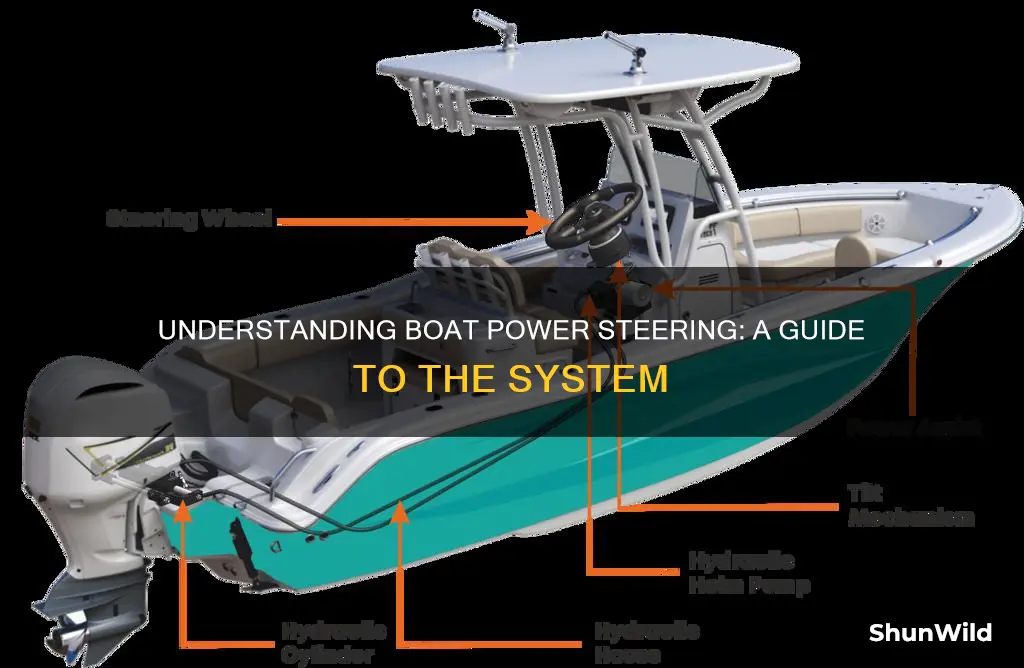
Boat power steering systems are an essential component of any vessel, big or small. They work by utilising hydraulic pressure to turn the boat's steering wheel. This makes steering easier and more effortless, reducing operator fatigue and improving safety. Without a power steering system, the operator would have to rely on physical strength to steer the boat, which can be exhausting and even dangerous in rough waters.
Characteristics | Values |
---|---|
How it works | Utilises hydraulic pressure to turn the boat's steering wheel |
Steering wheel | Connected to a hydraulic pump that draws fluid from a reservoir and sends it to a hydraulic cylinder or ram |
Hydraulic cylinder or ram | Connected to the boat's rudder or outboard motor, allowing the hydraulic pressure to turn the steering mechanism |
Hydraulic system | Operates under high pressure, which is regulated by a control valve |
Control valve | Controls the amount of fluid that flows into the cylinder, depending on the position of the steering wheel |
Importance | Responsible for the smooth and effortless steering of the vessel, making it easier for the operator to navigate through the water |
Benefits | Enhances steering control, reduces operator fatigue, improves safety, and makes it easier to turn the boat even with a heavy load |
What You'll Learn
Hydraulic steering systems
A boat power steering system is a vital component in any boat, whether big or small. It is responsible for the smooth and effortless steering of the vessel, making it easier for the operator to navigate through the water. Without it, the boat operator would have to rely on physical strength to steer the vessel, which can be exhausting and even dangerous in rough waters.
A power steering system makes it easy to turn the boat, even with a heavy load, allowing the operator to maintain control and avoid accidents. It requires less effort to turn the steering wheel, allowing the operator to stay focused and alert, especially during long trips.
This type of hydraulic steering operates similarly to the engine-driven power steering system, but without the engine-driven pump. The hydraulic power comes from a standalone electric motor, usually supplied with DC power. These systems vary in design. While their primary application lies with large centre console boats powered by multiple outboards, electric power steering pumps are becoming more popular in sportfish boats.
Exploring Cinematic Adaptations: The Boys in the Boat Franchise
You may want to see also
Electric power steering pumps
Boat power steering systems use hydraulic pressure to turn the boat's steering wheel. The steering wheel is connected to a hydraulic pump that draws fluid from a reservoir and sends it to a hydraulic cylinder or ram. The cylinder or ram is connected to the boat's rudder or outboard motor, allowing the hydraulic pressure to turn the steering mechanism. The hydraulic system operates under high pressure, which is regulated by a control valve. The control valve controls the amount of fluid that flows into the cylinder, depending on the position of the steering wheel. This makes it easy to turn the boat, even with a heavy load, and reduces operator fatigue.
The constantly running electric hydraulic pump provides a smooth and consistent steering feel. The pump runs continuously, even when the steering wheel is not being turned, to maintain hydraulic pressure in the system. This allows for quick and responsive steering input at all times.
