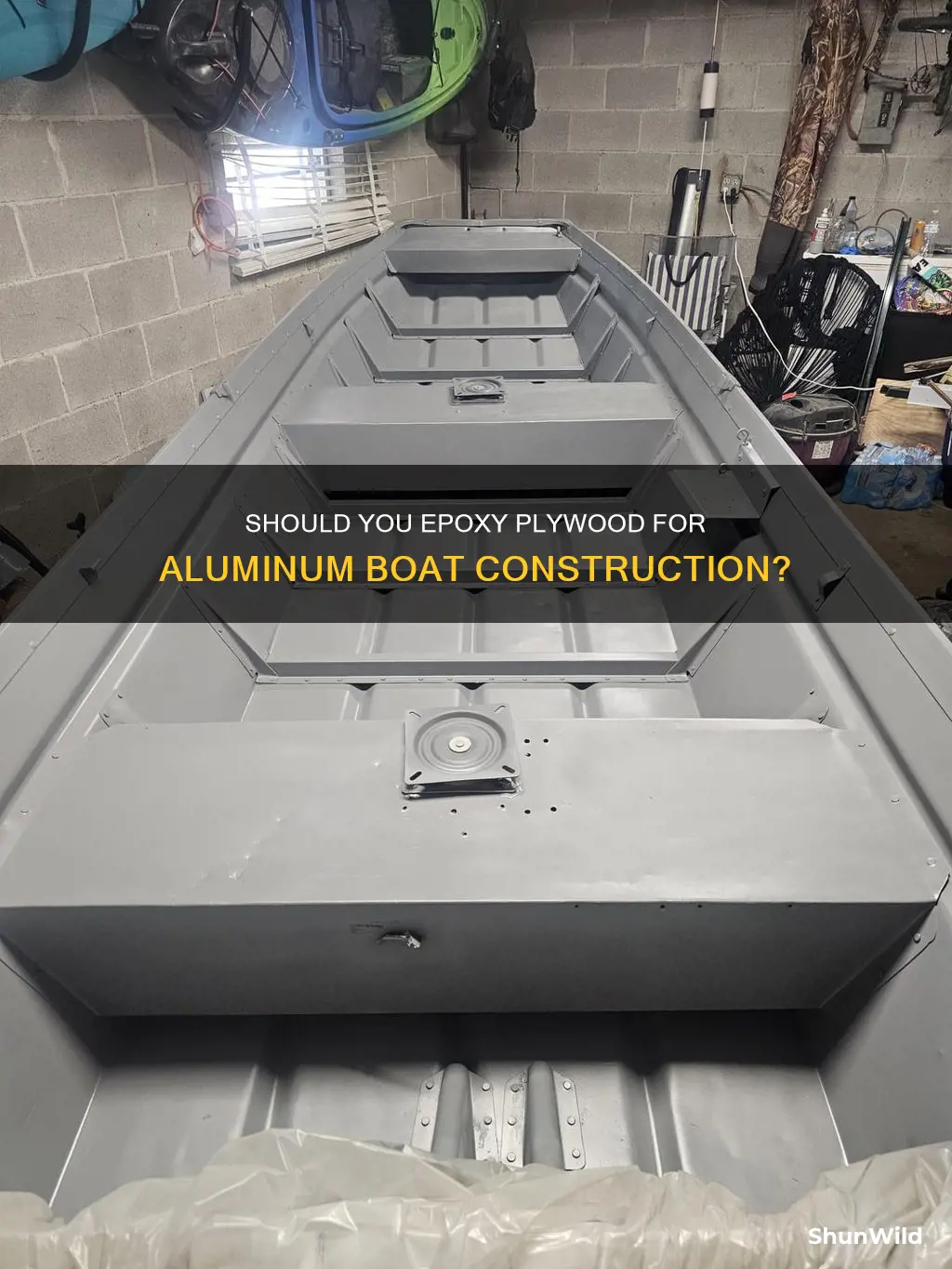
Epoxying plywood for an aluminium boat is a common practice. The process involves coating the plywood with epoxy resin, which can provide a strong and durable finish. However, opinions vary on whether this is necessary. Some people suggest that using exterior-grade plywood and painting it with epoxy resin can be a more cost-effective approach. Others argue that epoxy should be avoided as it does not tolerate UV exposure and suggest using polyester resin instead. Ultimately, the decision depends on factors such as budget, desired durability, and personal preference.
