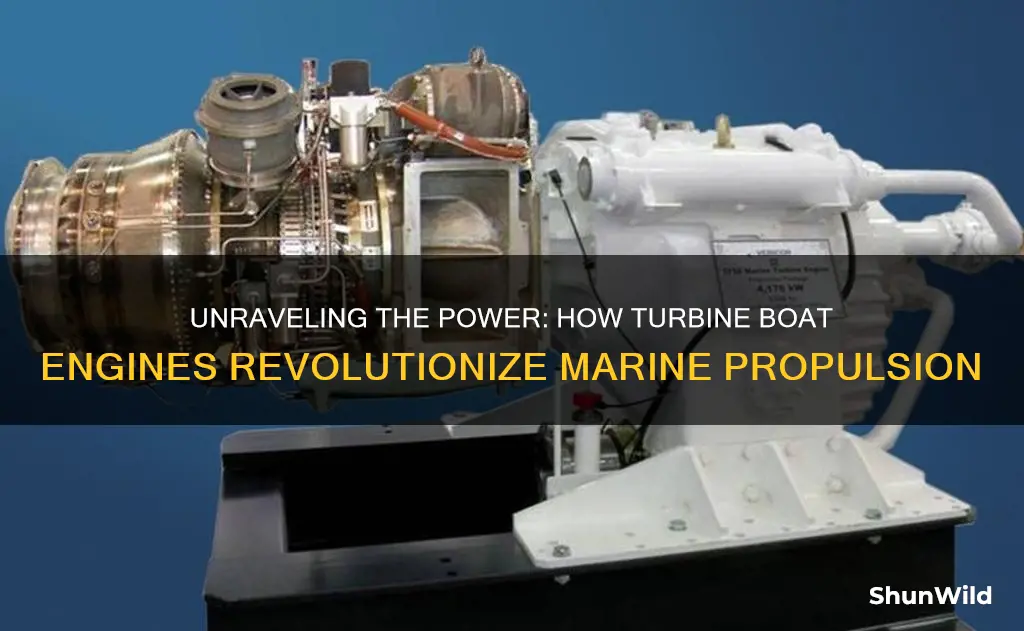
Turbine boat engines are a marvel of engineering, utilizing the principles of gas or steam turbines to propel vessels through water. These engines convert the energy from fuel into rotational motion, which is then transferred to the propeller, generating thrust. The process involves compressing air, mixing it with fuel, igniting the mixture, and directing the resulting hot gases through a turbine, spinning it rapidly. This spinning turbine drives a generator, which produces electricity to power various components of the boat. The design allows for efficient power generation and transmission, making turbine engines a popular choice for high-performance boats and military vessels. Understanding the mechanics of these engines is crucial for anyone interested in marine propulsion technology.
What You'll Learn
- Engine Components: Turbine boat engines consist of blades, rotors, and a compressor for power generation
- Fuel Combustion: Gasoline or diesel is injected and burned to create high-pressure gases
- Blade Rotation: Gases accelerate and spin blades, converting thermal energy into mechanical energy
- Propulsion System: The spinning blades drive a propeller, propelling the boat forward
- Efficiency and Maintenance: Regular maintenance ensures optimal performance and longevity of turbine engines
Engine Components: Turbine boat engines consist of blades, rotors, and a compressor for power generation
The core of a turbine boat engine's power generation lies in its intricate design, which includes several key components. Firstly, there are the blades, which are typically made of lightweight, durable materials such as titanium or advanced composites. These blades are carefully shaped and angled to capture and redirect the flow of water or gas. When the boat's propeller spins, it creates a vortex, and these blades are positioned to take advantage of this vortex, extracting energy from it. The blades are connected to a central shaft, often called the rotor, which rotates as a result of the blade's movement.
The rotor is a critical component, as it is directly responsible for converting the energy from the blades into rotational motion. This motion is then transferred to a compressor, which is the heart of the engine's power generation process. The compressor compresses the incoming fluid (often water or air) to increase its pressure and temperature, creating a high-energy state. This compression process is essential as it provides the necessary energy to drive the turbine and generate power.
Within the compressor, there are multiple stages of compression, each designed to increase the pressure further. These stages are carefully engineered to ensure efficient compression without causing excessive heat or pressure, which could lead to engine damage. The compressed fluid is then directed towards the turbine, where the energy is extracted to spin the rotor. This process is the fundamental principle of turbine engines, where the energy of the fluid is harnessed to create rotational motion.
The turbine's blades are positioned to capture the high-energy fluid, and as it flows over them, it causes the rotor to spin rapidly. This spinning motion is then transferred to the boat's propeller, driving the vessel forward. The efficiency of this process relies on the precise engineering of each component, ensuring that energy is effectively captured and transferred from one part to another.
