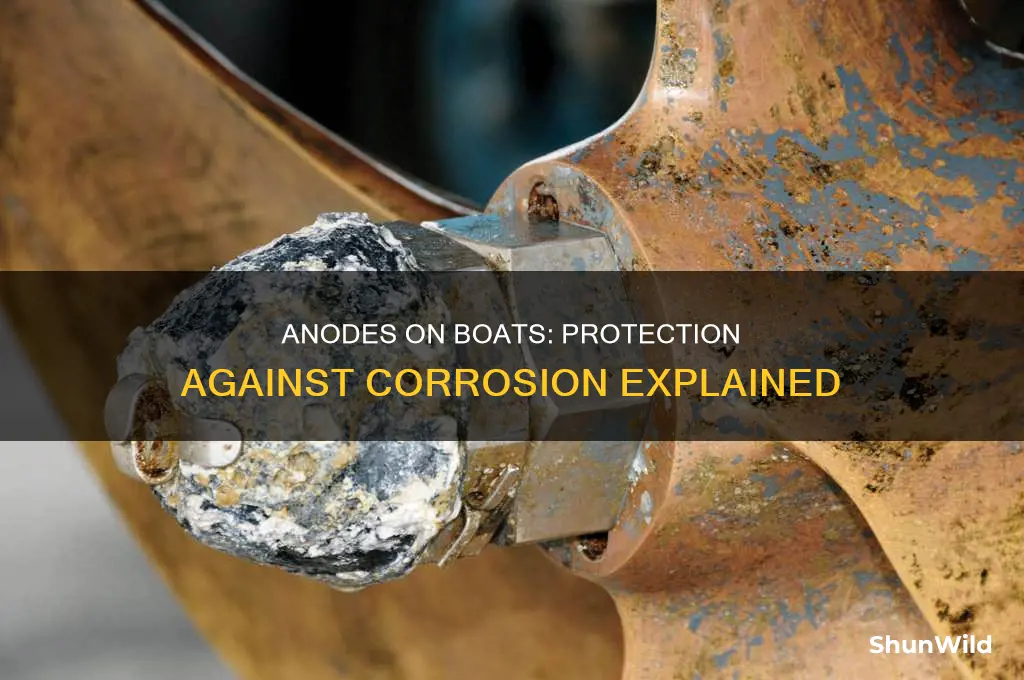
Anodes are placed underneath boats and attached to all metal parts to prevent corrosion. They are also known as sacrificial blocks or sacrificial anodes because they corrode faster than the boat's metal, preserving the metal parts for longer. Anodes are made of zinc, aluminium or magnesium, and they work similarly to electrolysis to bring about a chemical reaction.
Characteristics | Values |
---|---|
Placement | Underneath the boat, attached to all metal parts |
Attachment | Welding, bolting, tying with brackets |
Conductivity | Must be free of paint and other solvents |
Material | Zinc, aluminium, magnesium |
Function | Protect metal parts by absorbing ions that damage boat metal during corrosion |
Corrosion | Sacrifices itself by corroding faster than boat metal |
Connection | Must be connected to the component it is protecting through direct contact or a wire |
What You'll Learn
How to attach anodes to a boat
Anodes are placed underneath the boat and attached to all metal parts. They are secured by welding them to a metal hull surface or directly onto metal components. They can also be bolted and tied with brackets, which makes them easier to replace.
To attach anodes to a boat, you should first ensure that the anodes are not painted or covered in any other solvents, as this will render them useless. Then, attach the anodes to the metal parts of the boat. They can be welded, bolted, or tied with brackets. If you want to replace them easily, it is best to bolt or tie them.
It is important to note that anodes must remain submerged to perform their function. They work by corroding faster than the boat's metal, preserving the metal parts for longer. Anodes are made of different types of material, such as zinc, aluminium, or magnesium, and their purpose is to protect metal parts by absorbing ions that damage the boat's metal during corrosion.
For the anode to work correctly, it must be connected to the component it is protecting either through direct contact or through a wire connecting the two parts.
The Ultimate Guide to Titling Your Boat in Delaware
You may want to see also
Why anodes should not be painted
Anodes are placed underneath boats, attached to all metal parts to protect them from corrosion. They are also known as sacrificial blocks or sacrificial anodes because they corrode faster than the boat's metal, preserving the metal parts for longer.