Characteristics | Values |
---|---|
Plywood for an aluminium boat | Exterior grade plywood |
Marine-grade plywood | |
Pressure-treated plywood | |
Epoxy resin | |
Polyester resin | |
Fiberglass cloth | |
Polyester | |
Marine vinyl | |
Marine caulk | |
Marine caulks | |
Penetrating epoxy sealer | |
Topside boat paint | |
Polyurethane primer | |
Polyurethane high-gloss lacquer |
What You'll Learn
Epoxying plywood floors in aluminium boats
When choosing plywood for your boat floor, it is important to select the right type. Marine-grade plywood is ideal, as it is made with waterproof glue and has no voids. Exterior-grade plywood can also be used, but it is important to encapsulate it in epoxy to ensure that it is well-sealed. Pressure-treated plywood should be avoided, as the treatment process leaves the wood with high moisture content, which can affect the strength and bonding of the epoxy.
Before epoxying the plywood, it is crucial to prepare the wood properly. This includes cutting the plywood to size, ensuring that all edges are sealed with epoxy, and allowing the wood to dry completely. It is also important to follow the instructions for mixing and applying the epoxy carefully to ensure a strong bond.
Once the plywood is coated with epoxy, it can be installed in the boat. It is recommended to use a marine-grade adhesive to attach the plywood to the boat's ribs or stringers. Additionally, using foam between the ribs can provide flotation and floor support. After installation, the plywood floor can be covered with marine carpet or vinyl for added protection and comfort.
By following these steps and properly maintaining your boat, you can ensure that your epoxy-coated plywood floor lasts for many years.
Sailing the Valheim Seas: Mastering Boat Navigation
You may want to see also
Using exterior-grade plywood for aluminium boats
When it comes to using exterior-grade plywood for aluminium boats, there are a few important considerations to keep in mind. Firstly, it is crucial to understand the properties of exterior-grade plywood and how it differs from other types of plywood, such as marine-grade. Exterior-grade plywood is typically made of fewer and thicker plies, which can affect its overall strength and stiffness. It is also important to note that exterior-grade plywood may have voids and gaps, which can allow water to sit and cause rot over time.
For this reason, if you choose to use exterior-grade plywood for your aluminium boat, it is essential to seal it properly. One popular method is to use epoxy resin, which can provide a long-lasting barrier against water intrusion. When applying epoxy, be sure to follow the manufacturer's instructions carefully and seal all sides and edges of the plywood. Another option is to use polyester resin, which can also provide effective protection. However, it is important to thin it out to ensure good penetration into the plywood edges.
In addition to sealing, you may also want to consider using tongue-and-groove plywood, which can provide additional support and help prevent deflection. It is also recommended to use construction adhesive when mating the pieces together. Once the resin has cured, you may need to use a primer before applying additional coats. For the finishing touch, you can coat the plywood with tinted polyester and broadcast fine silica on it, using a short-nap roller to bed it in.
When purchasing exterior-grade plywood, look for the grading ABX, BCX, or CDX, which indicates that it is suitable for exterior use. Make sure to avoid pressure-treated plywood, as the chemicals used in the treatment process can react with aluminium and cause corrosion. Always allow the plywood to dry thoroughly before installation, as it may have high moisture content from the treatment process.
By following these guidelines and properly sealing your exterior-grade plywood, you can create a durable and long-lasting floor for your aluminium boat.
The Infamous Vessel: Joe Cool's Deadly Voyage
You may want to see also
Pros and cons of epoxying plywood in boats
Epoxying plywood in boats has its pros and cons.
Pros
- Epoxying plywood in boats can result in long-lasting repairs.
- Epoxying can provide a rigid structure to the boat, making it strong and stiff.
- Epoxying plywood can help protect the wood from water damage and rot.
- Epoxy is a superior adhesive to polyester or vinylester resins, which have weak adhesive qualities.
- Epoxying plywood can reduce maintenance requirements for wooden boats.
Cons
- Epoxying the exterior of a wooden boat can create an impermeable barrier, trapping water inside and leading to dry rot.
- Epoxying plywood may not be suitable for older wooden boats with different designs and construction methods.
- Epoxying can be time-consuming and labour-intensive, especially when applied to large hull areas.
- Epoxying plywood may not be suitable for high-speed boats that experience heavy wave action, as hairline cracks may appear in the epoxy.
- Epoxying plywood can be more expensive than using other types of wood or materials for boat repairs.
Conor McGregor's Luxurious Boat: A Lavish Yacht Tour
You may want to see also
Marine-grade plywood vs. exterior-grade plywood for boats
Marine-grade plywood is made of thin layers of high-quality hardwood held together with waterproof glue. It is water-resistant, lightweight, strong, and virtually defect-free. It is used for wood exposed to a lot of water, including boats and nautical uses, outdoor furniture, decks, and porches. The plywood is either expected to be a show face or a consistent face that can operate as a reliable surface for a decking veneer or fibreglass overlay.
