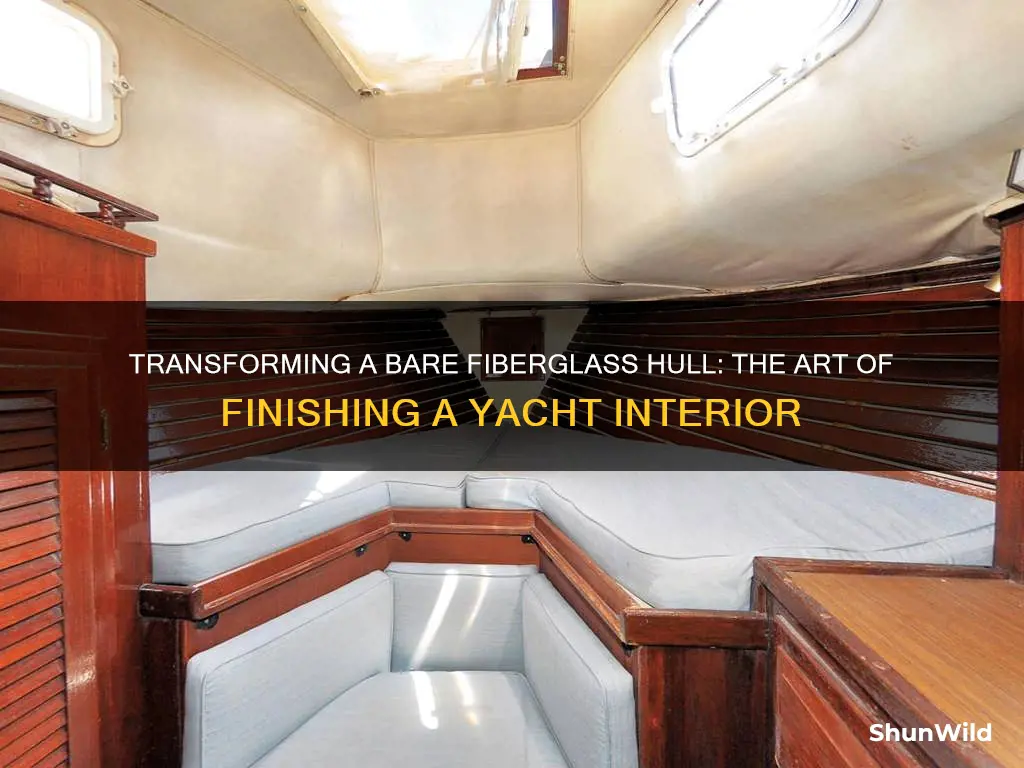
Boat builders face a challenging task when it comes to finishing the interior of a bare fiberglass yacht. The process involves several intricate steps to ensure a smooth, durable, and aesthetically pleasing interior. This process typically begins with thorough cleaning and preparation of the fiberglass surface, followed by the application of specialized primers and paints to create a seamless and long-lasting finish. The interior is then fitted with various components such as countertops, cabinetry, and seating, all of which require precise installation to ensure structural integrity and a luxurious feel. Finally, the interior is often finished with a protective coating to enhance its resistance to wear and tear, ensuring the yacht's interior remains beautiful and functional for years to come.
What You'll Learn
- Sealing Gaps: Use marine-grade sealants to fill gaps and prevent water intrusion
- Wooden Trim: Apply marine-grade wood finishes for a classic, durable look
- Upholstery: Choose marine-grade fabrics and foam for comfort and durability
- Electrical Wiring: Route and secure wiring with marine-grade connectors and insulation
- Ventilation: Install marine-grade vents for proper airflow and moisture control
Sealing Gaps: Use marine-grade sealants to fill gaps and prevent water intrusion
Sealing gaps is a crucial step in finishing a bare fiberglass yacht interior, as it ensures the boat's structural integrity and prevents water intrusion. When dealing with a bare fiberglass hull, it's essential to pay close attention to the smallest details, as even a tiny gap can become a significant issue over time. Marine-grade sealants are specifically designed to withstand the harsh marine environment, making them the ideal choice for this task.