On the other hand, the on-demand electric motor pump only activates when the steering wheel is turned. This design conserves energy and reduces wear and tear on the pump by only operating when needed. The steering feel may be slightly different due to the pump needing to ramp up to full power each time it is activated, resulting in a slight delay in response time compared to the constantly running pump.
Both designs have their advantages and are suitable for different applications. The constantly running pump may be preferred for boats that require quick and immediate steering responses, such as high-performance or racing boats. On the other hand, the on-demand pump can be a more energy-efficient option for boats with less demanding steering requirements. Ultimately, the choice of electric power steering pump design depends on the specific needs and preferences of the boat operator.
Boat Engines: Annual CO2 Emissions and Their Impact
You may want to see also
Steering control
A boat power steering system is a vital component in any boat, big or small. It enhances steering control, reduces operator fatigue and improves safety.
Boat power steering systems work by using hydraulic pressure to turn the boat's steering wheel. The steering wheel is connected to a hydraulic pump that draws fluid from a reservoir and sends it to a hydraulic cylinder or ram. The cylinder or ram is connected to the boat's rudder or outboard motor, allowing the hydraulic pressure to turn the steering mechanism. The hydraulic system operates under high pressure, which is regulated by a control valve. The control valve controls the amount of fluid that flows into the cylinder, depending on the position of the steering wheel.
The power steering system makes it easy to turn the boat, even with a heavy load, allowing the operator to maintain control and avoid accidents. It requires less effort to turn the steering wheel, allowing the operator to stay focused and alert, especially during long trips.
There are two design styles of electric power steering systems: one with a constantly running electric hydraulic pump and the other with an on-demand electric motor pump. While the end result is similar, the feel of the system and response time is slightly different.
Sailing Boat Folding: A Step-by-Step Guide to Success
You may want to see also
Operator fatigue
Boat power steering systems reduce operator fatigue by making it easier to turn the steering wheel. This requires less effort from the operator, allowing them to stay focused and alert, especially during long trips. Without power steering, the operator would have to rely on physical strength to steer the vessel, which can be exhausting and even dangerous in rough waters.
Power steering systems use hydraulic pressure to turn the boat's steering wheel. The steering wheel is connected to a hydraulic pump that draws fluid from a reservoir and sends it to a hydraulic cylinder or ram. The cylinder or ram is then connected to the boat's rudder or outboard motor, allowing the hydraulic pressure to turn the steering mechanism. The hydraulic system operates under high pressure, which is regulated by a control valve that controls the amount of fluid that flows into the cylinder depending on the position of the steering wheel.
There are two main types of power steering systems for boats: engine-driven and electric. Engine-driven systems use an engine-driven pump to generate hydraulic power, while electric systems use a standalone electric motor, usually supplied with DC power. Electric power steering pumps are becoming more popular in sportfish boats, and there are two design styles: one with a constantly running electric hydraulic pump and the other with an on-demand electric motor pump. While the end result is similar, the feel of the system and response time is slightly different.
Boat Docking Options Near North Conway, NH
You may want to see also
Safety
Boat power steering systems are an essential component of any boat, big or small, and are vital to the safety of the vessel. They work by utilising hydraulic pressure to turn the boat's steering wheel. The steering wheel is connected to a hydraulic pump that draws fluid from a reservoir and sends it to a hydraulic cylinder or ram. The cylinder or ram is then connected to the boat's rudder or outboard motor, allowing the hydraulic pressure to turn the steering mechanism.
The hydraulic system operates under high pressure, which is regulated by a control valve. This control valve is responsible for controlling the amount of fluid that flows into the cylinder, depending on the position of the steering wheel. This ensures that the operator maintains control and can avoid accidents.
Boat power steering systems improve steering control and reduce operator fatigue by requiring less effort to turn the steering wheel. This is especially important during long trips or in rough waters, where physical strength to steer the vessel can be exhausting and even dangerous.
Electric power steering systems are also available, supplied with DC power and featuring an electric hydraulic pump or an on-demand electric motor pump. These systems are becoming more popular in sportfish boats.
Boat Slip Ownership: Is It Worth the Cost?
You may want to see also
Frequently asked questions
Boat power steering works by using hydraulic pressure to turn the boat's steering wheel. The steering wheel is connected to a hydraulic pump that draws fluid from a reservoir and sends it to a hydraulic cylinder or ram. The cylinder or ram is then connected to the boat's rudder or outboard motor, allowing the hydraulic pressure to turn the steering mechanism.
Boat power steering improves steering control, reduces operator fatigue, and improves safety. It requires less effort to turn the steering wheel, allowing the operator to stay focused and alert, especially during long trips.
The hydraulic system operates under high pressure, which is regulated by a control valve. The control valve controls the amount of fluid that flows into the cylinder, depending on the position of the steering wheel.
There are two main types of power steering systems available for boats: engine-driven power steering systems and hydraulic power steering systems. Electric power steering pumps are becoming more popular in sportfish boats, and there are two design styles of these systems: one with a constantly running electric hydraulic pump and the other with an on-demand electric motor pump.
Boat power steering is a vital component in any boat, big or small. Without it, the operator would have to rely on physical strength to steer the vessel, which can be exhausting and dangerous, especially in rough waters.