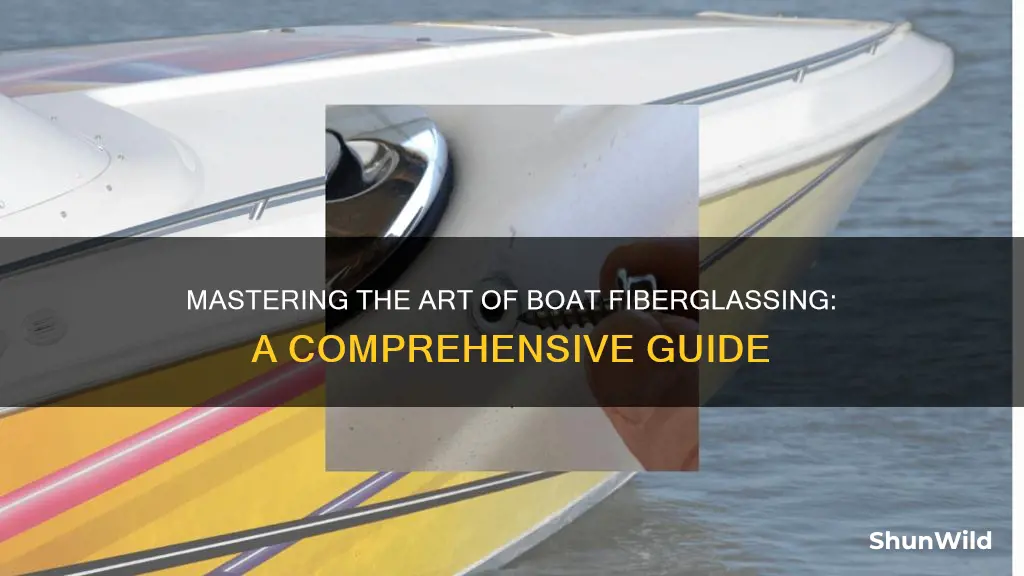
Fiberglassing a boat is a crucial process in boat building and repair, allowing for the reinforcement and protection of the vessel's structure. It involves applying a layer of fiberglass, a composite material made of fine glass fibers and a resin, over a wet or dry surface to create a strong, lightweight, and durable shell. This technique is commonly used to repair damage, reinforce weak areas, or create custom shapes and designs. The process typically starts with preparing the surface by cleaning and smoothing it, then applying a layer of fiberglass cloth or mat, followed by a layer of resin, and finally, a curing process to harden the material. This method is favored in boat construction due to its ability to provide a smooth, seamless finish and its resistance to corrosion and impact damage.
What You'll Learn
- Preparation: Clean and prepare the boat's surface for fiberglass application
- Mixing Resins: Combine epoxy resin and hardener in precise ratios for optimal bonding
- Laying Glass: Apply fiberglass cloth in layers, ensuring even coverage and smooth surface
- Sanding & Fairing: Smooth the fiberglass surface with sandpaper and fairing techniques for a seamless finish
- Finishing Touches: Apply final coatings and sealants to protect the boat's fiberglass structure
Preparation: Clean and prepare the boat's surface for fiberglass application
Before you begin the process of applying fiberglass to your boat, proper preparation is crucial to ensure a successful and long-lasting repair or customization. The key to a durable and smooth finish lies in meticulous surface preparation. Here's a step-by-step guide to cleaning and preparing the boat's surface for fiberglass application:
Step 1: Remove Old Material (if applicable): If your boat already has existing fiberglass or any other material that needs to be replaced, start by carefully removing it. This process might involve chipping away old resin or fiber, ensuring you don't damage the underlying structure. Use tools like chisels and wire brushes to gently lift and remove the old material, creating a clean and smooth base for the new fiberglass.
Step 2: Sanding: Sanding is an essential step to create a rough surface that will provide better adhesion for the fiberglass. Use a variety of sandpaper grades, starting with a coarse grit (e.g., 40-60) to remove any remaining old material and smooth out the surface. Progress to finer grits (e.g., 80-120) for a more refined finish. Pay close attention to all areas, including curves and contours, ensuring an even and consistent surface. After sanding, wipe away any dust or debris with a damp cloth to prepare the surface for the next step.
