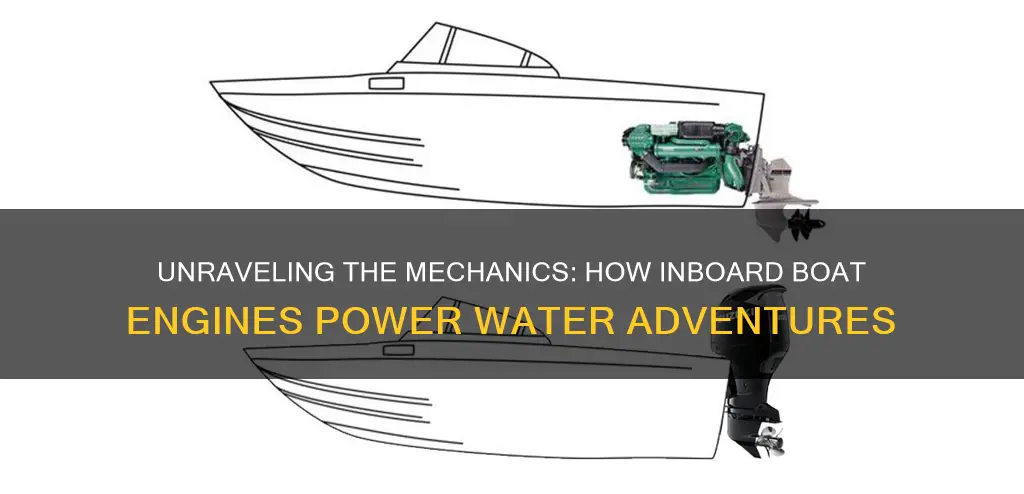
Inboard boat engines are a popular choice for recreational and commercial vessels, offering a range of benefits over outboard engines. These engines are mounted inside the hull of the boat, with the propeller extending into the water. This design provides several advantages, including improved stability, reduced noise, and enhanced fuel efficiency. Understanding how inboard boat engines work is essential for boat owners and operators, as it can help optimize performance, ensure maintenance, and prolong the engine's lifespan. This paragraph will delve into the mechanics of inboard boat engines, explaining the key components, their functions, and how they work together to propel the boat through the water.
What You'll Learn
- Engine Components: Inboard engines consist of cylinders, pistons, and a crankshaft
- Fuel System: Injection or carburetors deliver fuel to the engine
- Cooling: Engines use water or air cooling to prevent overheating
- Propeller Drive: The engine's power is transferred to the propeller via a drive shaft
- Electrical System: Batteries and alternators power the engine's accessories and starting system
Engine Components: Inboard engines consist of cylinders, pistons, and a crankshaft
Inboard boat engines are a type of marine propulsion system that is mounted inside the hull of the vessel, with the engine block positioned below the waterline. These engines are known for their compact design and efficient power-to-weight ratio, making them a popular choice for various watercraft, including boats, yachts, and personal watercraft. The operation of inboard engines relies on several key components that work in harmony to convert the engine's rotational motion into the forward thrust needed to propel the boat.
One of the fundamental components of an inboard engine is the cylinder. Cylinders are cylindrical chambers where the combustion process takes place. Inside each cylinder, a piston is fitted, which moves up and down as the engine operates. The piston's movement is directly linked to the engine's power output and efficiency. When a fuel-air mixture is ignited in the cylinder, it creates a controlled explosion, forcing the piston to move downward, which in turn rotates the crankshaft.
The piston's downward movement is a result of the combustion process, where a spark plug ignites a mixture of fuel and air, causing an explosion. This explosion exerts a force on the piston, which is then transferred to the crankshaft via the connecting rod. The crankshaft is a critical component as it converts the reciprocating motion of the pistons into rotational motion. This rotational motion is then transferred to the propeller shaft, which is connected to the propeller, ultimately providing the necessary thrust to move the boat forward.
The crankshaft plays a vital role in the engine's operation. It is a rotating shaft that is positioned at a right angle to the cylinder bank. As the pistons move, they create a reciprocating motion, but the crankshaft transforms this into a continuous rotational motion. This rotational motion is essential for the engine's overall performance and efficiency. The crankshaft is connected to the propeller shaft through a series of gears or a belt drive, ensuring that the engine's power is effectively transferred to the propeller.
In addition to these primary components, inboard engines also feature various other parts such as the fuel injection system, which delivers the precise amount of fuel required for efficient combustion, and the cooling system, which maintains optimal engine temperature. The engine's design and functionality are carefully engineered to ensure smooth operation, reliability, and longevity, making inboard engines a preferred choice for marine applications.
