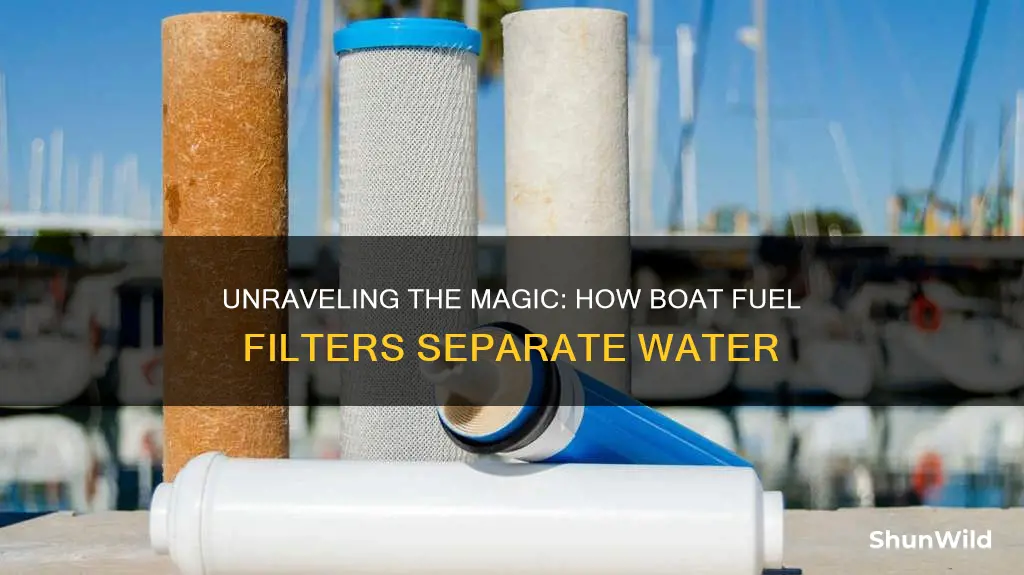
A boat water-separating fuel filter is a crucial component in the maintenance of marine engines, designed to protect the fuel system from contamination. This innovative filter system is specifically engineered to separate water and contaminants from the fuel, ensuring a clean and reliable fuel supply for the engine. By effectively removing water and other impurities, the filter helps prevent engine damage caused by corrosion and the formation of fuel emulsions. Understanding the mechanism behind this filter is essential for boat owners and operators to maintain optimal engine performance and longevity.
Characteristics | Values |
---|---|
Function | Removes water and contaminants from fuel to prevent engine damage |
Design | Typically a two-stage process: a mechanical filter and a carbon adsorption stage |
Mechanical Filter | Captures large particles and debris using a pleated media |
Carbon Adsorption | Utilizes activated carbon to attract and trap water and small particles |
Capacity | Varies depending on the model, but can handle large volumes of fuel |
Maintenance | Regular cleaning and replacement of filter elements required |
Applications | Ideal for boats, marine engines, and other fuel systems where water contamination is a concern |
Advantages | Ensures cleaner fuel, extends engine life, and reduces the risk of engine failure |
Disadvantages | May require periodic maintenance and can be more expensive than standard filters |
What You'll Learn
- Filter Media: Specialized materials trap contaminants, ensuring clean fuel
- Separation Process: Gravity and centrifugal forces separate water from fuel
- Fuel Flow Control: Valves regulate fuel flow, preventing water entry into the engine
- Water Detection: Sensors identify water presence, triggering alerts or shutdowns
- Maintenance: Regular cleaning and replacement ensure optimal performance
Filter Media: Specialized materials trap contaminants, ensuring clean fuel
The heart of a boat water-separating fuel filter is its filter media, a crucial component designed to trap and remove contaminants from the fuel. This specialized material is engineered to effectively capture water, sediment, and other impurities, ensuring that only clean fuel reaches the engine. The filter media's performance is key to maintaining engine health and longevity, especially in marine environments where water and fuel contamination are common issues.
Various materials can be used for this purpose, each with unique properties that make them suitable for different filtering needs. One common material is a synthetic fiber, often made from polypropylene or polyester. These fibers are highly effective at trapping small particles and moisture due to their fine mesh structure and large surface area. The fibers are arranged in a specific pattern, creating a network that allows fuel to pass through while capturing contaminants. This design ensures that even tiny particles and water droplets are trapped, preventing them from entering the engine.
Another type of filter media is a multi-layer filter element, which consists of multiple layers of different materials. For instance, a layer of pleated synthetic fibers might be followed by a layer of metal mesh or a fine-mesh screen. This multi-layer approach provides a more comprehensive filtration process, capturing a wide range of contaminants. The metal mesh, for example, can trap larger particles, while the synthetic fibers handle smaller impurities, ensuring a thorough cleaning of the fuel.