Step 3: Cleaning: Proper cleaning is vital to remove any contaminants that could interfere with the bonding process. Use a mild detergent or a specialized boat cleaner, applied with a soft brush or sponge. Scrub the entire surface, ensuring you cover all areas, including the areas where the old material was removed. Rinse thoroughly with water to remove any cleaning solution, and allow the surface to dry completely in a well-ventilated area.
Step 4: Filling and Repair: Inspect the boat's surface for any remaining imperfections, such as small holes or cracks. Fill these areas with a suitable marine filler or putty, ensuring it is compatible with the existing material. Follow the manufacturer's instructions for application and curing time. This step is crucial to creating a seamless surface for the fiberglass. Once the filler is cured, sand it again to create a smooth and even base for the fiberglass application.
Step 5: Etching (Optional): For optimal adhesion, some experts recommend etching the surface. This process involves using a weak acid solution to create a microscopic roughness on the surface. Follow a reputable guide or consult a professional for the correct etching process, as it requires precision and care.
By following these preparation steps, you'll ensure that the boat's surface is clean, smooth, and ready for the fiberglass application, resulting in a strong and long-lasting bond.
Boat Ramps in Tampa: Open for Business?
You may want to see also
Mixing Resins: Combine epoxy resin and hardener in precise ratios for optimal bonding
When it comes to fiberglassing a boat, one of the most critical steps is mixing the epoxy resin and hardener in the correct proportions. This process ensures the structural integrity and longevity of the boat's construction. Here's a detailed guide on how to achieve optimal bonding through precise resin and hardener mixing:
Understanding the Ratio: The key to successful bonding lies in the ratio of epoxy resin to hardener. Epoxy resins are typically two-part systems, consisting of a resin and a hardener. The resin is the liquid component, while the hardener is a catalyst that initiates the curing process when mixed. The ideal ratio is crucial as it determines the strength, flexibility, and overall performance of the epoxy bond. An improper ratio can lead to weak joints, reduced impact resistance, or even structural failure.
Measuring Accurately: To achieve the correct ratio, precise measurements are essential. Use accurate measuring tools, such as graduated cylinders or measuring cups, to measure the epoxy resin and hardener separately. It is recommended to follow the manufacturer's guidelines for the specific epoxy system you are using. Typically, the resin and hardener are mixed in a 1:1 ratio by weight or volume, depending on the product. For example, if the instructions specify a 100-gram mixture, measure 50 grams of resin and 50 grams of hardener.
Mixing Technique: When combining the resin and hardener, ensure a thorough and consistent blend. Start by slowly adding the hardener to the resin, stirring continuously. This step is crucial to prevent the formation of air bubbles, which can weaken the bond. Mix the components until they are fully incorporated and there are no visible signs of separation. The mixing process should be done quickly but carefully to maintain the chemical reaction's activation period, which is typically a short time frame.
Consistency and Timing: The mixed epoxy should have a smooth, viscous consistency, resembling honey or thick paint. If the mixture becomes too thick, it may indicate an excess of hardener. Conversely, if it becomes too runny, it could suggest an excess of resin. Adjust the ratio accordingly and mix again. Timing is critical; once the epoxy is mixed, it has a limited time before it starts to cure, so work efficiently to ensure a successful bond.
Application and Curing: After achieving the perfect mix, apply the epoxy to the boat's surface, following the specific techniques recommended for your chosen epoxy system. Ensure proper surface preparation and adhesion to maximize bonding strength. Allow sufficient time for the epoxy to cure according to the manufacturer's instructions, which may vary depending on the temperature and humidity. Proper curing is essential to develop the full strength of the fiberglass bond.
Finding Your Boat's Weight Limit: A Guide
You may want to see also
Laying Glass: Apply fiberglass cloth in layers, ensuring even coverage and smooth surface
When laying glass on a boat, the process of applying fiberglass cloth in layers is a crucial step to ensure a strong and durable structure. This technique involves carefully placing and smoothing out multiple layers of fiberglass cloth to create a seamless and sturdy surface. Here's a step-by-step guide to mastering this process:
Preparation: Before you begin, ensure that the boat's surface is clean, dry, and free from any debris. Prepare the fiberglass cloth by cutting it to the appropriate size, considering the area you need to cover. It's essential to have a steady hand and a sharp knife or scissors for precise cuts. Gather the necessary tools, including a roller or brush for applying resin, a heat gun or hairdryer for curing, and a smooth surface to work on.
