water to pass through.
Physical barriers are typically constructed using fine mesh screens or filters with very small openings. These screens are strategically placed in the water flow path, often in the form of a cylindrical or conical filter element. The key to their effectiveness lies in their ability to physically block larger particles, such as sediment, rust, and other debris, while allowing water to pass through. When water enters the system, it encounters these screens, and the larger particles get physically trapped, preventing them from continuing downstream.
The design and placement of these screens are critical to their performance. Filters are often designed with specific mesh sizes, ensuring that particles larger than the mesh size are retained, while smaller particles and water molecules can pass through. This process is similar to how a sieve separates solids from liquids, but on a much smaller scale. The screens are typically made from durable materials like stainless steel or specialized synthetic fibers to ensure longevity and resistance to corrosion.
In a boat's water separation system, these physical barriers are often part of a multi-stage filtration process. After the initial screening, further filtration steps may involve carbon blocks or sediment traps to capture even smaller particles. This multi-stage approach ensures that the water is thoroughly cleaned, providing a reliable source of clean water for the boat's engine and other critical systems. Regular maintenance, including filter replacement, is essential to ensure the system's continued effectiveness.
By utilizing physical barriers, boats can maintain the integrity of their fuel and engine oil, ensuring optimal performance and longevity. This method is a cost-effective and environmentally friendly approach to water separation, as it does not require chemical treatments or complex processes, making it a popular choice for various marine applications. Understanding the mechanics of these physical barriers is essential for boat owners and operators to ensure their water separation systems function optimally.
The Evolution of Show Boat Musical
You may want to see also
Centrifugal Force: Spin filters separate water from contaminants using centrifugal force
Centrifugal force is a powerful tool in the world of water filtration, especially for boat water separators. These filters utilize the principle of centrifugal force to separate water from contaminants, ensuring that the water on board remains clean and safe for use. Here's how it works:
When water enters the spin filter, it is directed into a spinning chamber. This chamber is designed to create a high-speed rotational flow of water. As the water spins, it experiences centrifugal force, which pushes the contaminants and larger particles outward, away from the center of the chamber. The force is strong enough to separate even the smallest particles, ensuring that the water remains clear and free from debris. The design of the filter's internal components, including the spinning mechanism and the collection chamber, is crucial to its efficiency.
The spinning motion causes the contaminants to move in a circular path, eventually settling at the bottom of the chamber. This separation process is rapid and effective, allowing for a continuous flow of clean water. The filter's housing is typically made of durable materials to withstand the high-speed rotation and the pressure of the water flow.
One of the key advantages of using centrifugal force is its ability to handle a large volume of water quickly. This makes it ideal for boats, where a steady supply of clean water is essential for various operations. The filter can be designed to accommodate different flow rates, ensuring that it meets the specific needs of the boat's water system.
In summary, centrifugal force-based spin filters are an efficient and reliable method for separating water from contaminants in boat water systems. By utilizing the power of spinning motion, these filters provide a continuous supply of clean water, contributing to the overall safety and functionality of the vessel. Understanding the mechanics of these filters is essential for anyone looking to maintain a reliable water supply on their boat.
Transferring Boat Registration in Georgia: A Comprehensive Guide
You may want to see also
Chemical Treatment: Chemical processes neutralize contaminants, making them easier to remove
Chemical treatment is a crucial process in water separation systems, especially for boats, as it plays a vital role in ensuring the effectiveness of the filtration process. When water enters the separator, it often contains various contaminants, including oils, grease, fuel, and other organic compounds. These substances can be challenging to remove through physical separation alone, especially when they are present in low concentrations. This is where chemical treatment comes into play.
The primary goal of chemical treatment is to neutralize or alter the chemical properties of contaminants, making them more susceptible to removal. This is typically achieved through the use of specific chemicals that react with the target contaminants. For instance, one common chemical treatment method is the addition of coagulants and flocculants. Coagulants, such as aluminum salts (e.g., aluminum sulfate), are added to the water to neutralize the electrical charge of contaminants, causing them to lose their ability to repel each other. This process is known as coagulation. Flocculants, on the other hand, are used to promote the formation of small, dense particles called flocs. These flocs are easier to separate from the water due to their increased size and weight.
When coagulants and flocculants are introduced into the water, they initiate a series of chemical reactions. The contaminants, which may be in the form of fine particles or emulsions, start to aggregate and form larger flocs. This process is often facilitated by the mixing and agitation provided by the separator's internal components. As the flocs grow, they become heavy enough to settle at the bottom of the separator, allowing for their separation from the clean water. This settling process is known as sedimentation.
The effectiveness of chemical treatment relies on careful selection and dosage of the chemicals used. Different contaminants require specific chemical agents to neutralize their properties. For example, oil and grease may require different coagulants compared to fuel or organic matter. The treatment process also involves monitoring the pH level of the water, as it can affect the chemical reactions and the overall efficiency of the separation. Adjusting the pH may be necessary to optimize the treatment.
After the chemical treatment process, the water is typically directed to a sedimentation basin or a filtration unit. Here, the flocs settle, and the clean water is separated from the contaminants. This treated water can then be discharged or further processed for reuse on the boat. Chemical treatment is a critical step in the overall water separation process, ensuring that the filter can effectively capture and remove contaminants, providing clean and safe water for various boat operations.