The process begins with identifying all the gaps that need to be addressed. These can include gaps between the fiberglass panels, around windows and doors, and any other openings where water might find its way into the boat. It's important to use a sharp tool, such as a utility knife or a specialized gap-filling tool, to carefully cut and create a clean, precise edge for the sealant. This step ensures that the sealant adheres properly and provides an effective barrier.
Once the gaps are prepared, it's time to apply the marine-grade sealant. These sealants are typically available in various forms, such as tubes or cartridges, making application convenient. When applying the sealant, it's crucial to use a generous amount to ensure complete coverage. Start by applying the sealant to one side of the gap, then carefully smooth it out with a spatula or a finger, depending on the consistency of the sealant. Ensure that the sealant is level and flush with the surface on both sides of the gap.
After the sealant has been applied and smoothed, allow it to cure according to the manufacturer's instructions. Marine-grade sealants typically cure within a few hours to a full day, depending on the type. During this time, it's essential to avoid any pressure or force on the sealed area to ensure a strong bond. Once cured, the sealant will create a robust, flexible barrier that effectively seals the gaps and prevents water from seeping in.
Regular maintenance and reapplication of marine-grade sealants are recommended to maintain the yacht's interior integrity. Over time, sealants can degrade due to UV exposure, temperature changes, and other environmental factors. By periodically inspecting and reapplying the sealants, boat owners can ensure that their yacht remains watertight and well-protected. This simple yet effective technique is a fundamental part of boat building and maintenance, ensuring a durable and long-lasting vessel.
Mysterious Water Droplets: A Boat's Cabin Mystery
You may want to see also
Wooden Trim: Apply marine-grade wood finishes for a classic, durable look
When it comes to finishing a bare fiberglass yacht interior, boat builders often seek to enhance the aesthetic appeal and durability of the space. One popular choice for achieving a classic and elegant look while ensuring long-lasting results is the application of marine-grade wood finishes. This technique not only adds a touch of warmth and sophistication but also provides excellent protection against the harsh marine environment.
Marine-grade wood finishes are specifically designed to withstand the challenges posed by saltwater and UV radiation. These finishes are typically made from high-quality, durable materials that can resist fading, chalking, and deterioration over time. Boat builders often prefer natural wood species such as teak, mahogany, or cherry, which offer a rich, warm tone and exceptional durability. The process begins with carefully selecting the wood and ensuring it is properly prepared by removing any imperfections and smoothing the surface.
To apply the finish, boat builders often use a multi-step process. First, a primer is applied to the wood surface to create a smooth base and ensure better adhesion. This primer should be marine-grade and designed to withstand the marine environment. After the primer dries, a high-quality marine-grade wood stain or paint is applied. These products come in various colors, allowing boat owners to customize the interior to their desired aesthetic. The stain or paint is carefully brushed or sprayed onto the wood, ensuring an even and consistent coverage.
Once the stain or paint is applied, the boat builders will often add a protective topcoat. This topcoat serves multiple purposes: it adds a layer of durability, protects the wood from moisture and UV rays, and contributes to the overall finish's longevity. Marine-grade clear coatings, such as polyurethanes or epoxy resins, are commonly used for this purpose. These coatings are carefully applied and cured to ensure a smooth, glossy surface that enhances the wood's natural beauty.
By utilizing marine-grade wood finishes, boat builders can create a stunning and functional interior. The natural beauty of wood, combined with its durability, provides a timeless and elegant solution for finishing bare fiberglass yacht interiors. This method not only enhances the overall appearance but also ensures that the yacht's interior can withstand the rigors of marine life, making it a popular choice among boat enthusiasts.