Anodes should not be painted as they will lose their conductivity. This is because anodes are made of different types of material, such as zinc, aluminium or magnesium, and their purpose is to protect metal parts by absorbing ions that damage the boat's metal during corrosion. If an anode is painted, it will not be able to absorb these ions and will therefore not be able to protect the metal parts of the boat.
Additionally, for anodes to work correctly, they must be connected to the component they are protecting either through direct contact or through a wire. If an anode is painted, it may not be able to make this connection, rendering it useless.
It is also important to never paint a component before the anode is installed, as this will also cause the anode to lose its conductivity. This is because the paint will create a barrier between the anode and the metal part, preventing the two from making direct contact.
Finally, anodes should be kept untouched and free of solvents when attached to metal parts. This is to ensure that they remain tightly in place and are able to perform their function optimally.
Replacing a Lost Boat Title in Georgia: A Simple Guide
You may want to see also
How anodes protect metal structures from corrosion
Anodes are placed underneath a boat, attached to all metal parts and must remain submerged to perform their function. They are secured by welding them to a metal hull surface or directly on metal components. Or, they are bolted and tied with brackets.
Anodes are also called sacrificial blocks or sacrificial anodes because they wear away quicker due to the fast rate of corrosion. They essentially ‘sacrifice’ themselves by corroding faster rather than the boat's metal, with the aim of preserving the metal parts for longer. Anodes are made of different types of material, like zinc, aluminium or magnesium, and their purpose is to protect metal parts by absorbing ions that damage the boat's metal during corrosion.
Water and air provide the perfect environment for oxidation and with constant exposure to these elements, a boat's metals are subject to falter. Anodes work similarly to electrolysis to bring about a chemical reaction in something that would otherwise not react.
For anodes to perform optimally, they should stay untouched and free of paint and other solvents when attached to the metal parts or they will lose conductivity.
The Ultimate Guide to Antebellum Boat Paint
You may want to see also
The types of corrosion
Anodes are placed underneath a boat and attached to all metal parts. They are secured by welding, bolting or tying with brackets. They are made of zinc, aluminium or magnesium and protect metal structures from corroding by absorbing ions that damage the boat's metal during corrosion.
There are two basic types of corrosion: erosion and electro-chemical. Erosion can be caused by high-speed water flow, for example, the pitting seen on rudder blades behind propellers. Electro-chemical corrosion is the primary type of corrosion that boat owners have to deal with.
There are also other types of corrosion, including simple, electrolytic, crevice, galvanic and stray current corrosion. Simple corrosion occurs when molecules on a metal surface bond with oxygen, causing oxidation. Galvanic corrosion can occur when two different types of metal are in contact with water, creating the possibility of current flow.
Decoding Boat Hull ID: RTC004MBJ788 Explained
You may want to see also
The different materials anodes are made from
Anodes are placed underneath a boat and attached to all metal parts. They are usually secured by welding them to a metal hull surface or directly onto metal components. They can also be bolted and tied with brackets. Anodes are made from different materials, such as zinc, aluminium or magnesium. These materials are chosen because they corrode faster than the boat's metal, preserving the metal parts for longer. This process is called galvanic corrosion.
The purpose of anodes is to protect the metal parts of a boat by absorbing ions that would otherwise damage the boat's metal during corrosion. Water and air provide the perfect environment for oxidation, so boats are particularly susceptible to this. Anodes work in a similar way to electrolysis, bringing about a chemical reaction.
Anodes must be connected to the component they are protecting either through direct contact or through a wire. They should not be painted or touched, as this will render them useless. Anodes are also known as sacrificial blocks or sacrificial anodes because they sacrifice themselves by corroding faster than the boat's metal.
If anodes are not replaced regularly, the metal parts of the boat will corrode faster, leading to costly replacements.
Repairing Soft Spots in Your Center Console Boat: A Guide
You may want to see also
Frequently asked questions
Anodes are sacrificial materials that are added to a boat circuit to protect metal structures from corroding. They are placed underneath the boat, attached to all metal parts and must remain submerged to perform their function.
Anodes work similarly to electrolysis to bring about a chemical reaction. They essentially 'sacrifice' themselves by corroding faster than a boat's metal, with the aim of preserving the boat's metal parts for longer.
Anodes are made of different types of material, like zinc, aluminium or magnesium.
Anodes are secured by welding them to a metal hull surface or directly on metal components. They can also be bolted and tied with brackets.
Anodes should never be painted as they will lose their conductivity and become useless.