The Boys in the Boat: Were They Really Late?
You may want to see also
Sedimentation: Gravity-based method where contaminants settle at the bottom of the separator
Sedimentation is a fundamental process in boat water separators, offering a simple yet effective method to separate contaminants from water. This gravity-based technique relies on the natural tendency of particles to settle at the bottom of a container, allowing for the separation of water and its impurities. When water enters the separator, it is directed into a chamber designed to facilitate this process. The key principle is that contaminants, such as sediments, dirt, and other suspended particles, will naturally settle due to their weight and the force of gravity.
As the water flows through the separator, the velocity decreases, especially near the bottom of the chamber. This reduction in velocity, combined with the upward flow of cleaner water, creates a gentle upward current. The contaminants, being denser, are drawn downward by gravity, gradually settling at the bottom of the separator. This process effectively separates the water from the unwanted particles, leaving behind relatively clean water.
The sedimentation process is a passive method, meaning it does not require any mechanical action or external power source. It is a natural and cost-effective way to remove sediments and other larger particles from the water. The efficiency of this method depends on factors such as the initial water quality, the size of the separator, and the specific gravity of the contaminants. Larger and more dense particles will settle more rapidly, while finer particles may require additional filtration methods to achieve complete separation.
In a boat water separator, the sedimentation chamber is typically designed with a sloped bottom, allowing the settled contaminants to accumulate at a specific location. This accumulation can be periodically removed, ensuring the separator's continuous operation. The separated water can then be directed back into the boat's water system or stored for further treatment or use. This gravity-based approach is a crucial component of boat water filtration systems, providing a simple yet reliable means of maintaining clean and safe water supplies.
Understanding the sedimentation process is essential for optimizing the performance of boat water separators. By allowing contaminants to settle naturally, this method contributes to the overall efficiency of the filtration system, ensuring that the water supplied to the boat's systems is free from visible sediments and other large particles. This process, combined with other filtration techniques, plays a vital role in providing clean and potable water for various onboard applications.
Exploring the 2005 Regal: A Boat Overview
You may want to see also
Microfiltration: Tiny pores trap microscopic particles, ensuring clean water
Microfiltration is a crucial process in water purification systems, especially in the context of boat water separators. It involves the use of extremely small pores, typically measured in nanometers, to filter out contaminants from water. These tiny pores act as a physical barrier, allowing water molecules to pass through while effectively trapping microscopic particles, including bacteria, viruses, and other impurities.
The concept behind microfiltration is based on the size exclusion principle. Water molecules, being much smaller than the pores, can easily pass through, ensuring that the filtered water remains clean and safe for various purposes. However, particles larger than the pore size are physically blocked, preventing their entry into the clean water stream. This method is highly effective in removing a wide range of contaminants, making it an essential component of boat water separators.
In a boat water separator, microfiltration is often employed in conjunction with other filtration techniques to achieve comprehensive water purification. The process begins with water entering the separator, where it passes through a series of filters with varying pore sizes. The microfiltration stage specifically targets microscopic particles, ensuring that the water is free from visible contaminants and harmful microorganisms. This is particularly important for boats, where access to clean water is essential for drinking, cooking, and sanitation.
The design of microfiltration membranes is critical to their efficiency. These membranes are engineered to have precise pore sizes, ensuring that only the desired particles are removed. For instance, a membrane with a pore size of 0.2 micrometers will trap bacteria and other microorganisms while allowing clean water to pass through. This level of precision is made possible by advanced manufacturing techniques, ensuring that the filtration process is highly effective and reliable.
By utilizing microfiltration, boat water separators can provide a consistent supply of clean water, even in challenging environments. This technology is a cornerstone of water purification systems, offering a practical solution for maintaining water quality on boats and in various other applications where access to clean water is critical. Its ability to trap microscopic particles ensures that the water remains safe and suitable for a wide range of uses.
Understanding Drive Gear Cases in Boats
You may want to see also
Frequently asked questions
A boat water separator filter is a device designed to remove water and contaminants from the engine's cooling system, ensuring that only clean engine oil circulates through the engine. It is an essential component for maintaining engine performance and longevity, especially in marine environments where water intrusion is common.
The filter operates based on the principle of centrifugal separation. When the boat's engine is running, the separator is activated, creating a spinning motion that separates water and contaminants from the engine oil. The spinning action causes the water droplets to move outward and separate from the oil, which remains in the center.
The separator effectively removes water, air bubbles, and small particles like dirt, rust, and other foreign matter. It ensures that the engine oil remains clean and free-flowing, preventing potential damage to engine components caused by water corrosion and excessive wear.
The replacement frequency depends on various factors, including the boat's usage, environmental conditions, and the separator's design. As a general guideline, it is recommended to replace the filter every 50-100 hours of engine operation or annually, whichever comes first. Regular maintenance ensures optimal performance and extends the life of the engine.
Yes, boat water separator filters are versatile and can be used in various boat types, including powerboats, sailboats, and personal watercraft. They are particularly useful in areas with high humidity or where the boat is frequently exposed to water, such as during docking or in rough seas.