In some cases, activated carbon is used in the filter media. This material is highly effective at adsorbing contaminants, particularly water vapor and organic compounds. By incorporating activated carbon, the filter can remove volatile organic compounds (VOCs) and ensure that the fuel is not only clean but also free from harmful chemicals. This is especially important in marine applications where fuel quality can vary significantly.
The choice of filter media depends on factors such as the engine's requirements, the type of fuel used, and the specific environmental conditions. For instance, in areas with high humidity, a filter with a strong moisture-trapping capacity might be preferred. Similarly, in regions with dusty environments, a filter with a robust particle-trapping mechanism is essential. By selecting the right filter media, boat owners can ensure that their engines receive the cleanest possible fuel, leading to improved performance, reduced maintenance, and a longer engine lifespan.
Boat Traffic on the Illinois River: Open or Closed?
You may want to see also
Separation Process: Gravity and centrifugal forces separate water from fuel
The process of separating water from fuel in a boat's water-separating fuel filter is a crucial aspect of maintaining a vessel's engine performance and longevity. This system relies on the principles of gravity and centrifugal forces to effectively remove water and contaminants from the fuel, ensuring optimal combustion and engine operation.
When the fuel enters the filter, it is directed into a chamber where gravity plays a significant role in the separation process. The fuel's natural tendency to flow downward allows heavier particles and water droplets to settle at the bottom of the chamber. This initial gravity-based separation helps to remove larger contaminants and water, preventing them from entering the engine's fuel system. The design of the filter often includes a screen or mesh that captures these particles, ensuring they are effectively trapped and not drawn into the engine.
As the fuel continues its journey through the filter, centrifugal forces come into play. The filter's design incorporates a spinning mechanism, typically a rotor or impeller, which rotates rapidly. This rotation creates a centrifugal field that forces the fuel to move outward, away from the center of the filter. During this process, any remaining water droplets and smaller particles are separated from the fuel stream. The centrifugal force causes the water and contaminants to move in a circular pattern, eventually exiting the filter through a separate outlet.
The key to the success of this separation technique lies in the careful engineering of the filter's components. The rotor or impeller must be precisely balanced to ensure smooth and efficient rotation. Additionally, the filter's housing and internal components are designed to withstand the high-speed rotation and provide a stable environment for the separation process. This attention to detail ensures that the fuel remains clean and free of water, even under varying operating conditions.
In summary, the water-separating fuel filter on a boat utilizes gravity and centrifugal forces to effectively remove water and contaminants from the fuel. Gravity aids in the initial separation, allowing heavier particles to settle, while the spinning mechanism employs centrifugal forces to further refine the process. This combination of physical principles ensures that the fuel supplied to the engine is clean and free-flowing, contributing to improved performance and engine longevity.
Mastering the Art of Driving a Moomba Boat
You may want to see also
Fuel Flow Control: Valves regulate fuel flow, preventing water entry into the engine
In marine environments, ensuring the proper functioning of a boat's fuel system is crucial for safe and efficient operation. One critical component that plays a vital role in maintaining the quality of fuel is the water-separating fuel filter. This filter is designed to prevent water and contaminants from entering the engine, which could lead to significant performance issues and potential damage. The primary function of this filter is to separate water and debris from the fuel, ensuring that only clean, dry fuel reaches the engine.
The mechanism behind this filter's effectiveness lies in its design and functionality. When fuel is supplied to the engine, it passes through the water-separating filter. This filter typically consists of a series of screens and separators that work together to capture and remove water droplets and small particles. The process begins with the fuel entering a chamber where it is agitated, allowing water to separate from the fuel due to its lower density. This initial separation step is crucial as it prevents water from being drawn into the engine along with the fuel.
As the fuel continues its journey through the filter, it encounters various filtration media. These media can include pleated filters, screens, or even specialized materials designed to attract and trap water. The fuel's flow rate is carefully controlled to ensure optimal filtration. Valves play a critical role in this process, acting as gatekeepers to regulate the fuel's passage. These valves are strategically positioned to monitor and control the fuel flow, ensuring that any water or contaminants are effectively trapped and removed.
The valves used in this system are designed to be highly sensitive and responsive. They are typically solenoid-operated, allowing for precise control. When the engine is running, the valves remain open, allowing fuel to flow freely. However, when the engine is not in use or during periods of inactivity, the valves can be closed to prevent any potential water intrusion. This automatic closure mechanism is essential for maintaining the engine's longevity and performance, especially during extended periods of non-operation.
In summary, the water-separating fuel filter is a critical component in a boat's fuel system, ensuring that only clean, dry fuel reaches the engine. The use of valves in this system allows for precise control of fuel flow, preventing water entry and potential engine damage. By understanding the inner workings of this filter and its associated valves, boat owners can better appreciate the importance of regular maintenance and the role of these components in keeping their vessels running smoothly and reliably.
Miami to Grand Cayman: A Boat Trip Adventure
You may want to see also
Water Detection: Sensors identify water presence, triggering alerts or shutdowns
Water detection systems are an essential safety feature in marine environments, especially for boats, where the presence of water in the fuel system can lead to significant issues. These systems are designed to identify and alert the operator to any water intrusion, ensuring prompt action to prevent potential engine damage. The core of this technology lies in the use of specialized sensors that can detect even minute amounts of water, which is crucial for the overall safety and longevity of the vessel.