Applying the First Layer: Start by laying the fiberglass cloth over the prepared area, ensuring it covers the entire surface evenly. Use your hands or a roller to gently press the cloth onto the boat, removing any air bubbles. Smooth out any wrinkles or creases by carefully running your fingers or a soft brush over the cloth. Take your time to create a flat and even surface, as this will impact the overall finish. Allow the first layer to cure slightly, following the resin manufacturer's instructions for curing times.
Adding Subsequent Layers: For subsequent layers, repeat the process, carefully placing the fiberglass cloth over the previous layer. Ensure that the edges align properly, and use a roller or brush to press the cloth firmly. Pay close attention to corners and edges, as these areas require extra care to avoid gaps or uneven surfaces. After each layer, inspect the work and use a sharp tool to remove any excess resin or cloth fibers that may have lifted.
Achieving Smoothness: The key to a successful layup is maintaining a smooth surface. Take the time to carefully smooth out each layer, ensuring there are no visible wrinkles or creases. Use a soft brush or your fingers to gently glide over the surface, removing any air bubbles or imperfections. For intricate areas or curves, consider using a small brush or a heat gun to carefully melt and reshape the resin, creating a seamless finish.
Curing and Inspection: Allow sufficient time for each layer to cure according to the resin's instructions. Once cured, inspect the work for any imperfections or areas that require additional attention. Use a sharp tool to carefully remove any lifted fibers or uneven spots, and reapply a thin layer of resin to these areas if needed. Proper curing and inspection ensure that the fiberglass layers bond correctly and create a strong, durable boat structure.
Transferring a Boat Title: Texas to Louisiana
You may want to see also
Sanding & Fairing: Smooth the fiberglass surface with sandpaper and fairing techniques for a seamless finish
Sanding and fairing are crucial steps in achieving a smooth and seamless finish when working with fiberglass on a boat. These processes ensure that the surface is not only visually appealing but also structurally sound, allowing for a durable and long-lasting vessel. Here's a detailed guide on how to master the art of sanding and fairing for a professional-grade boat finish.
Sanding the Fiberglass Surface:
Start by ensuring the fiberglass is clean and free from any debris or old filler. Use a fine-grit sandpaper (e.g., 400-grit) to gently sand the entire area, following the direction of the fiber weave. This initial sanding helps to remove any imperfections and prepares the surface for further work. Pay close attention to corners and edges, as these areas often require more careful treatment. After sanding, wipe away the dust and any remaining debris with a damp cloth to create a smooth base for the next step.
Fairing for a Seamless Finish:
Fairing is the process of smoothing out the surface using various tools and techniques. Here's a breakdown:
- Fairing Compound: Apply a fairing compound specifically designed for fiberglass. This compound fills in minor imperfections and creates a smooth surface. Work in small sections, applying the compound with a putty knife or a specialized fairing tool. Allow it to dry slightly, then sand it gently with a finer grit (e.g., 600-grit) to ensure a smooth transition between panels.
- Sanding Techniques: Use a variety of sanding tools like a power sander, orbital sander, or even a hand sander for tight spaces. Start with a higher grit (e.g., 320-grit) and gradually move to finer grits (600-grit, 1200-grit) for an ultra-smooth finish. Always sand with the direction of the fiber weave to maintain structural integrity.
- Fairing Tools: Invest in fairing tools like a fairing block or a 'fairing gun' to apply compounds and resins efficiently. These tools help create a seamless blend between panels, ensuring a professional-looking finish.
Mastering the art of sanding and fairing requires practice and attention to detail. Take your time, work in small sections, and always sand with the grain. This process ensures that your boat's fiberglass surface is not only smooth but also ready for the final coat of paint or gelcoat, resulting in a stunning and durable vessel. Remember, patience and precision are key to achieving a seamless fiberglass finish.
