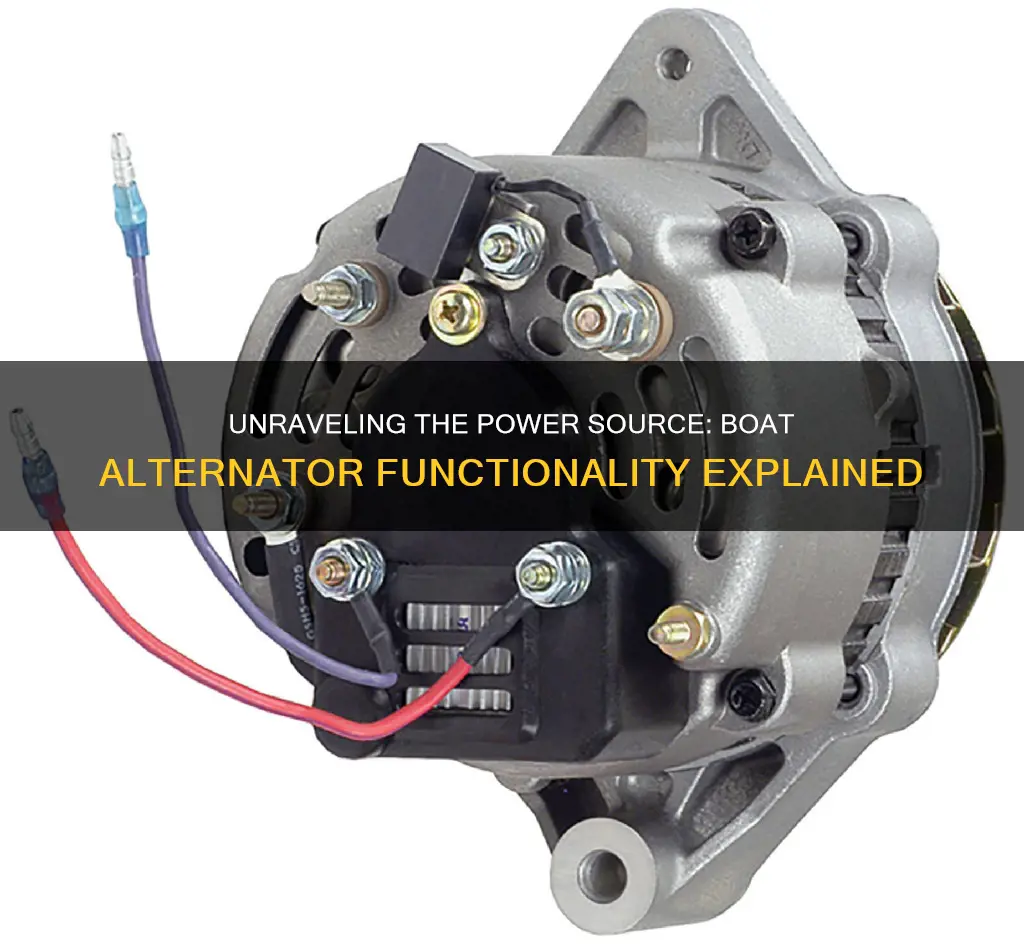
A boat alternator is a crucial component of a vessel's electrical system, responsible for generating electrical power from the engine's mechanical energy. It operates on the principle of electromagnetic induction, where the rotation of the engine's internal components, typically a rotor, creates a magnetic field that induces an electric current in the stator windings. This process converts the mechanical energy into electrical energy, which is then used to power various electrical systems on the boat, such as lights, navigation equipment, and appliances. Understanding the inner workings of a boat alternator is essential for proper maintenance and troubleshooting, ensuring the vessel's electrical system functions reliably during extended periods at sea.
What You'll Learn
- Alternator Basics: Converts mechanical energy into electrical power for boat systems
- AC vs DC: Alternators produce alternating current (AC), which is then converted to direct current (DC)
- Rotor and Stator: The rotor spins inside the stator, generating electrical current through electromagnetic induction
- Regulation: Voltage regulation ensures a stable output, compensating for load variations
- Cooling System: Efficient cooling prevents overheating, maintaining optimal performance
Alternator Basics: Converts mechanical energy into electrical power for boat systems
An alternator is a crucial component in a boat's electrical system, responsible for generating electrical power from mechanical energy. It is a vital device that ensures the boat's various systems, such as lighting, engines, and appliances, have a consistent and reliable power supply. Understanding the basics of how an alternator works is essential for boat owners and operators to maintain and troubleshoot their vessel's electrical systems effectively.
