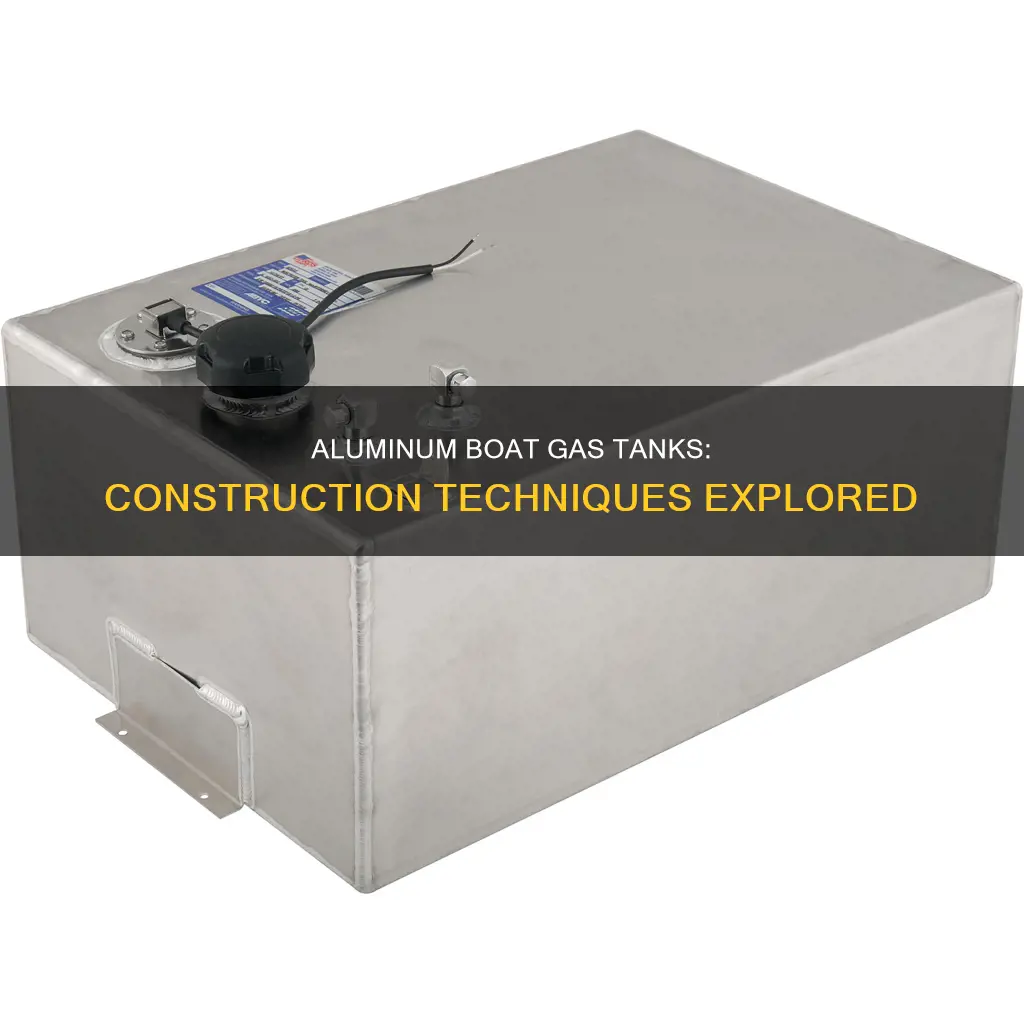
Aluminum is a popular material for constructing boat gas tanks due to its strength, lightweight nature, and anti-corrosive properties. Boat gas tanks are typically made from marine-grade aluminum, specifically Grade 5052, 5086, or 5083. The construction process involves fabricating the aluminum sheets to meet specific requirements, such as thickness and shape, and treating them with a protective coating to enhance their performance and durability. Customization is a key aspect of aluminum boat gas tank construction, with fabricators often working from customer specifications, drawings, or even replicating old tanks.
