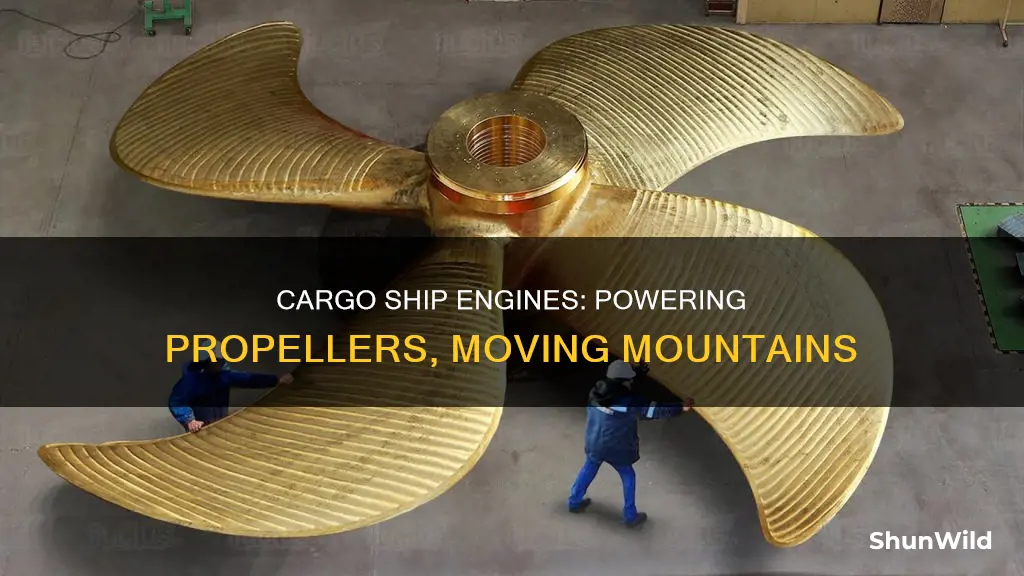
The power requirements of a ship are one of the most important stages of the ship design process, as they determine fuel expenses and the environmental efficiency of the vessel. Most modern ships are propelled by mechanical systems consisting of an electric motor or internal combustion engine driving a propeller. Diesel-mechanical propulsion is preferred for cargo ships that require low-speed operations and lower operating costs. Diesel engines are also more cost-effective, have a straightforward structure, and exhibit high overall efficiency.
Characteristics | Values |
---|---|
Propulsion method | Propellers, pump jets, paddles, sails |
Propeller design | Number of blades, shape, size, angle, pitch |
Power source | Electric motor, internal combustion engine, steam turbine, diesel engine |
Engine type | Two-stroke, four-stroke, turbo-electric transmission |
Fuel type | Diesel, gasoline, LNG, biofuels |
Engine speed | Low speed (300 rpm), medium speed (300-1000 rpm), high speed (1000 rpm) |
Engine components | Crankshaft, camshaft, gearbox, clutch |
Power requirements | Determined by ship's resistance, type of propulsion system, engine or diesel alternator ratings |
Efficiency | Affected by propeller design, engine speed, fuel type, ship speed |
What You'll Learn
The role of propellers in cargo ship movement
Propellers are the driving force behind cargo ships, and their design affects all aspects of a vessel, from handling and riding to comfort, speed, acceleration, engine life, fuel economy, and safety.
Propellers both push and pull water to create forward thrust. As they rotate, they push water backward, creating space in front that water must rush in to fill. Each blade has a pressure differential, with the bottom of the blade creating positive pushing pressure, and the top of the blade creating negative pulling pressure. Most propellers have three or four blades, although they can have more, and each creates these forces simultaneously.
The first commercial ships to be driven by a screw propeller were steamships in the early 19th century. Today, most cargo ships are propelled by mechanical systems consisting of an electric motor or internal combustion engine driving a propeller.
The size of a propeller is determined by factors including RPM, the amount of power provided, the required speed of the vessel, and whether the propeller will be partially surfaced. Larger propellers are used on slower boats, and smaller propellers on faster boats. The number of blades also affects performance—while one blade would be the most efficient setup, it would create a lot of vibration. Therefore, most cargo ships use three or four blades as a compromise between efficiency and reduced vibration.
Pump jets, which are used by water skis and other small craft, are pipes that go through the craft with internal propellers to draw water in and eject it at high pressure. Another alternative is a rim-driven thruster, which integrates an electric motor into a ducted propeller.
Repairing Rubber-Backed Boat Carpet: A Step-by-Step Guide
You may want to see also
How cargo ship propellers are powered by diesel engines
The mechanism or system used to generate thrust and move a watercraft through water is known as marine propulsion. While human-powered paddles and oars were the first forms of marine propulsion, most modern ships are propelled by mechanical systems consisting of an electric motor or internal combustion engine driving a propeller.
