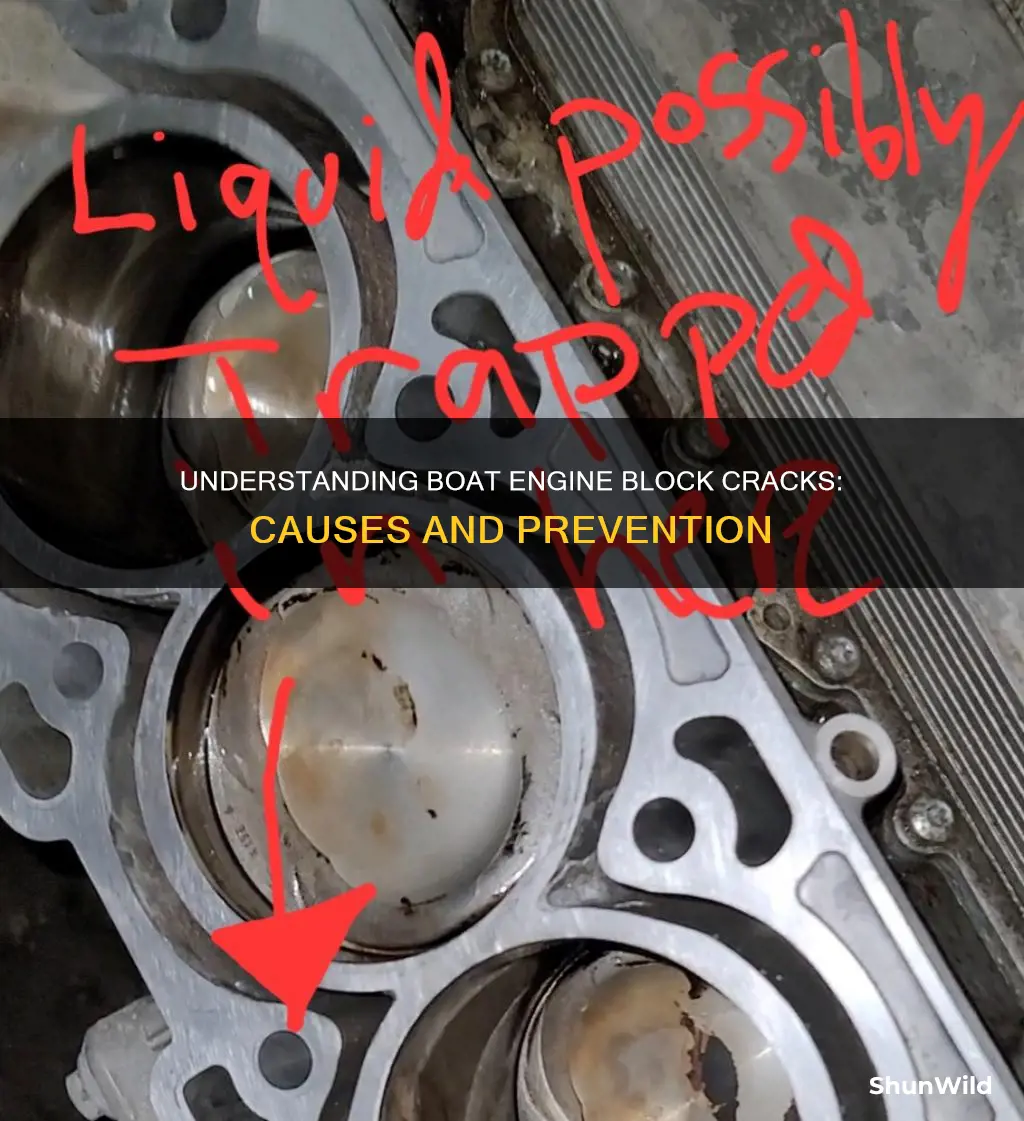
A cracked engine block on a boat can hinder its performance and lead to poor efficiency. While cracks in the engine block are uncommon, they are one of the most devastating problems boats face, especially older ones. Engine block cracks are usually caused by excess heat, which is often due to a problem with the coolant. If the crack is not too severe, repairs can be made by sealing the damage to prevent oil or coolant from leaking. However, not all cracks are repairable, and a replacement block or new engine may be necessary. Boat owners should be vigilant about troubleshooting and maintaining their boats to prevent such issues.