Finding Bad Grounds on Boats: A Comprehensive Guide
You may want to see also
Fuel System: Injection or carburetors deliver fuel to the engine
The fuel system is a critical component of an inboard boat engine, responsible for delivering the necessary fuel to the engine's cylinders for combustion. This system ensures efficient and precise fuel supply, allowing the engine to run smoothly and deliver optimal performance. The primary function of the fuel system is to mix the correct ratio of air and fuel, which is crucial for combustion and engine efficiency.
Inboard boat engines typically use either a fuel injection system or a carburetor for fuel delivery. Both methods have their advantages and are chosen based on the engine's design and performance requirements.
Fuel Injection:
Fuel injection systems are known for their precision and efficiency. This system uses an electronic control unit (ECU) to precisely manage the fuel-air mixture. The ECU receives input from various sensors, such as the engine's speed, temperature, and load, to calculate the optimal fuel-air ratio. High-pressure fuel injectors then spray the fuel directly into the engine's cylinders, ensuring a consistent and accurate fuel supply. This method provides better control over the combustion process, resulting in improved engine performance, reduced emissions, and increased fuel efficiency. Fuel injection systems are commonly found in modern inboard boat engines due to their ability to deliver a precise and consistent fuel-air mixture, leading to enhanced engine performance and reliability.
Carburetors:
Carburetors, on the other hand, are simpler mechanical devices. They mix air and fuel by using a series of passages and a float bowl. As the engine runs, the carburetor draws fuel from the float bowl and mixes it with air, creating a combustible mixture. This mixture is then delivered to the engine's cylinders through a series of throttle plates. Carburetors are known for their simplicity and reliability, making them a popular choice for smaller inboard boat engines. However, they may not provide the same level of precision as fuel injection systems, especially at higher engine speeds or under varying load conditions.
The choice between fuel injection and carburetors depends on the specific requirements of the inboard boat engine. Modern engines often utilize fuel injection for its ability to provide precise fuel management, resulting in improved performance and reduced emissions. Carburetors, while simpler, remain a viable option for certain applications, offering a cost-effective solution for less demanding engine requirements.
Flex Tape's Effectiveness on Hypalon Boats
You may want to see also
Cooling: Engines use water or air cooling to prevent overheating
Inboard boat engines, a popular choice for recreational and commercial vessels, rely on efficient cooling systems to maintain optimal performance and prevent overheating. The cooling mechanism is a critical component, ensuring the engine operates within safe temperature limits, especially during extended periods of use.
One common cooling method is water cooling, where the engine's block and cylinder head are immersed in a coolant liquid. This liquid absorbs heat from the engine components, transferring it to the surrounding water or a separate cooling system. The coolant then circulates through a series of passages within the engine block, dissipating heat to the water or air. This process is often facilitated by a water pump, which ensures a continuous flow of coolant, maintaining a consistent temperature. Water cooling is highly effective as it provides excellent heat dissipation, making it ideal for high-performance engines.
Alternatively, air cooling is employed in some inboard boat engines, particularly those designed for lighter applications or where water cooling might be impractical. Air cooling utilizes fins and fans to draw cool air over the engine components, dissipating heat through convection. This method is simpler and often lighter, making it suitable for smaller boats or those with limited space. The engine's block and head are designed with numerous small passages and fins, maximizing surface area to enhance heat transfer. As the engine operates, the fans create a cooling breeze, drawing in fresh air and expelling warm air, thus keeping the engine cool.
Both cooling methods are essential to ensure the longevity and reliability of inboard boat engines. Overheating can lead to engine damage, reduced performance, and even catastrophic failure. Therefore, engineers design these engines with robust cooling systems, often combining both water and air cooling techniques for optimal results. The choice between water and air cooling depends on factors such as engine size, power output, and the specific requirements of the boat's application.
In summary, inboard boat engines employ water or air cooling systems to manage heat dissipation effectively. Water cooling, with its efficient heat transfer, is common in high-performance engines, while air cooling provides a lightweight solution for smaller boats. Understanding these cooling mechanisms is vital for boat owners and operators to ensure their vessels' engines remain in top condition.
The Mystery of the Missing Boat Bitmoji
You may want to see also
Propeller Drive: The engine's power is transferred to the propeller via a drive shaft
The propeller drive system is a critical component of inboard boat engines, responsible for efficiently transferring the engine's power to the propeller, which in turn propels the vessel forward. This process involves a series of intricate mechanical components working in harmony.
When the engine's power is generated, it is transmitted through a drive shaft, a robust and sturdy metal shaft designed to withstand the immense force. The drive shaft is connected to the engine's output, often a pulley or gear system, which is specifically engineered to match the engine's rotational speed and torque. This connection ensures that the engine's power is effectively harnessed and directed.