The alternator operates on the principle of electromagnetic induction. It consists of several key components: an alternator pulley, a rotor (or armature), and a stator. The alternator pulley is connected to the boat's engine via a belt or direct drive, allowing the alternator to rotate when the engine is running. As the pulley turns, it drives the rotor, which is typically a series of coils of wire. The rotor is positioned inside the stator, a stationary component with slots that accommodate the rotor's coils.
When the rotor rotates, it generates a magnetic field that interacts with the stator's slots. This interaction induces an electric current in the rotor's coils through the process of electromagnetic induction. The stator's design ensures that the magnetic field cuts through the rotor coils at a precise angle, maximizing the induction of electrical current. This current is then directed through the alternator's internal wiring and diodes, which ensure the proper flow of direct current (DC) to the boat's electrical system.
The alternator's output is typically in the form of alternating current (AC) due to the rotating nature of the rotor and stator. However, most boat systems require direct current (DC) for operation. This is where the rectifier comes into play. The rectifier is an essential component that converts the AC output from the alternator into DC, ensuring the boat's electrical components function correctly.
In summary, an alternator is a mechanical-to-electrical energy converter, playing a critical role in powering a boat's electrical systems. It harnesses the mechanical energy from the boat's engine and transforms it into electrical power through electromagnetic induction. The alternator's design, including its pulley, rotor, and stator, ensures efficient energy conversion, while the rectifier ensures the output is in the form of DC, suitable for most boat applications. Understanding these basics is key to maintaining a boat's electrical integrity and ensuring a safe and functional vessel.
Finding the Empty Boat: A Thousand Gates' Secrets
You may want to see also
AC vs DC: Alternators produce alternating current (AC), which is then converted to direct current (DC)
Alternators in boats, like in any vehicle, play a crucial role in generating power for the electrical systems. When it comes to understanding the inner workings of a boat alternator, it's essential to grasp the difference between alternating current (AC) and direct current (DC) and how they interact.
Alternators produce AC electricity, which is a type of electrical current that periodically reverses its direction. This is in contrast to DC, which flows in one direction only. The AC output from the alternator is a result of the mechanical rotation of the alternator's armature, which is driven by the engine. As the armature rotates, it generates a changing magnetic field, inducing an AC voltage in the alternator's stator windings.
The challenge arises when considering the use of AC in a boat's electrical system, as most boat electronics and appliances are designed to operate on DC. This is where the concept of conversion comes into play. The AC electricity generated by the alternator is not directly usable for most boat applications. Therefore, it undergoes a process called rectification, where diodes are used to convert the AC waveform into a pulsating DC current. This process essentially 'locks' the current in one direction, making it suitable for charging batteries and powering DC-dependent devices.
The rectification process is a critical component of a boat's electrical system. It ensures that the energy generated by the alternator is in a form that can be effectively utilized by the various components, such as lights, navigation equipment, and entertainment systems. The alternator's output is then regulated to provide a stable DC voltage, typically around 12 volts, which is commonly used in marine applications.
In summary, boat alternators produce AC electricity, which is then converted to DC through rectification. This process ensures that the electrical energy generated by the alternator can power the boat's electrical systems efficiently. Understanding this conversion process is key to maintaining a reliable and functional electrical setup on any vessel.
Murdaugh Boat Accident: Unraveling the Mystery
You may want to see also
Rotor and Stator: The rotor spins inside the stator, generating electrical current through electromagnetic induction
The alternator in a boat is a crucial component for charging the battery and powering various electrical systems while the vessel is in operation. At the heart of this process are two key components: the rotor and the stator.
The rotor is a rotating part of the alternator, typically an armature or a magnet. It is designed to spin rapidly within the stator, which is a stationary component. This spinning motion is achieved through the engine's power, often via a belt or direct drive. As the rotor rotates, it creates a magnetic field that interacts with the stator's coils.
The stator is a cylindrical or cylindrical-shaped assembly of coils of wire. These coils are wound around a core, often made of iron or steel, to create a magnetic flux. When the rotor's magnetic field interacts with the stator's coils, it induces an electrical current through the process of electromagnetic induction. This current is then directed through the alternator's internal wiring to the battery and other electrical systems.
The speed of the rotor's rotation is critical to the alternator's performance. The faster the rotor spins, the more electrical current is generated. This is why alternators are often driven by the engine's crankshaft, as the engine's speed directly influences the rotor's rotation. The design of the rotor and stator, along with the number of magnetic poles and wire turns, determines the voltage and current output of the alternator.
In summary, the rotor and stator work in harmony to convert mechanical energy from the engine into electrical energy. The spinning rotor, driven by the engine, creates a magnetic field that interacts with the stator's coils, inducing an electrical current. This process is fundamental to the alternator's role in keeping a boat's electrical systems powered and the battery charged.