What You'll Learn
Why aluminium is used for boat gas tanks
Aluminium is used for boat gas tanks because of its ability to withstand constant exposure to saltwater. Unlike stainless steel, which is another material used in marine fuel tanks, aluminium does not corrode over time due to saltwater exposure. This anti-corrosive property of aluminium is further enhanced by treating it with a protective polymer coating that inhibits oxidation, tarnishing, and staining.
Aluminium is also lightweight and strong, making it ideal for marine applications. Its high-density properties give it strength, while its low melting point makes it suitable for the fabrication process without losing its ability to resist water damage. This means that aluminium fuel tanks can withstand the intense forces a ship might experience at sea without leaking.
Another advantage of using aluminium for boat gas tanks is its malleability. Aluminium is a "soft" metal that can be easily fabricated and shaped using CNC plasma or waterjet cutting. This malleability allows fabricators to craft fuel tanks that precisely fit the unique spaces available on different vessels.
To ensure the durability and safety of aluminium boat gas tanks, fabricators follow guidelines from the American Boat and Yacht Council (ABYC) and the United States Coast Guard. These guidelines specify the grade of aluminium, minimum thickness, and the inclusion of features such as mounting brackets and internal baffles to minimise fuel sloshing.
Bunk Spacing on Boat Lifts: How Much Space Is Needed?
You may want to see also
The construction process
Aluminum is a popular material for constructing boat gas tanks due to its strength, lightweight nature, and anti-corrosive properties. The construction process for an aluminum boat gas tank typically involves the following steps:
Planning and Design
First, the fabricator will need to know the specifications of the tank, including its shape, size, and capacity. This information is crucial as boat gas tanks need to fit precisely into the available space on the vessel. Customers can provide drawings or the measurements of their old tank for reference. The United States Coast Guard has specific guidelines for fuel tanks that must be adhered to during the design process.
Material Selection
Grade 5086, 5083, or 5052 aluminum is typically used for marine fuel tanks, with a minimum thickness of 0.90 inches for small tanks and a range of 0.125 to 0.250 inches for larger tanks. This aluminum is marine grade, meaning it can withstand saltwater exposure without corroding over time, which is a common issue with stainless steel tanks.
Fabrication
The fabrication process begins with bending the aluminum plate to form the tank's shape. CNC press brakes are used to bend the metal accurately, and it is preferable to bend the corners rather than weld them. The fabricator will then weld the ends and lid of the tank securely. Internal baffles are added to prevent fuel from sloshing around, with notches to eliminate air pockets in the corners. Mounting brackets are welded onto the tank to allow for secure installation in the boat.
Welding
TIG welding and MIG welding are common techniques for joining the aluminum components. MIG welding is often used for the interior of the tank to increase speed, while TIG welding is used for the fittings to improve accuracy.
Coating and Protection
To enhance the tank's durability and protect against corrosion, a protective coating can be applied. This could be an epoxy coating or a polymer treatment to inhibit oxidation, tarnishing, and staining.
Testing
Once the construction is complete, a pressure test is performed to ensure the tank does not leak. This is a crucial step to guarantee the safety and functionality of the gas tank.
Boat Battery Lifespan: Replacement Frequency and Maintenance Tips
You may want to see also
Tank shapes
Aluminum boat gas tanks can be square, rectangular, or V-bottom-shaped. The shape of the tank is determined by the available space in the boat and the specific requirements of the vessel.
When designing the shape of an aluminum boat gas tank, it is important to consider the size and layout of the boat. The tank must fit precisely into the designated space, taking into account any obstacles or structural elements that may impact the shape and size of the tank.
Square and rectangular tanks are common choices as they can be easily adapted to fit the available space. These shapes also allow for efficient use of space, maximizing fuel capacity within the given dimensions.
V-bottom-shaped tanks are often used in boats with a V-shaped hull. This shape allows the tank to fit snugly into the hull, utilizing the available space efficiently. V-bottom tanks are typically welded together from several pieces of aluminum, with mounting brackets added for secure installation.