Diesel Engines in Marine Propulsion
Diesel engines are widely used in marine propulsion systems due to their operating simplicity, robustness, and fuel economy compared to other prime mover mechanisms. They are known for their high power output and simpler structure, making them ideal for cargo ships and other large vessels. Diesel engines can also utilise different types of fuel oils, including gas oil, marine diesel oil, intermediate fuel oil, marine fuel oil, and heavy fuel oil, providing flexibility in fuel choice.
Powering the Propellers
The propellers in cargo ships are powered by diesel engines through a process that involves several key steps. Firstly, the resistance of the ship is calculated by conducting a towing tank test, which helps determine the power requirements of the vessel. This is followed by selecting the appropriate type of ship propulsion system, with diesel-mechanical propulsion being the preferred choice for cargo ships due to their low-speed operations and lower operating costs.
Diesel-Mechanical Propulsion
In diesel-mechanical propulsion, the diesel engine is directly connected to the propeller through a gearbox, resulting in minimal mechanical losses. This configuration ensures high overall efficiency, and the engine can burn traditional marine fuel oil or low-carbon fuel effectively. However, diesel-mechanical propulsion may suffer from poor manoeuvrability, especially when reversing the ship or during complex steering manoeuvres.
The Role of Propellers
Propellers play a crucial role in the propulsion system by creating thrust and moving the vessel through the water. They operate by pushing water backward and creating a space in the front that water must rush in to fill, generating forward thrust. Most marine propellers are screw propellers with helical blades that rotate on a propeller shaft, similar to the principle of Archimedes' screw.
Efficiency Considerations
The efficiency of cargo ship propellers powered by diesel engines is a key concern. Larger propellers with slower rotation speeds, such as those typically found on large ships, tend to be more efficient than smaller, faster-turning propellers. Additionally, diesel-mechanical propulsion systems may not offer high efficiencies at all torque levels, which is an important consideration for certain types of vessels.
In summary, cargo ship propellers are powered by diesel engines through a combination of mechanical and electrical systems. The selection of diesel engines for marine propulsion offers advantages in terms of power, efficiency, and fuel flexibility. However, it is essential to consider the limitations in manoeuvrability and the potential for higher emissions compared to other propulsion methods.
Repairing Cosmetic Boat Damage: A Step-by-Step Guide
You may want to see also
The design of cargo ship propellers
Propeller Hub or Boss
The propeller has a central boss or hub, similar to the backbone of a traditional table fan. This part mates with the rotating shaft that connects to the engine room mechanism. The shaft transmits the power from the engine to rotate the blades mounted on the hub. Modern designs tend to feature a smaller yet stronger boss to improve efficiency and maintain structural integrity.
Blades
Blades are the most recognisable part of a propeller, akin to the propeller itself. They are mounted on the hub, resembling thin aerofoil sections that create the necessary hydrodynamic lift to generate thrust. Over time, blade designs have evolved into numerous shapes, including foiled, twisted, and torqued configurations, tailored to the specific vessel's design speed and displacement.
Leading and Trailing Edges
The leading edge of a propeller blade is the edge that first pierces the water surface during rotation. The trailing edge is the opposite edge that follows or 'lags' behind the leading edge. The sense of rotation of the propeller determines which edge becomes the leading edge.
Root and Tip
The root is the point of attachment of the blades to the propeller boss or hub. The tip, on the other hand, is the furthest point of the blade from the root, tapering like a leaf. It has the least section width and joins the leading and trailing edges.
Pitch
Pitch refers to the lateral distance traversed by a fixed point when the propeller completes a revolution. It is similar to the pitch on a screw and measures how much the propeller would "drive" or "push forward". The pitch may vary along the length of the blade and is crucial in determining the propeller's effectiveness.
Rake and Skew
When viewed from the side, the blades of the propeller are usually tilted at an angle, either towards the fore-end or the aft end of the ship. This tilt is called rake. The angle of rake depends on the vessel's design, capacity, speed, and other structural factors.
Skew, on the other hand, refers to the sideways tilt of the blade when viewed from the back of the ship. There are two types of skew: balanced and unbalanced. Balanced skew is within smaller limits, while unbalanced skew is a more significant deviation.
Performance and Efficiency
The design of the propeller has a significant impact on the vessel's performance and efficiency. Factors such as the shape, size, angle, and number of blades influence the ship's handling, riding comfort, speed, acceleration, engine life, fuel economy, and safety. For example, larger propellers are generally used on slower boats, while smaller propellers are used on faster vessels.
Materials
The choice of materials for ship propellers is critical, especially considering the corrosive nature of saltwater. Ship propellers commonly use alloys like brass to withstand the harsh marine environment. Additionally, the design must consider the effects of cavitation, which can cause vibration, wear, and damage to the propeller.
The Boys in the Boat: Themes of Resilience and Camaraderie
You may want to see also
The efficiency of cargo ship propellers
Propellers are the driving force behind most ships, and their design is critical to the overall efficiency of the vessel. The following factors are considered when designing cargo ship propellers to ensure optimal performance and fuel efficiency:
Propeller Diameter
The speed of the shaft is closely related to the propeller diameter. While a low shaft speed is beneficial for efficiency, it results in high shaft torque and larger shafts and gearboxes. Therefore, finding the right balance is crucial for propeller performance. Increasing the propeller diameter generally improves propulsive efficiency, but it is limited by the draught of the vessel.