Aluminum vs. Fiberglass Boats: Which Material Floats Lighter?
You may want to see also
Regulation: Voltage regulation ensures a stable output, compensating for load variations
Voltage regulation is a critical component of a boat alternator's functionality, ensuring that the electrical system on the vessel remains stable and reliable, even under varying load conditions. This regulation mechanism is designed to maintain a consistent voltage output, which is essential for the proper operation of sensitive electronic equipment and the overall safety of the boat.
The alternator's voltage regulation system works by continuously monitoring the voltage output and making adjustments to keep it within a specified range. When the alternator is connected to the battery, it begins to generate an alternating current (AC) voltage. This voltage is then regulated to ensure it remains at an optimal level, typically around 12 volts for a standard automotive alternator. The regulation process involves a feedback loop, where a voltage regulator component compares the actual voltage output with a reference voltage and makes adjustments to the alternator's field or armature circuit accordingly.
In the event of increased electrical load, such as running multiple high-power devices simultaneously, the alternator's voltage regulation system springs into action. It detects the drop in voltage caused by the additional load and responds by increasing the alternator's output. This ensures that the voltage remains stable, preventing potential damage to sensitive electronics and maintaining the boat's electrical system's integrity. Conversely, if the load decreases, the regulator reduces the alternator's output to maintain the desired voltage level.
This dynamic voltage regulation is crucial for the longevity and reliability of the boat's electrical system. Without it, sudden changes in load could lead to voltage fluctuations, causing damage to sensitive components like computers, navigation systems, and electronic controls. By compensating for load variations, the alternator's voltage regulation system ensures that the boat's electrical needs are consistently met, providing a safe and efficient operation.
In summary, voltage regulation in a boat alternator is a sophisticated process that ensures the electrical system's stability and longevity. It enables the alternator to adapt to changing load conditions, delivering a consistent voltage output that powers the boat's electronics and accessories reliably. Understanding this regulation mechanism is essential for maintaining and troubleshooting the electrical system of any vessel.
The Lickity Split Boat's Mysterious Fate
You may want to see also
Cooling System: Efficient cooling prevents overheating, maintaining optimal performance
The cooling system is a critical component of a boat alternator's design, ensuring its longevity and efficient operation. Overheating can lead to performance degradation, damage to the alternator, and even failure. Therefore, understanding the cooling mechanism is essential for maintaining the alternator's health.
Boat alternators often utilize a combination of cooling methods to prevent overheating. One common approach is the use of a liquid cooling system, typically involving a coolant or antifreeze mixture. This liquid is circulated through the alternator's core, absorbing heat generated during operation. The heated coolant then travels to a radiator, where it dissipates the excess heat into the surrounding air. This process is similar to how car engines cool down, but adapted for marine environments.
In addition to liquid cooling, some boat alternators employ air cooling. This method relies on the natural convection of air to transfer heat away from the alternator. The alternator's housing is designed with fins or louvered panels that increase the surface area, allowing for more efficient heat dissipation. Air cooling is often used in conjunction with liquid cooling to enhance overall cooling performance, especially in high-power applications.
Efficient cooling is crucial for maintaining the alternator's performance and extending its lifespan. Overheating can cause internal components to expand and warp, leading to electrical shorts or mechanical failures. It can also result in reduced voltage output and decreased charging efficiency. By keeping the alternator's temperature within optimal limits, the cooling system ensures consistent performance, allowing the alternator to deliver the required power to the boat's electrical systems.
Regular maintenance of the cooling system is essential. This includes checking the coolant level and condition, ensuring the radiator is clean and free of debris, and inspecting the alternator's housing for any signs of damage or corrosion. Proper maintenance ensures that the cooling system functions effectively, providing reliable and efficient operation of the boat alternator.
Lime Saddle Boat Launch: Open or Closed?
You may want to see also
Frequently asked questions
A boat alternator is an electrical generator that converts mechanical energy into electrical power. It is a crucial component in a boat's electrical system, providing the necessary power to run various electrical devices and recharge the battery.
The alternator operates through a process called electromagnetic induction. It consists of a rotating armature (rotor) and a stationary stator. When the engine is running, the rotor spins within the stator, creating a magnetic field. This magnetic field induces an electric current in the stator windings, thus generating electrical power.
The belt or pulley system connects the alternator to the boat's engine. As the engine rotates, it drives the alternator's rotor, which in turn generates electricity. This system ensures that the alternator receives the necessary mechanical power to function efficiently.
While both devices convert mechanical energy to electrical energy, they operate slightly differently. A generator typically produces direct current (DC), whereas an alternator generates alternating current (AC). In a boat's context, the alternator is more common as it provides the AC power required for most electrical devices, and it also charges the DC battery.