Bass Boat Essentials: Must-Have Products for a Great Catch
You may want to see also
Finishing Touches: Apply final coatings and sealants to protect the boat's fiberglass structure
The final steps in the fiberglass boat-building process involve applying protective coatings and sealants to ensure the boat's longevity and durability. These finishing touches are crucial to safeguarding the fiberglass structure from environmental damage and wear and tear. Here's a comprehensive guide to achieving a professional-grade finish:
Step 1: Choosing the Right Coatings
Start by selecting the appropriate coatings for your boat's specific needs. Marine-grade epoxy resins are commonly used for their excellent bonding properties and resistance to UV radiation and chemicals. These resins can be applied as a thin layer or a thicker coat, depending on the desired finish and protection level. For added protection, consider using a clear, high-build epoxy system, which provides a robust barrier against water absorption and chemical penetration.
Step 2: Surface Preparation
Before applying any coatings, ensure the fiberglass surface is clean, smooth, and free of debris. Use a mild detergent to wash the boat, then rinse thoroughly and allow it to dry completely. Inspect the surface for any imperfections, such as small holes or scratches, and fill them with a suitable fiberglass filler. Sand the entire surface gently with fine-grit sandpaper to create a smooth, even finish. This preparation step is critical to ensure proper adhesion and a seamless final coat.
Step 3: Application Techniques
There are several methods to apply the final coatings, each offering unique advantages:
- Spraying: This method provides an even, smooth finish and is ideal for larger areas. Use a high-pressure spray gun to apply the epoxy resin, ensuring full coverage. Spray in a consistent, controlled manner, maintaining a steady distance from the surface.
- Brushing or Rolling: For smaller areas or intricate details, brushing or rolling the epoxy is preferable. This technique allows for more precise control and is suitable for creating thin, decorative coats. Use a high-quality brush or roller to ensure an even application.
- Hand Application: For the final coat, consider hand-applying the epoxy using a small brush or pad. This method is excellent for achieving a smooth, glossy finish and is perfect for detailing and edge work.
Step 4: Curing and Protection
After applying the coatings, allow sufficient time for curing, following the manufacturer's instructions. Curing times can vary depending on the epoxy system used. Once cured, the boat's fiberglass structure will be protected by a durable, water-resistant layer. To enhance this protection, consider adding a marine-grade sealant to the joints and seams, ensuring a comprehensive seal against water intrusion.
Step 5: Final Touches and Maintenance
Once the boat is fully cured, inspect the entire surface for any imperfections or areas requiring touch-ups. Use fine-grit sandpaper to smooth out any rough spots and then wipe down the surface with a clean cloth. Finally, apply a marine-grade wax or polish to enhance the boat's appearance and provide additional protection. Regular maintenance, including cleaning and re-coating, will ensure the boat's fiberglass structure remains in excellent condition for years to come.
Catamaran Boats: Inshore Exploration, Good or Bad?
You may want to see also
Frequently asked questions
Fiberglassing a boat involves several steps to reinforce and protect the hull and structure. It starts with preparing the boat's surface by cleaning and smoothing it. Then, a layer of fiberglass cloth is applied over the gelcoat or epoxy resin, ensuring a smooth and even surface. This process is repeated with multiple layers, allowing each layer to cure before adding the next. The final step includes sanding and finishing to create a smooth, durable exterior.
Selecting the appropriate fiberglass depends on various factors. Consider the boat's intended use, desired strength, and aesthetic appeal. For structural reinforcement, consider using woven fiberglass cloth, which provides excellent strength and durability. For a lighter and more flexible option, mat or chopped strand fiberglass can be used for non-structural areas. Always refer to the manufacturer's guidelines or consult an expert to ensure you choose the right type for your specific boat project.
Having the right tools is crucial for a successful fiberglassing job. Essential equipment includes various types of fiberglass cloth, resin, hardener, and a gelcoat or paint for the final finish. You will also need a respirator for safety, gloves, and protective clothing to avoid skin contact with chemicals. Additionally, tools like a roller, spray gun, and utility knife are essential for application and shaping the fiberglass. It's recommended to have a well-equipped workshop or consult professionals for guidance on the necessary tools for your boat's fiberglassing project.