Rotational Speed (RPM)
The rotational speed of the propeller should be different from the resonant frequencies of the shaft, hull, and other machinery. Lower RPM designs often result in higher propulsive efficiency, with reductions in fuel consumption and emissions.
Number of Blades
The number of blades impacts the level of unsteady forces acting on the propeller. From an efficiency standpoint, open water efficiency increases with a higher number of blades. However, all else being equal, adding more blades can reduce overall propeller efficiency due to the disturbance in the flow caused by each blade.
Blade Outline and Area
Research shows that efficiency increases when blade area is decreased as it reduces frictional drag. However, the strength of the propeller must be maintained, and the tip of the blade should be narrower to ensure efficient water flow.
Angle of Attack and Camber
The design of the angle of attack and camber depends on the desired lift, which is determined by the naval architect. A larger angle of attack makes the propeller less susceptible to pressure side cavitation but more susceptible to suction side cavitation.
Pitch/Diameter Ratio
To achieve the best propulsive efficiency for a given propeller diameter, an optimal pitch-to-diameter ratio must be determined, corresponding to a specific design revolution rate.
Energy Saving Devices (ESD)
In addition to the above design considerations, certain external components can improve flow around the propeller, enhancing propulsive efficiency. These include wake equalizing ducts, pre-swirl fin systems, twisted rudders, and propeller boss cap fins, among others.
Hull Form
The hull form also plays a role in propeller efficiency. Bulbous bows designed for high speeds may increase wave-making and decrease vessel performance at lower speeds.
Engine Upgrade/Tuning
When reducing the speed of a vessel, the main engine should be updated or tuned to match the lower speed. This can further improve fuel efficiency, especially when combined with a redesigned propeller optimized for lower RPM and larger diameter.
Odysseus' Men Taken by the Sirens
You may want to see also
The history of cargo ship propellers
The early modern period saw pioneering inventors suggest the use of 'screws' for water propulsion. In 1683, Robert Hooke modified his watermill design to provide motive power for ships through water. In the 1750s, the French mathematician Alexis-Jean-Pierre Paucton suggested a water propulsion system based on the Archimedean screw, and the Academy of Sciences in Paris offered prizes for propeller designs.
In the early 19th century, there were several successful attempts at using propellers to power ships. For example, Edward Shorter's propeller-powered transport ship, 'Doncaster', achieved speeds of 1.5 mph in 1800, and John Stevens' 25-foot vessel with a four-blade propeller reached 4 mph in 1802. However, experimentation with screw propulsion before the 1830s was limited, and those inventions that were tested proved unsatisfactory.
In the 1830s, two British inventors, John Ericsson and Francis Pettit Smith, took out screw propeller patents. Smith demonstrated his wooden propeller on the 'Francis Smith' canal boat on the Paddington Canal from 1836 to 1837. Ericsson demonstrated a 45-foot screw-propelled steamboat on the Thames, reaching speeds of 10 miles per hour.
The SS Archimedes, built in 1838 by Henry Wimshurst, was the world's first steamship successfully driven by a screw propeller. This vessel had a considerable influence on ship development, encouraging the adoption of screw propulsion by the Royal Navy and commercial vessels. Isambard Kingdom Brunel's SS Great Britain, which became the first screw-propelled steamship to cross the Atlantic in 1845, was influenced by the SS Archimedes.
In the late 19th century, progress in propeller design and manufacturing stagnated until the 1970s fuel crisis, which led to an overhaul in the efficiency and cost of maritime travel. Steam propulsion was largely replaced by diesel-electric propulsion, changing how propellers were powered.
A Beginner's Guide: Starting Your Jet Boat Engine
You may want to see also
Frequently asked questions
The three main types of ship propulsion systems are mechanical propulsion, electric propulsion, and hybrid propulsion. Mechanical propulsion is the most traditional method, with most ships currently using this system. Electric propulsion offers exceptional manoeuvrability and reduced noise levels, making it suitable for cruise ships and ferries. Hybrid propulsion combines both mechanical and electric propulsion, offering increased energy efficiency and improved manoeuvrability.
Propellers create forward thrust by pushing water backward, which creates space for water to rush in and fill the front. This process pulls water in and pushes it out at a higher speed, generating the force that moves a vessel through the water. Propellers can have a single blade but typically have three or four to balance the forces involved.
The number of blades on a ship propeller impacts the performance of the boat. A single blade would be the most efficient setup but would create a lot of vibration. Three or four blades are most common as they balance efficiency and reduced vibration. Five-bladed propellers are also used in some cases.
Propellers are much more efficient than jet engines for powering cargo ships because water provides much higher resistance than air, making it easier to push against. Propeller-driven ships can be powered by gas turbines, which are similar to jet engines but work differently and don't propel ships through ejected air.