Additionally, the overall size of the tank will determine the thickness of the aluminum required. Smaller tanks may use thinner aluminum sheets, while larger tanks will need thicker material to ensure structural integrity.
It is worth noting that all boat gas tanks must follow specific guidelines set by organizations like the American Boat and Yacht Council (ABYC) and the United States Coast Guard. These guidelines ensure the safe and proper construction of fuel tanks, including specifications for materials, thickness, and construction methods.
Phoenician Seafaring: Exploring Ancient Navigation Limits
You may want to see also
Welding techniques
Aluminium boat gas tanks are constructed using a variety of welding techniques, depending on the specific requirements and preferences of the manufacturer and customer. Here is an overview of the welding processes involved:
- TIG Welding: TIG welding, or Tungsten Inert Gas welding, is a common technique used in aluminium boat gas tank construction. It involves using a non-consumable tungsten electrode to create an arc that melts the base metal and fuses the pieces together. This method is often chosen for its precision and accuracy, especially when welding the fittings of the tank. TIG welding produces strong, high-quality welds and is ideal for thinner aluminium sheets.
- MIG Welding: MIG welding, or Metal Inert Gas welding, is another popular technique. It uses a consumable wire electrode fed through a welding gun, along with an inert gas shield, to create the weld. MIG welding is faster than TIG welding, making it suitable for welding the insides of the tank. It is versatile and can be used on a range of aluminium thicknesses.
- Plug Welding: This technique is used to weld the baffles inside the tank. Plug welding involves creating a hole in one of the pieces to be joined and then welding through the hole to create a solid, strong joint. This ensures that the baffles are securely attached and can effectively prevent fuel from sloshing around.
- CNC Press Brake: While not strictly a welding technique, the use of a CNC press brake is an important aspect of aluminium boat gas tank construction. This equipment allows fabricators to bend the aluminium plates and sheets to the required angles, typically up to 90 degrees. This helps form the shape of the tank, and having bends in the corners is generally preferable to welding ends together.
The choice between welding techniques depends on the specific requirements of the tank design and the expertise of the fabricator. Both TIG and MIG welding are commonly used in combination to balance speed and accuracy during the construction process.
Best Boats for Finger Lakes, New York
You may want to see also
Testing and coating
Once the aluminium boat gas tank has been fabricated, it must be tested to ensure it meets the necessary requirements and standards. Testing involves running a pressure test to confirm that the tank does not leak. This is a crucial step, as a leaking fuel tank can have serious consequences.
After the tank passes the pressure test, it may undergo an additional step of coating. Coating the aluminium with a protective polymer layer can further enhance its performance and protect against oxidation, tarnishing, and staining. This coating process can also be done before the tank is assembled, as a pre-treatment to improve the aluminium's resistance to corrosion and degradation.
Customers can also opt to have their tanks coated with a bed liner material for added durability. This extra layer provides an additional barrier against potential damage and helps to ensure the tank's longevity.
The coating process can vary depending on the manufacturer and the specific requirements of the boat owner. Some tanks may also be painted or treated with other protective substances to further enhance their resistance to corrosion and degradation.
Aluminium boat gas tanks are also often constructed with baffles, which help to prevent the fuel from sloshing back and forth. These baffles are internal structures that help to stabilise the fuel and reduce the risk of leakage during rough seas or turbulent conditions.
The final step in the construction process is the installation of the tank into the boat. This involves fitting the tank into the designated space, ensuring all connections are secure, and integrating it with the boat's fuel system.
Sutherland Bayou Boat Ramp: Open or Closed?
You may want to see also
Frequently asked questions
Boat gas tanks are constructed from either steel or aluminium.
Aluminium is used for boat gas tanks because it is lightweight, strong, and anti-corrosive. It can also be easily fabricated and shaped.
Most aluminium boat gas tanks are constructed from 5052 grade aluminium, which is marine grade aluminium.