Selling Your Bass Boat: Tips for a Quick Sale
You may want to see also
Upholstery: Choose marine-grade fabrics and foam for comfort and durability
When it comes to finishing the interior of a bare fiberglass yacht, choosing the right upholstery is crucial for both comfort and durability. Marine-grade fabrics and foam are specifically designed to withstand the harsh marine environment, offering a reliable and long-lasting solution for boat builders. These materials are engineered to resist the elements, including UV rays, saltwater, and the constant motion of the sea, ensuring that the yacht's interior remains in excellent condition for years to come.
Marine-grade fabrics are typically made from durable synthetic materials such as polyester or nylon. These fabrics are highly resistant to fading, stretching, and tearing, making them ideal for the demanding conditions of a boat interior. They are also easy to clean and maintain, which is essential for a space that may be exposed to spills, stains, and general wear and tear. Look for fabrics that are specifically labeled as marine-grade or boat-grade, as these will have the necessary properties to handle the unique challenges of a yacht's interior.
The choice of foam is equally important. Marine-grade foam is designed to provide comfort and support while also being durable. It is typically made from high-density polyurethane foam, which offers excellent resilience and shape retention. This foam is resistant to compression and will maintain its structure even with frequent use. When selecting foam, consider the thickness and density required for the specific application. Thicker foam will provide more padding and comfort, especially in areas like seating and sleeping quarters, while denser foam is ideal for structural integrity and support.
In addition to the materials, the construction of the upholstery is key. Marine-grade fabrics and foam should be carefully sewn and bonded to ensure a secure and long-lasting finish. The stitching should be reinforced to withstand the constant movement and potential impact of a boat's interior. Consider using heavy-duty threads and ensuring that all seams are securely finished to prevent any potential tears or damage.
By utilizing marine-grade fabrics and foam, boat builders can create a yacht interior that is not only aesthetically pleasing but also highly functional and long-lasting. These materials provide the necessary comfort, durability, and resistance to the marine environment, ensuring that the yacht remains a pleasure to be on for its owner and passengers.
Unveiling Boys in the Boat: A Biographical Journey
You may want to see also
Electrical Wiring: Route and secure wiring with marine-grade connectors and insulation
When it comes to electrical wiring in a bare fiberglass yacht interior, the goal is to create a system that is both functional and durable, capable of withstanding the marine environment. The process involves careful planning, precise routing, and the use of specialized components designed for marine applications. Here's a detailed guide on how to approach this task:
Planning the Wiring Route: Before any wiring begins, it's crucial to have a comprehensive plan for the electrical layout. This includes identifying the locations of various electrical components, such as switches, outlets, lighting fixtures, and electronic devices. Create a detailed diagram or layout plan, ensuring that all wiring runs are logical and easily accessible for future maintenance. Consider the aesthetics of the interior as well; wiring should be discreet and blend seamlessly with the overall design.
Marine-Grade Connectors and Insulation: Utilizing marine-grade connectors is essential for ensuring a secure and reliable electrical connection. These connectors are designed to withstand the harsh marine environment, including exposure to salt water, temperature fluctuations, and vibration. Look for connectors that are corrosion-resistant and have a robust sealing mechanism. Insulation is another critical aspect; marine-grade insulation materials should be used to protect the wiring from moisture, UV radiation, and physical damage. This insulation should be flexible enough to navigate around tight spaces but also durable to handle the rigors of the boat's operation.
Routing the Wires: Start by running the main power supply lines to the various electrical panels and distribution boards. These lines should be securely fastened to the boat's structure using appropriate mounting hardware. For smaller wires and control cables, consider using a combination of bulkheads and stringers as guides. Ensure that all wiring routes are protected from sharp edges and potential damage during the construction process. Keep the wiring as straight and short as possible to minimize the risk of chafing and to make future repairs easier.
Securing and Organizing Wiring: Once the wiring routes are established, it's time to secure the wires in place. Use marine-grade wire ties or clips that are designed to resist corrosion and UV degradation. Space the ties evenly to prevent excessive tension on the wires. Consider using wire loom or conduit in areas where the wiring needs to be protected from physical contact or where a neater appearance is desired. Proper organization of the wiring not only looks professional but also makes troubleshooting and maintenance much simpler.