Characteristics | Values |
---|---|
Signs of a cracked engine block | Visible smoke in the cabin, overheating of the engine, compromised performance, milky-white oil, oil leak |
Causes of a cracked engine block | Excess heat, poor storage, malfunctioning water pump, manufacturer error |
Solutions to a cracked engine block | Pinning, glueing, welding, replacement |
What You'll Learn
Welding a cracked engine block
Step 1: Assess the Damage
Before starting any repair work, it is crucial to thoroughly inspect the engine block and identify the extent of the damage. Look for any signs of coolant in the oil, which may appear as a creamy white substance. Additionally, check for oil leaks in the coolant and pay attention to any unusual odours or sounds coming from the engine. These could indicate a more serious issue that may require further attention.
Step 2: Prepare the Area
Once you have confirmed the presence of a crack, it is important to prepare the area for welding. This involves cleaning and beveling the cast iron surface by grinding or using a sanding disk. Creating a bright, shiny surface will ensure optimal penetration of the weld. It is also essential to remove any contaminants, such as oil or grease, from the area to ensure a strong and reliable weld.
Step 3: Pre-heating
Gently pre-heat the cast iron engine block to remove moisture and prevent pinholes and porosity in the weld. This step is crucial as it helps the weld lay flatter when you start your bead. However, be cautious not to overheat the cast iron, as excessive heat can cause warping or further damage. Aim for a temperature of around 300 degrees Fahrenheit or slightly higher.
Step 4: Welding Technique
When welding cast iron, it is recommended to use a standard arc welder with Muggy Weld 77 cast iron welding rods. This type of welding rod is specifically designed for cast iron and provides superior results. Start by tacking a quarter-inch thick mild steel plate over the crack to cover it. Weld side to side to prevent the cast iron from getting too hot and potentially cracking further. Ensure you have good penetration and a strong weld by adjusting the amperage as needed.
Step 5: Post-Welding Care
After completing the weld, cover the engine block with heat-retaining blankets to allow it to cool slowly and evenly. This step is crucial in preventing further cracking or warping of the metal. Once the engine block has cooled, you can proceed to reassemble the engine, ensuring that all components are properly secured and aligned.
Step 6: Testing and Verification
Before considering the repair complete, it is essential to thoroughly test the engine block to ensure the weld holds and there are no leaks. Run the engine and monitor it closely for any signs of coolant or oil leaks. Additionally, listen for any unusual noises that may indicate further issues. If the weld holds and the engine functions properly, you can be confident that the repair was successful.
Replacing Boat Window Screen: A Step-by-Step Guide for Boaters
You may want to see also
Signs of a cracked engine block
A cracked engine block is one of the most serious issues a vehicle owner can face, often requiring a new engine. While it is uncommon for an engine block to crack, it is still possible. Here are some signs that indicate a cracked engine block:
- White smoke from the exhaust pipe: A crack in the engine block can cause coolant to leak into the engine's cylinders, where it is burned during combustion. This will result in white smoke, which is actually steam, coming from the exhaust. The exhaust fumes may also have a sweet smell.
- Coolant or oil leaks: A cracked engine block can result in internal or external coolant and oil leaks. If you notice a puddle of coolant or oil under your car, it could be a sign of a crack.
- Engine overheating: Coolant leaks caused by a cracked engine block can lead to engine overheating. Keep an eye on your engine temperature gauge and if it enters the red zone, it's a sign of overheating.
- Rough running and misfiring: A cracked engine block can cause a loss of compression, leading to rough engine running and misfiring.
- Combustion gases in the cooling system: A cracked engine block may allow combustion gases to enter the cooling system, resulting in an excessive amount of bubbles in the coolant and high pressure in the system.
- Coolant-oil intermix: A crack between the block's oil and coolant passages can result in coolant and oil mixing. This can be identified by the presence of oil in the coolant or a milky substance in the oil.
- Illuminated warning lights: A cracked engine block can trigger warning lights on your dashboard, such as the check engine light, low coolant level light, and engine over-temperature light.
Greta Thunberg's Sail Journey: Diesel or Not?
You may want to see also
Causes of an engine block crack
An engine block crack can occur due to a variety of reasons, with excess heat being the most common cause. Here are some of the main causes of engine block cracks:
Excess Heat
High temperatures in the engine are usually caused by a malfunctioning coolant system. If the coolant system fails, the engine parts that don't receive coolant will overheat, causing the metal to expand. In contrast, the cooler parts of the engine remain at an average temperature. This temperature difference creates thermal stress, which eventually leads to cracks in the engine block.
Poor Winterization and Storage
Improper winterization and storage of your boat during the colder months can also lead to engine block cracks. It is crucial to drain the water from the engine and fill the system with antifreeze to prevent freezing. If the water freezes, it expands and can result in cracks in the engine block.
Malfunctioning Water Pump
A malfunctioning water pump can hinder the flow of coolant, causing the engine to overheat. This, in turn, can lead to thermal stress and engine block cracks.