In summary, turbine boat engines harness the power of fluid dynamics, utilizing blades, rotors, and compressors to generate electricity. The blades capture energy from the boat's movement, the rotor converts this energy into rotational motion, and the compressor increases fluid pressure, all working in harmony to provide the necessary power for the vessel's propulsion and other electrical needs. This intricate system showcases the brilliance of engineering, allowing boats to navigate efficiently while utilizing the principles of turbine technology.
Kenny Chesney's Boat: A Pirate's Life?
You may want to see also
Fuel Combustion: Gasoline or diesel is injected and burned to create high-pressure gases
The process of fuel combustion in turbine boat engines is a critical aspect of their operation, converting chemical energy into mechanical power. When gasoline or diesel is used as fuel, the combustion process involves precise injection and rapid burning to generate high-pressure gases. This high-pressure gas production is a fundamental principle of turbine engines, where the expansion of these gases through a turbine blade array creates the rotational force that drives the boat.
Fuel injection is a precise process, where the fuel is carefully measured and atomized to ensure efficient combustion. The fuel is injected into the engine's combustion chamber, where it mixes with air and is ignited. This mixture is highly controlled to optimize the combustion process, ensuring that the fuel burns completely and rapidly. The timing and amount of fuel injection are critical, as they directly impact the engine's performance and efficiency.
The combustion process begins with the injection of fuel into the combustion chamber, which is typically a small, enclosed space. The fuel is injected at high pressure to ensure it mixes thoroughly with the air. This mixture is then ignited, often by a spark plug in the case of gasoline engines or by the heat of compression in diesel engines. The rapid burning of this mixture creates a significant temperature and pressure rise, resulting in the formation of high-pressure gases.
These high-pressure gases expand rapidly, driving the turbine blades. The turbine is connected to the engine's output shaft, and as the gases expand, they spin the turbine, which in turn rotates the shaft. This rotational force is then transferred to the boat's propeller, propelling the vessel forward. The efficiency of this process is crucial, as it directly impacts the engine's power output and the boat's performance.
In summary, the combustion of gasoline or diesel fuel in turbine boat engines is a complex and precise process. It involves careful fuel injection, rapid burning, and the creation of high-pressure gases, which then drive the turbine and propel the boat. This intricate process showcases the engineering marvels that enable modern boats to navigate efficiently through the water.
Boat Driving: Easy Ocean Cruising or Tricky Task?
You may want to see also
Blade Rotation: Gases accelerate and spin blades, converting thermal energy into mechanical energy
In the heart of a turbine boat engine, the process of converting thermal energy into mechanical energy begins with the rotation of blades. This fundamental principle is at the core of how these engines operate, providing the power necessary to propel boats through the water.
When a turbine boat engine is in operation, hot gases are produced by the combustion of fuel. These gases are directed towards the turbine section of the engine. As the gases enter the turbine, they encounter a series of blades arranged in a specific configuration. The design of these blades is crucial, often featuring a curved or cambered shape that allows for efficient energy transfer.
The interaction between the hot gases and the turbine blades is a dynamic one. As the gases accelerate towards the blades, they create a force that causes the blades to rotate. This rotation is a result of the gases' momentum and the carefully designed angle of attack on the blades. The angle of attack refers to the angle at which the gases impact the blades, and it is optimized to maximize the lift force, which in turn drives the blade rotation.
The spinning blades are connected to a shaft, often through a series of gears or a direct coupling. This shaft is a critical component, as it transfers the rotational energy from the blades to other parts of the engine. The mechanical energy generated by the blade rotation is then utilized to drive the boat's propeller, propelling the vessel forward.
This process of blade rotation and energy conversion is a highly efficient method of power generation. Turbine boat engines are renowned for their ability to produce significant power output from relatively small fuel consumption. The design and precision engineering of these engines ensure that the thermal energy from fuel is effectively transformed into the mechanical energy required to move the boat, making them a popular choice for various watercraft applications.
Exploring Oceans with a 20-Foot Sailboat
You may want to see also
Propulsion System: The spinning blades drive a propeller, propelling the boat forward
The propulsion system in turbine boat engines is a fascinating and efficient method of generating forward momentum. When the turbine engine is in operation, the spinning blades, often referred to as rotors, play a pivotal role in this process. These blades are designed with precision, featuring a unique shape and angle that allows them to capture and harness the power of the turbine's rotation. As the engine rotates, the blades accelerate, creating a powerful force that drives the propeller.
The propeller is a critical component in this system. It is typically connected to the turbine via a shaft, which ensures the transfer of power from the spinning blades to the propeller. The propeller's design is such that it has a series of blades or vanes that are angled and shaped to optimize water flow. When the propeller is driven by the turbine, it rotates, creating a forward thrust. This thrust is a result of the water being pushed backward, which, according to Newton's third law of motion, propels the boat forward.
The efficiency of this system lies in the precise engineering of the blades and the propeller. The angle and shape of the blades are carefully calculated to maximize the power transfer and minimize energy loss. As the turbine blades spin, they create a vortex of air or water, depending on the type of engine, which is then directed through the propeller. This process is highly efficient, allowing for a significant amount of power to be transferred to the propeller, resulting in a powerful and controlled forward motion.