As the drive shaft rotates, it engages with a series of gears or pulleys, depending on the engine design. These mechanical components increase or decrease the speed and torque, ensuring the propeller receives the optimal power for efficient propulsion. The drive shaft's rotation is then transferred to the propeller shaft, which is typically a hollow tube running along the length of the boat.
At the end of the propeller shaft, the propeller itself is attached. Propellers are designed with multiple blades that, when rotated, create a forward thrust. The propeller's blades are carefully angled and shaped to optimize water flow, generating lift and pushing the boat forward. The drive shaft's power is now fully utilized, as it directly influences the propeller's rotation and, consequently, the boat's speed and maneuverability.
This system is a marvel of engineering, ensuring that the engine's power is efficiently and effectively converted into the forward motion of the boat. The propeller drive's design and precision are crucial for achieving optimal performance, fuel efficiency, and overall boating experience. Understanding this process highlights the complexity and ingenuity of inboard boat engines.
Lobster Boat Merrimack NH: Opening Hours and More
You may want to see also
Electrical System: Batteries and alternators power the engine's accessories and starting system
The electrical system of an inboard boat engine is a critical component that ensures the engine's functionality and reliability. It primarily relies on two key elements: batteries and alternators. These components work in tandem to provide the necessary power for various engine accessories and the starting system, ensuring a smooth and efficient operation.
Batteries: These are the primary source of electrical energy for the boat's engine. They store the power required to start the engine and provide the initial surge of electricity needed to activate the starter motor. Lead-acid batteries are commonly used in marine applications due to their high capacity and ability to deliver a large amount of current when required. Modern boats often feature deep-cycle batteries, which are designed to withstand frequent deep discharges and provide a steady power supply for extended periods. Proper battery maintenance is essential, including regular cleaning, ensuring secure connections, and monitoring the battery's charge to prevent over-discharge.
Alternators: Alternators are devices that generate electrical power by converting mechanical energy from the engine into electrical energy. As the engine runs, the alternator spins, producing a direct current (DC) that charges the batteries and powers the electrical accessories. This system ensures a continuous supply of electricity, even when the engine is not running, as the alternator can provide the necessary power for the boat's electrical needs. The alternator's output voltage and current must match the requirements of the boat's electrical system to function optimally.
The electrical system's design and functionality are crucial for the overall performance and safety of the boat. Proper wiring, fuses, and circuit breakers are essential to protect against electrical faults and ensure the safe distribution of power. Additionally, the system should be designed to handle the specific power demands of the boat's accessories, such as navigation equipment, lighting, and electronic controls, ensuring that each component receives the required power without overloading the system.
In summary, the electrical system, powered by batteries and alternators, is vital for the operation of inboard boat engines. It provides the necessary energy for starting, accessory functionality, and overall engine performance. Understanding and maintaining this system are essential for boat owners to ensure a reliable and safe boating experience.
The Burger Boat Company: Ownership and Management
You may want to see also
Frequently asked questions
Inboard boat engines are a popular choice for recreational boats and offer a reliable and efficient power source. These engines are mounted inside the boat's hull, with the lower unit (transom-mounted) or the drive shaft extending through the hull and connecting to the propeller. When the engine is started, it drives the propeller, which propels the boat forward or backward. The key components include the engine, transmission, driveshaft, and lower unit. The engine's power is transferred through the driveshaft to the lower unit, which adjusts the speed and torque to match the propeller's needs. This setup provides a compact and streamlined design, allowing for better handling and reduced draft compared to outboard engines.
Inboard and outboard engines differ in their mounting location and design. Inboard engines are mounted inside the boat, typically in the stern or side, with the propeller extending through the hull. This design offers better fuel efficiency, reduced weight, and a lower center of gravity, resulting in improved stability and handling. Outboard engines, on the other hand, are mounted on the outside of the boat, usually on the transom. They provide easier access for maintenance and repair but may affect the boat's stability due to their weight and location.
Regular maintenance is crucial to keep inboard engines running smoothly. Here are some essential maintenance tips:
- Check the engine's oil level regularly and top it up if necessary.
- Inspect the engine for any leaks and address them promptly.
- Change the engine oil and filter at the recommended intervals to prevent wear and tear.
- Keep the cooling system clean and ensure proper water flow to prevent overheating.
- Check the propeller for damage or wear and replace it if necessary.
- Inspect the driveshaft and lower unit for any signs of corrosion or damage.
- Regularly clean the engine and hull to remove dirt and debris.
- Follow the manufacturer's guidelines for specific maintenance tasks and schedules.