Manufacturing Defects
In some cases, engine block cracks may be due to manufacturing defects. Improper casting during injection molding can cause thinning of the metal in certain regions. When the engine heats up, these thin sections may not withstand the high temperatures, leading to cracks.
Extreme Cold Temperatures
While it is uncommon, extremely cold temperatures can also lead to engine block cracks. If the engine is not properly winterized and is exposed to freezing temperatures for an extended period, the water inside the engine can freeze and expand, putting enough pressure on the engine block to cause cracks.
It is important to note that while some cracks can be repaired using specialized welding techniques or sealants, others may require a complete engine block replacement.
Best Oils for Boat Lower Units: A Comprehensive Guide
You may want to see also
Fixing a cracked engine block
If you've discovered a crack in your boat's engine block, you may be able to repair it without having to replace the entire engine. Here are some methods to fix a cracked engine block:
Welding
Welding the crack is an option, but it's important to note that welding cast iron effectively is challenging. It requires removing the engine, stripping it to the bare block, preheating the block to around 300 degrees, welding or brazing the break, and then slowly cooling the block before reassembling. Even then, there's no guarantee the repair will last, and it may be more cost-effective to install a new short block.
Epoxy or JB Weld
If the crack is in the water jacket and the oil is clean and not foamy, you can try using epoxy or JB Weld to seal it. However, this is only a temporary solution as the repair will likely fail due to the different expansion rates of the materials. Once the repair fails, it can cause water to leak into the bilge while the engine is running. To improve the chances of success with this method, it's recommended to drill a hole at each end of the crack to prevent further spreading, grind the surface to provide a better bite for the epoxy or weld, and clean the area thoroughly before applying the epoxy or weld.
Belzona Weld Repair
Belzona weld repair is suggested by some as a more durable alternative to JB Weld.
Metal Stitching
Metal stitching is mentioned as a repair method for large and expensive engine blocks, but it's not clear if this is a viable option for smaller boat engines.
Before attempting any repairs, it's important to determine the extent of the damage and whether the crack is internal or external. If the crack is internal, a new block may be necessary. Performing a compression test can help determine the severity of the damage. Additionally, checking the oil for a milky appearance can indicate if there is water in the oil, which could be a sign of a cracked block.
Locating Your Boat's HIN: A Step-by-Step Guide
You may want to see also
Engine block cracks and poor boat storage
Poor storage of your boat can lead to a cracked engine block. If you don't drain the water and fill the system with antifreeze before storing your boat for the winter, the water can freeze and expand, causing cracks in the engine block.
To prevent this from happening, it is important to properly winterize your boat. This includes draining the water and adding antifreeze to the engine, as well as taking other measures such as covering the boat and using heat sources to keep the engine from freezing.
If you suspect that your boat's engine block may be cracked, there are several signs you can look out for. One indication is visible smoke in the cabin, which can be caused by the mixing of oil or coolant and antifreeze when the engine block cracks. Overheating of the engine is another symptom, as reduced antifreeze levels can cause temperatures to rise. Leaking oil is also a sign of a potential crack, as the slit in the defective engine can allow oil or coolant to seep out.
If you notice any of these issues, it is important to address them promptly. While some cracks can be repaired, others may require a replacement engine. It is recommended to consult a professional to assess the damage and determine the best course of action.
In addition to poor storage, other causes of engine block cracks include excess heat due to coolant system failure, water pump failure, and manufacturer defects. To prevent cracks, it is important to maintain your boat's engine and address any issues with the coolant system or water pump promptly.
Zoning Requirements for Boat and RV Storage and Parking
You may want to see also
Frequently asked questions
If your boat's engine block is cracked, you may notice some of the following symptoms:
- Coolant in the oil, giving it a creamy white appearance.
- Oil in the coolant, resulting in a loss of oil.
- Coolant or oil leaks into the bilge area.
- Visible smoke in the cabin.
- Overheating of the engine.
- Discoloured oil.
- Poor engine performance.
Engine blocks can crack due to a variety of issues, but excess heat is the most common cause. High temperatures in the engine are usually caused by a problem with the coolant, which regulates engine temperature. When the coolant system fails, sections of the engine that don't receive coolant overheat, causing the metal to expand and creating thermal stress that can lead to cracks.
Yes, if the cracks are not too severe, it is possible to repair a cracked boat engine block. Repairs may involve sealing the damage to prevent coolant or oil leaks, and techniques such as pinning, gluing, and welding can be used. However, not all cracks are repairable, and you may need to replace the engine block or get a new engine.
To prevent your boat's engine block from cracking, proper maintenance is key. This includes draining the water and filling the system with antifreeze during fall storage. Additionally, ensure your boat's water pump is functioning optimally to maintain proper coolant flow and prevent overheating.