In turbine boat engines, the propulsion system is often designed to provide variable speed and torque control. This means that the engine can adjust the speed of the spinning blades and, consequently, the propeller's rotation. By doing so, the boat can accelerate, maintain speed, or even decelerate smoothly. This control is essential for navigating different water conditions and ensuring a comfortable and safe journey for passengers.
The design and functionality of the propulsion system in turbine boat engines showcase the ingenuity of marine engineering. It combines the principles of fluid dynamics, mechanics, and control systems to create a powerful and responsive method of propulsion. Whether it's a high-speed vessel or a leisurely boat, this system ensures efficient and reliable performance, making it a popular choice for various marine applications.
Launching a Boat Solo: Stay Dry with These Tips
You may want to see also
Efficiency and Maintenance: Regular maintenance ensures optimal performance and longevity of turbine engines
Regular maintenance is crucial for ensuring the efficiency and longevity of turbine boat engines. These engines, which utilize gas turbines to generate power, are known for their high performance and reliability, but they require careful attention to function optimally over extended periods. Here's an overview of why maintenance is essential and how it contributes to the overall efficiency and lifespan of these engines.
Preventive Maintenance:
Preventive maintenance is a proactive approach to engine care. It involves scheduled inspections and servicing at regular intervals, often recommended by the manufacturer. During these maintenance checks, technicians will examine various components, including the turbine blades, compressor sections, fuel injectors, and cooling systems. By identifying and addressing potential issues early on, preventive maintenance helps prevent unexpected breakdowns and costly repairs. For instance, regular cleaning and replacement of air filters ensure optimal air intake, reducing strain on the engine and improving overall efficiency.
Oil and Lubrication Systems:
Turbine engines rely on sophisticated lubrication systems to minimize friction and wear between moving parts. The oil used in these systems plays a critical role in cooling, lubricating, and sealing critical engine components. Regular oil changes and filter replacements are essential to maintain the oil's quality and prevent contamination. Over time, oil can break down and become less effective, leading to increased engine wear. Maintenance technicians will also inspect the oil cooler and ensure proper circulation to maintain optimal engine temperatures.
Performance Optimization:
Maintenance routines often include performance testing and calibration. This process involves measuring and adjusting various parameters such as fuel-air mixture, ignition timing, and exhaust gas recirculation. By optimizing these parameters, technicians can enhance engine performance, improve fuel efficiency, and reduce emissions. Regular calibration also ensures that the engine operates within the specified parameters, preventing potential damage from over-stressing the components.
Long-Term Reliability:
Proper maintenance significantly contributes to the long-term reliability of turbine boat engines. Well-maintained engines are less likely to experience sudden failures, ensuring that boat owners can rely on their vessels for various activities, from recreational cruising to commercial operations. Moreover, regular maintenance helps identify and rectify minor issues before they escalate, potentially saving the cost of major overhauls or engine replacements.
In summary, regular maintenance is the cornerstone of keeping turbine boat engines efficient, reliable, and long-lasting. It involves a combination of preventive checks, lubrication system management, performance optimization, and long-term reliability considerations. By adhering to maintenance schedules and best practices, boat owners can ensure their turbine engines perform at their best, providing power and peace of mind for years to come.
The Mystery of Steve Job's Sunken Yacht
You may want to see also
Frequently asked questions
Turbine boat engines, also known as gas turbines, are a type of internal combustion engine that powers boats and other watercraft. These engines operate on a principle similar to jet engines, where a fuel-air mixture is ignited in a combustion chamber, causing a rapid expansion of gases that spin a turbine. The turbine's rotational motion is then transferred to a propeller or shaft, which propels the boat forward. The key components include the compressor, which increases the air pressure, the combustion chamber where fuel is injected and ignited, and the turbine blades that extract energy from the hot gases, driving the propeller.
Turbine engines offer several benefits over piston engines. Firstly, they provide higher power-to-weight ratios, making them more efficient and powerful for their size. This results in faster acceleration and higher top speeds for boats. Turbine engines also have a higher power output for a given displacement, meaning they can produce more power in a smaller package. Additionally, they have a higher power-to-weight ratio, making them ideal for high-performance watercraft. The fuel efficiency of turbine engines is also notable, as they can achieve better fuel economy compared to piston engines, especially at higher speeds.
Yes, turbine boat engines require specific maintenance to ensure optimal performance and longevity. Regular maintenance includes checking and replacing engine oil and filters, as well as inspecting the turbine blades for any signs of wear or damage. Due to the high temperatures involved, cooling system maintenance is crucial to prevent overheating. Additionally, keeping an eye on fuel quality and system cleanliness is essential, as turbine engines are sensitive to fuel contamination. It is recommended to follow the manufacturer's guidelines for maintenance intervals and procedures to ensure the engine's reliability and extend its lifespan.