The sensors employed in water detection systems are typically designed to respond to the unique properties of water. These sensors can identify water-specific characteristics, such as its electrical conductivity or dielectric properties, which are significantly different from those of fuel. When water is present in the fuel, these sensors can detect the change and trigger an alert or, in some cases, initiate a shutdown of the engine to prevent any potential catastrophic failures. This real-time monitoring capability is vital for maintaining the integrity of the fuel system.
One common type of sensor used in water detection is the conductivity sensor. These sensors measure the electrical conductivity of the fuel-water mixture. Pure fuel has a low electrical conductivity, but when water is introduced, the mixture's conductivity increases. By monitoring this change, the sensor can accurately detect the presence of water. Another approach is the use of dielectric sensors, which measure the dielectric constant of the fuel, which changes when water is present. These sensors provide a rapid and reliable method of identifying water contamination.
In addition to triggering alerts, some water detection systems are programmed to initiate automatic shutdowns of the engine upon detecting water. This is a critical safety feature, especially in high-risk scenarios where water intrusion could lead to engine damage or failure. The shutdown mechanism ensures that the engine is not subjected to potentially harmful conditions, thus preventing costly repairs and potential breakdowns. This automated response is a key advantage of modern water detection technology.
The effectiveness of water detection systems relies on regular maintenance and calibration. Sensors should be checked and calibrated periodically to ensure they are functioning correctly. This includes cleaning the sensors to remove any debris or contaminants that might interfere with their performance. Proper maintenance ensures that the system remains reliable and accurate, providing an effective layer of protection against water-related engine issues.
Exploring Hawaii and Florida: A Boating Adventure's Distance
You may want to see also
Maintenance: Regular cleaning and replacement ensure optimal performance
Regular maintenance is crucial to ensure the efficient operation of a boat's water-separating fuel filter. Over time, these filters can accumulate contaminants, including water, sediment, and debris, which can lead to reduced performance and potential engine issues. Therefore, it is essential to establish a routine maintenance schedule to keep the filter in optimal condition.
One critical aspect of maintenance is regular cleaning. The filter should be cleaned periodically to remove any built-up contaminants. This process typically involves draining the fuel tank and then carefully cleaning the filter element. It is important to use the appropriate cleaning agents and methods to avoid damaging the filter media. For instance, using a mild detergent solution can help dissolve and remove any stubborn deposits. After cleaning, ensure that the filter is thoroughly rinsed to eliminate any residual cleaning agents, as these can attract moisture and cause further contamination.
In addition to cleaning, regular replacement of the filter is vital. Boat fuel filters often have a limited lifespan, and over time, the filter media can become saturated with contaminants. When this happens, the filter's ability to separate water and debris from the fuel diminishes. To maintain optimal performance, it is recommended to replace the filter at regular intervals, typically every 50-100 hours of operation, depending on the specific make and model. Keep a record of the replacement schedule to ensure you don't overlook this important maintenance task.
During the replacement process, it is essential to handle the filter with care. Start by disconnecting the fuel lines and allowing any residual pressure to dissipate. Then, carefully remove the old filter, being mindful of any debris that may have accumulated around it. Inspect the filter housing for any signs of damage or wear and ensure it is clean before installing the new filter. When replacing the filter, follow the manufacturer's instructions to ensure proper orientation and secure it firmly in place.
By adhering to a regular cleaning and replacement schedule, boat owners can significantly extend the life of their fuel filters and maintain the overall health of their engines. This proactive approach to maintenance helps prevent costly repairs and ensures a reliable power source for boating adventures. Remember, proper maintenance is key to enjoying a smooth and safe boating experience.
Bass Boat Hulls: Waxing is a Bad Idea
You may want to see also
Frequently asked questions
A boat water-separating fuel filter is an essential component in a vessel's fuel system, designed to remove water and contaminants from the fuel, ensuring optimal engine performance and longevity. It is particularly crucial in marine environments where water can easily enter the fuel system through various sources like condensation, seepage, or accidental spillage.
This filter operates based on the principle of gravitational separation. It consists of a cylindrical housing with a series of baffles or plates inside. When fuel is drawn from the tank, it passes through the filter, and the water droplets, due to their higher density, tend to settle at the bottom of the housing. The clean fuel then rises and exits through the top, while the water remains trapped at the bottom, often with a drain valve for periodic removal.
Yes, regular maintenance is necessary to keep the filter efficient. Boat owners should regularly check the filter for any signs of excessive water accumulation, which may indicate a blocked drain or a faulty filter. Cleaning or replacing the filter element at recommended intervals is also essential to prevent clogs and ensure proper water separation. Proper maintenance will help maintain engine performance and avoid potential issues caused by contaminated fuel.