Testing and Final Touches: After the wiring is installed, conduct thorough testing to ensure everything functions correctly. Check for proper voltage, continuity, and the absence of short circuits. Verify that all switches, controls, and electronic devices respond as expected. Once the electrical system is proven reliable, add any final touches, such as labeling switches and outlets for easy identification. This step is crucial for the boat's long-term usability and safety.
Shifting Seats on a Boat: Distance Covered?
You may want to see also
Ventilation: Install marine-grade vents for proper airflow and moisture control
Ventilation is a critical aspect of finishing a bare fiberglass yacht interior, ensuring a comfortable and healthy environment for the crew and passengers. Proper airflow and moisture control are essential to prevent the growth of mold and mildew, which can be detrimental to the boat's interior and the well-being of its occupants. When designing the ventilation system, boat builders should consider the unique challenges of marine environments, such as high humidity and varying weather conditions.
One effective solution is to install marine-grade vents, specifically designed to withstand the harsh marine climate. These vents are typically made from durable materials like stainless steel or corrosion-resistant alloys, ensuring longevity even in salty and humid conditions. Marine-grade vents offer several advantages over standard vents. Firstly, they are designed to be more robust and weather-resistant, capable of withstanding the constant exposure to saltwater and UV radiation. This durability is crucial to ensure the vents' longevity and performance over time.
The installation process involves carefully selecting the appropriate vent size and placement to ensure optimal airflow. Vents should be positioned to allow for a gentle, continuous flow of air throughout the interior, avoiding any dead zones or areas of poor ventilation. Proper placement also helps to prevent the accumulation of moisture in specific areas, which can lead to mold and mildew issues. Boat builders can consider installing vents in strategic locations, such as near windows, portholes, or in the walls, to create a well-ventilated space.
In addition to vents, boat builders can incorporate other ventilation techniques to enhance the system's effectiveness. This may include the use of exhaust fans, which can be strategically placed to draw moist air out of the interior and expel it overboard. Proper ventilation also involves managing the airflow direction, ensuring that moist air is directed away from the interior and towards the exterior of the boat. This can be achieved by using directional vents or fans with adjustable settings.
By implementing a comprehensive ventilation system with marine-grade vents, boat builders can create a comfortable and healthy interior environment. This not only enhances the overall experience for the crew and passengers but also contributes to the long-term maintenance and preservation of the yacht's interior, ensuring it remains in excellent condition despite the challenging marine conditions. Proper ventilation is a key element in the finishing process, addressing the unique challenges posed by the marine environment.
Life Jacket Necessity: Paddle Boats and Safety
You may want to see also
Frequently asked questions
The initial step is to ensure the surface is clean and free of any contaminants. This involves thorough cleaning with a suitable solvent to remove any dirt, grease, or old finishes. It's crucial to follow this with a thorough inspection to identify any imperfections, such as scratches, holes, or delaminations, which need to be addressed before the final finish is applied.
Preparation is key to a successful finish. After cleaning, the surface should be lightly sanded with fine-grit sandpaper (typically 600-1200 grit) to create a smooth, uniform texture. This step helps the final finish adhere better and ensures a professional-looking result. It's important to wipe away any dust after sanding to avoid any residue.
There are several popular choices for interior finishes, including:
- Epoxy Resin: This is a two-part system that provides a strong, durable bond and a smooth, glossy finish. It is often used for its ability to fill small imperfections and create a seamless surface.
- Polyurethane: A clear, hard-wearing finish that adds a beautiful shine and protects the surface from UV damage and stains. It requires multiple thin coats for optimal results.
- Vinyl Wrap: A cost-effective option, vinyl can be used to create unique designs and patterns, offering a modern aesthetic. It is applied in layers and sealed for long-lasting protection.