The most significant difference between marine-grade and standard plywood is that marine-grade plywood consists of five layers of high-quality wood adhered with waterproof glue, while regular plywood consists of three layers of wood attached to non-waterproof glue. Marine-grade plywood is stronger due to its water resistance characteristics, higher density, and waterproof glue technique that stands up to delamination or peeling glue.
The standards required by APA- The Engineered Wood Association, for a product to be called "marine grade" are not that much higher than your typical exterior-grade plywood. Exterior-grade plywood is generally B- or C-grade and sanded on one side. It is typically made up of five plies of southern yellow pine with waterproof glue used between the plies. With C-grade plies, voids and gaps are common, and water may sit in them and start to rot the wood.
For boat repair, the use of exterior plywood should be limited to areas where the overall strength of the wood is not critical, and the wood can be encapsulated in epoxy. A motor mount would be a good example; the fibreglass carries most of the load, and the wood will be well sealed.
When it comes to making economical and long-lasting repairs to your boat, using marine-grade or non-pressure-treated exterior-grade plywood and encapsulating the wood in epoxy is a good choice.
Troubleshooting a Locked Boat Engine: Common Culprits
You may want to see also
Plywood alternatives for aluminium boats
Plywood is a common material used in the construction of boats, but there are several alternatives that can be considered for aluminium boats. Here are some options to explore:
- Fiber Cement Board (FCB): FCB is a combination of cement and wooden fibres, providing extra strength, durability, and moisture resistance. It is lightweight, flexible, and suitable for curved surfaces.
- Medium Density Fiberboard (MDF): MDF is made from softwood fibres and wax resin, making it strong, flexible, and moisture-resistant. It is lighter and more cost-efficient than regular timber.
- Birch Plywood: Birch plywood is a suitable option for boat interiors, as it is pure, with minimal chemical additions, and has high strength and durability due to the ring-like composition of birch trees.
- Ribbon Grain Plywood: This type of plywood has an interesting ribbon-like grain pattern and a smooth surface, reducing the need for polishing. It is artificial but resembles real wood and offers good strength and shock resistance.
- Exterior Grade Plywood: This type of plywood is designed for the exterior of boats and can withstand moisture and harsh environments. However, it may require additional polishing and smoothing due to visible defects.
- 3M Reinforced Polyurethane Foam Board: Foam boards are lightweight, rot-resistant, and easy to work with. They come in different densities, with the lightest board weighing 15 pounds per cubic foot.
- Wax Resin Fiberboard: Wax resin fiberboards are strong, lightweight, and highly durable, making them suitable for industrial-grade applications. They are composed of small softwood fibres mixed with wax resin, providing moisture tolerance and reliable strength.
- King Starboard: This high-density polyethylene plywood is an alternative to marine plywood due to its lower cost. It is strong, immune to discolouration, and rot-free.
- Thermo-Lite Boards: Thermo-Lite boards are lightweight, sturdy, rot-free, and non-absorbent, making them suitable for various applications beyond boat construction, such as motor homes and houses.
- Weather and Boil Proof (WBP) Plywood: WBP plywood is designed to withstand harsh temperatures and weather conditions. It uses premium melamine glue and a cross-hatching technique to join the sheets, resulting in a robust, lighter, and more durable material.
- Recycled Plastic Panels: These panels are made from recycled plastic materials and are designed to withstand moisture, rot, and marine environments. They offer similar strength and stability to marine plywood.
- Fiberglass-Reinforced Plastic (FRP) Panels: FRP panels combine fiberglass with plastic resin, creating a strong and water-resistant material suitable for marine use, such as boat building, docks, and other applications.
Bass Boat Financing: Smart Ways to Get Your Dream Boat
You may want to see also
Frequently asked questions
Marine-grade plywood is generally A- or B-grade. The outer ply is an A-grade, and the other side is a B-grade ply. The inner plies should be a B-grade or better. The plywood should be a 7-ply lamination with most plies made from Douglas fir bonded together with waterproof glue.
Epoxying plywood is not strictly necessary, but it is recommended to seal and protect the wood. Epoxying plywood can help to prevent water intrusion and rot, and can also improve the strength and stiffness of the wood.
Plywood with epoxy can provide improved waterproofing, maintenance, and repairability compared to raw wood. It also offers a favourable weight/resistance ratio, resulting in a lighter and more solid boat.